32” LG LCD TV (32 LG 5000-ZA), no starting repair

This set belongs to our building manager who is a good friend of mine.
About one month ago he told me that he had starting problems with it and some days after that he told me again that the trouble disappeared by itself… I answered him right from the first time I heard his complaint about it that his set had problems with its PSU and this will worsen over time no matter if it seemed to be cured by itself.
Well, one week ago he told me again that the set refuses to start at all. He could only see the standby red LED light flashing, but no further change of it in a steady blue color which is a sign that the unit started normally. He brought the set to me and asked me to see what the problem was with it and then repair it. The model number is shown below
I opened the set for a quick optical check and before doing anything else I tried to start it. Its overall internal view is shown below
I saw the same effect: only the red color LEDs flashing at the front panel and nothing more. The PSU this set uses has its big and heavy components on its top side, as you can see below,
and its SMD components at its back side, as shown below:
Then I removed the power and left it for a while waiting for the filter capacitors to discharge. I started then with static measurements on the various power components. No defect found. Also, at least optically, there was no apparent problem with bulged capacitors. Everything was in order.
I removed afterwards the PSU for an extensive check of it. I measured all the semiconductors on it. No defect found. The situation seemed already weird …
I re-connected the unit again on the chassis and tried to start it, using a hair dryer and carefully heating its components. Heating a specific spot, around this big cap shown below, the unit started normally.
I had already tested the electrolytic caps for excessive ESR and I found this cap along with another one being in marginal but nevertheless accepted condition.Anyway I removed the PSU again and replaced them both. The one you see above is the new replacement cap (C512, 100µF/50V).
Then I reconnected the PSU and tried to start the unit again. No result. After reheating it, the test led me to a MOSFET nearby. I happened to have a readily available spare of the same type and thus I replaced it. Then I retried again. The same effect…No starting without the heating aid…
I thought then that I had a problem with some SMD components located exactly on the back side of the PCB, at the spot I was heating it from upside. So I removed the PSU again and tried to resolder all the suspect circuit in that area, removing as much quantity of that problematic lead-free modern solder it had on it as I could and replacing it with ordinary one.
Upon completion I tried it again. This time the result was disappointing indeed… No effect at all. No red light flashing…Absolutely nothing! I rechecked the rework I did using a magnifier lens and searching for possible shorts when resoldering (no matter that I already did this beforehand). No problem at all. All joints were as they should be.
Now what? As usually I had no schematic to go on. I thought to start with the basic information I could get through the web by searching for the relevant data sheets of the SMD ICs used in the back side of this PSU. It was really weird that I lost the standby power supply after my rework on it, having at the same time improved the quality of its solder joints.
After searching in the web I found all the basic info I needed and in order for me not to lose much time for the repair I ordered the three types of ICs this PSU makes use of, to a local shop which sells electronic parts. When I got them I tried to go on with it starting first with the standby supply. The driver IC of this stage, is a NCP 1207A. You can see this stage below
I checked its power supply voltage and I found it O.K but there were no trigger pulses at its output pin to drive the relevant MOSFET. After I replaced it, the stand by power supply was restored and I had back the 5.1V d.c, the 21V d.c for the regulated and switched 15V supplying the rest two I.Cs along with the 16V d.c used for the production of the switched 12V, but nothing else was working.
The situation now was very difficult for me in order to go on without a schematic in my hands. I decided to perform an overall rework on the solder joints… After finishing, checking for shorts and cleaning the PCB with flux removing spray I tried it again. No improvement.
Then I stopped there and searched in the web for a servicing manual. Finally I found a manual which I downloaded and started searching in it in order to find some helpful info.
This ended in another disappointment for me because the only info therein for my case was a simple logic diagram ending with the usual expression “replace the PSU”…There was no PSU schematic in it at all!!! Only parts of it located in the main board, the T-con etc.
I called a friend of mine who owns a repairs’ lab far away from Athens and works officially as an LG service center and asked him if he had something in his mind about this failure. His answer was even more disappointing:“I know that there is no schematic in there” he said. “I am also working without schematics”. And how do you manage the repairs I asked him. The answer was of course as expected…”Don’t bother yourself by performing component level troubleshooting. Replace the PSU. It costs 75€”. Then we stopped the discussion there.
The point is that I had in my hand a PSU unit in perfect condition with all its power components intact and with a mysterious problem which I considered as minor right from the first moment I spent in it.
Once again I was forced to analyze the circuit in order to locate the problem…
I started with the original observation I made, namely that if the standby PSU wouldn’t start, then nothing else could happen as the power supply for the control circuit of the motherboard and the basic 15V d.c supply needed for the rest two I.Cs was coming from the standby supply.
Now I had this voltage of 15V d.c available, but nothing else was working. Having the PSU completely disconnected and removed from the set, I started sketching the switching circuit which energizes the active PFC correction circuit. The circuit is shown below
And the driver I.C of the active PFC stage is shown below:
Following the PCB tracks, I spotted the transistor switch stage for “power on”. So I knew now that if I apply a 5V d.c artificial signal to the base circuit of this transistor by hand, this would equal to the “power on” signal of the main processor. This point on the other hand ends in the connector terminal marked as “power on”.
In the same way, following the PCB traces each time, I spotted the PNP SMD transistor switch (Q103) which had a marking of 2F on it and was responsible for powering the P.F.C stage of the PSU (which rises the voltage after the rectifier filter cap from its 320V of nominal magnitude, to 390V in order for this stage to function correctly). This stage was dead so far.
It’s the one just above the black squared painting shown in the second sequentially photo above, depicting the overall SMD side view of the PSU. Its driver I.C which performs the active P.F.C function is a SG 6961SZ as shown just above.
And the last IC for the switched auxiliary voltages of 24V d.c and 16V d.c for the supply of the display inverters etc (NCP 1396 AG), although it was getting the switched 15V, had no other reaction obviously due to the action of some protection signal, of course when I was testing the PSU before removing it. This I.C is shown below:
So it was a good starting point to begin troubleshooting by searching for the reason that this Q103 couldn’t switch those 15V to energize the PFC stage.
This transistor had its base controlled by an SMD I.C (U101) having the markings E1 on it. One of its terminals was connected to the cathode of one of the four optocouplers of this unit. Based on my experience I realized that this IC was the SMD version of the well known TL 431 used in such cases for regulation purposes. Later on I verified this. It was the same chip indeed.
Now I had all the info I needed in order to go on. You can see this stage below. The U 101 is located at the down-right side (corner) of the photo. It is the last component shown there. The Q103 is located at the same horizontal line of components, at the middle of the picture.
I connected the PSU to the line power having connected in advance a 40W lamp in series with it for safety reasons. I verified again all the available voltages. Then I connected a small piece of cable at one point I was measuring the standby 5V d.c, with its other end free for the moment.
Then I connected my multimeter to the switched 15 V d.c for the operation of the auxiliary supply and giving a “power on” signal to the transistor I spotted beforehand, I saw that I had the voltage output feeding the NCP 1396 I.C. I verified that this voltage reaches the relevant Vcc pin of this chip, but again possibly due to an acting protection signal there was no further function of this I.C.
Then the remaining key question was why that Q103 was not operating at all in order to power the active P.F.C stage. Of course I had already realized that the PSU would work normally only if this stage would be in operation.
Following the sketched circuit I had done, I was measuring the unregulated 21V d.c. supplying the anode of that optocoupler, but at its cathode I was measuring only one volt less which (by experience again) is a very high voltage for a stage like this one. I measured the current through the circuit by measuring the voltage drop across the terminals of the 10KΩ resistor feeding the circuit and measured zero volts.
Then I measured the voltage at the reference terminal of U101, expecting to see 2,5V there. This was also measuring zero volts! Now I had a vital info…
I followed the foil trace and stopped to the point of R109. As you can also see in the above picture the place of this resistor is empty. It is the one at the left side of the grey SMD cap shown in the bottom horizontal line of components, just above the wire bridge J21.
Its lower end was measuring 11,7V, which was also too high in comparison to 2,5V I expected to see there.
I followed the foil trace again and verified the values of all the resistors I saw up to the power supply point where they were finally connected. They were all O.K as shown in the sketch above. Then I decided to bridge the empty terminals of R109, but before doing that I removed the power again and observed this empty place again, using a magnifying lens and supplying a lot of light in this spot. There were visible remains of that red glue which is used in order to hold the SMD components in their place before their hot air soldering during the production process. I checked some other empty places of SMD components and there were no signs of red glue on those. Now I was absolutely sure that a resistor was put there which (inexplicably) was missing now.
According to the sketch I did, this should be a zero Ω bridging resistor, like the rest of them in the circuitry having the marking 000 on them. So I removed a resistor of this type from a salvaged PCB I had and put it there. (The solder remains you will see on the empty terminals of R109 in the above picture are there from the bridging tests I did).
Then I reconnected the PSU to the power line and gave it the artificial “power on” signal. All the missing voltages were now there, the active P.F.C stage started normally rising the voltage at the terminals of the bulk capacitor to 390V and the 11,7V I was measuring previously at the node before the free reference terminal of the U103 dropped now to its normal 2,5V value. The repair was over and the normal operation of this set was restored, as you can see below.
You can also see the defective components I replaced in this PSU unit below,
Then, trying to conclude with this puzzle, connecting all the events together, I remembered again the sayings of the owner of this set when he was telling me that “the TV starts once per each fifty attempts”. Apparently, when this R109 resistor was making a good contact with its connection terminals (depending obviously on the room temperature at the time of trying to start it) the set was starting quite normally. On the contrary, when this good contact was absent, the set could not start and only the standby part of its PSU was in normal operation, trying unsuccessfully to start the set…
What really happened with this set? Here is the sequence of events.
This resistor was so very badly soldered therein that over time the set worked “when it liked to work” as its owner told me…!! During my first rework on this PCB, apparently it dropped from its place and disappeared without myself to notice that event. Besides I didn’t find it anywhere although I searched the entire area very thoroughly for finding it… On the other hand, during my rework I was very careful and focused on the job and didn’t notice any accidental removal of this component when resoldering. I only made two accidental solder shorts which I noticed and removed immediately during the rework process.
Then, after the rework I did and for some unknown to me reason, the standby controller chip suddenly stopped working. Meanwhile this resistor was dropped somewhere, probably during the heating tests I did, and when I finally replaced it the proper function of the unit was restored.
A minor cause indeed, as I originally had estimated during the aforesaid heating tests since the PSU was starting normally by heating it, which nevertheless caused me so much trouble. Anyway it ended in a successful repair which I hope that you also enjoyed reading about it!
After this final verification which was free of any other problems, I reinstalled its top cover closing the unit. The repair was successfully over and this UPS was ready to be put in normal operation again making my good friend Makis very glad with its survival…
This article was prepared for you by Paris Azis from Athens-Greece. He is 59 years old and has more than 30 years’ experience in electronics repairs, both in consumer and industrial electronics. He started as a hobbyist at the age of 12 years and ended his professional carrier as a senior electronics technician. He has been a specialist in the entire range of consumer electronics repairs (: valve radio and BW TV receivers, transistorized color CRT TV, audio amps, reel and cassette tape recorders, telephone answering and telefax devices, electric irons, MW cooking devices e.t.c) working in his early stages at the official service departments of National-Panasonic first and JVC afterwards, at their premises in Athens.
Then he joined the telecoms industry, working for 20 years as field supporting technician in the sector of DMRs (: Digital Microwave Radio transmission stations), ending his carrier with this subject. Now he is a hobbyist again!
Please give a support by clicking on the social buttons below. Your feedback on the post is welcome. Please leave it in the comments.
P.S- If you enjoyed reading this, click here to subscribe to my blog (free subscription). That way, you’ll never miss a post. You can also forward this website link to your friends and colleagues-thanks!
Note: You can check out his previous repair article below:
https://www.jestineyong.com/riello-dialog-plus-70-ups-no-output-repair/


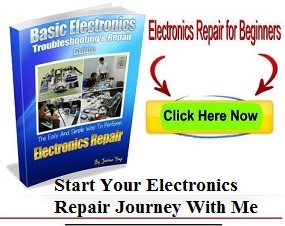
Gary Gemmell
November 20, 2015 at 9:00 am
I often read your articles Paris and admit to being a bit jealous of your skills.
I wish I was as good an electronics engineer as yourself, you really are pretty brilliant (you are my electronics hero lol >;o))- if only all engineers were as clever and inventive as you Paris we wouldnt have so many bad repairs in the industry but i guess your many years of practice gives you the skills you have.
Hope you are doing well in Greece with the current crisis.
Looking forward to your next article already!
Paris Azis
November 21, 2015 at 12:20 am
Hi Gary
First of all thank you for your kind words. I appreciate it and it is really encouraging me.
You don’t need to feel jealous! Electronics’ repairs is a job that of course needs some qualities on the part of the person performing them, but (I believe that) above all the repairer must respect the owner of the apparatus he is repairing. And this respect reflects in treating his/her property in such a way that it not only will bring the apparatus back to life again, but also take care for its longevity.
This last characteristic is the reliability seal on his/her qualitative work as a prerequisite. In other words (with the exception of the necessary existence of technical knowledge about repairs which must always be present) this attitude of mine is exclusively a way of thinking. Nothing less and nothing more.
As I have written somewhere else in this blog about this work subject “if you don’t love it, you ‘ll never conquer it”.
Repairs are many times a chore matter and one must be well prepared and willing in performing such tasks…
Best Regards
g wells
November 20, 2015 at 9:09 am
What i like, just will not give up.
Paris Azis
November 21, 2015 at 12:22 am
Hello g wells
Thank you for your positive comment.
Best Regards
Gregor
November 20, 2015 at 9:52 am
Thanks for posting your story ... I have experienced similar frustrations in repairs ... but it's all worth it when you finally fix something -- that's the reward!
Paris Azis
November 21, 2015 at 12:25 am
Hello Gregor
Thank you too for your kind words. And yes, this feeling is really superb!
Best Regards
Yogesh Panchal
November 20, 2015 at 2:14 pm
Paris,
Good approch and detective work and definitely Passion. thanks for sharing.
Paris Azis
November 21, 2015 at 12:27 am
Passion is a key word! Thank you too Yogesh!
Greetings!
sudhir
November 20, 2015 at 2:42 pm
Hi Paris Azis
I always enjoy and like your post on repair and troubleshooting skills. You are brilliant in your area of work.
please do keep posted your work !!!
Thanks
Paris Azis
November 21, 2015 at 12:28 am
Hello Sudhir
Thank you for your encouraging comment!
Best Regards
Herold Yiga
November 20, 2015 at 5:35 pm
Well ihave no comments but please thanks for your service thank you mach. GOOD-DAY .
Paris Azis
November 21, 2015 at 12:30 am
Hello Herold
Thank you for your kind words!
Best Regards
Rabi
February 14, 2020 at 10:14 am
Hi good work..I have the same concerns even lg black screen blue led. In summary which piece I must change
Albert van Bemmelen
November 20, 2015 at 7:25 pm
Great Job done Paris! A new board at a price of $75 Euros saved, but at the expense of your valuable free time no doubt. You're a good friend to have with your engineering skills!
Reading your impressive repair, I wondered how you figured out that the U101 chip with smd code E1 must be a TL431 zener? Because that code gave all kinds of other components but no TL431. And that component had all sorts of other SMD codes. It does worry me how to keep track of the right SMD code information. I still have components in defect devices that I can't find. And I have looked everywhere without succes! (for instance the SMD code 007F didn't seem to exist for a component in a defect Solar charger?).
Paris Azis
November 21, 2015 at 12:59 am
Hello Albert
It is not only the price of that board that matters. It is really the price of a new TV of similar quality with the defective one. This is the real money the owner saved in this case.
About this E1, as I have also written in the text, I was only based on my experience. The designers of switching power supplies are using it along with an optocoupler almost exclusively in their relevant regulating stages which control the output voltages of their PSUs.
You can find it in the datasheet od “diodes incorporated” as AZ431A, where you will also see the E1A code. Anyway, experience was my guide in this case…
What is this code you refer to? (What component)?
Best Regards
Albert van Bemmelen
November 21, 2015 at 3:52 pm
The SMD component 007F I mentioned was one of 2 unknown components in a Portable Solar Charger (With USB connector) that I was looking for to find its replacements parts. One had a Sot23-5 case and the other had a Sot23-3 case.
But according to your above experience finding the right information from those SMD codes is still almost impossible. Since you found the code in the datasheet you already had of the component in question.
I do have some older (such as Turuta 2011) SMD catalogs but in none of them the wanted Codes are mentioned. And although I also can buy the 2014 Turuta Code Book for 22 Euro, not knowing if these codes will be mentioned in there, prevents me from buying it. So I still have no clue how to find these SMD replacements. And the Manufacturers all handle their own way of Marking.
Paris Azis
November 21, 2015 at 10:37 pm
Albert,
Perhaps you should sketch the circuit around this unknown device as I did. There is always a good chance for you to recognize what kind of function this device does and this recognition could lead you to identify what this tiny thing is.
If I only judge from the device that uses it, it should be either a precision voltage reference or a comparator I.C.
Why don’t you try it? You have nothing to lose! The damage is already there waiting for you…to take care of it…
Good luck anyway!
Greetings
Albert van Bemmelen
November 22, 2015 at 1:28 am
Thanks Paris. I already tried that but it also could be a switching regulator and according to your foundings of the E1 code being only the last characters of chip "AZ431ANATRE1" or equivalent, it is searching for a needle in a haystack. Also because I have 2 unknown components in a very small device that doesn't do anything that would help to give a clue of the defect. But thanks for your input in this matter!
Robert Calk
November 20, 2015 at 7:26 pm
Nice job, Paris. Thanks for the article. Which website did you find that the SMD IC,"E1", is an adjustable precision shunt regulator?
Paris Azis
November 21, 2015 at 1:49 am
Hello Robert
Thank you too for your positive comment. As regards this SMD IC, please take a look in my answer to Albert. I just downloaded some data sheets to confirm that I was right about it when I had my sketch ready and my imagination tachometer in the red zone!
Greetings!
Paris Azis
November 21, 2015 at 10:27 pm
Yes Robert, this is an adjustable shunt regulator.
You can also say that it works as an adjustable (or programable if you prefer) zener diode.
Best Regards
Robert Calk
November 22, 2015 at 12:06 am
Hi Paris,
I was wondering what website you found it on because the website I went to says that a SOT-23-3 IC with the marking "E1" is a NPN transistor.
Paris Azis
November 23, 2015 at 5:22 pm
Hi Robert
I have also visited that site and saw the NPN transistor description, but this could not be the case because if you imagine a NPN transistor in such a connection it would function as an ordinary switch (apart from the fact that the driving current due to those very high resistors would most likely be not enough to saturate it, but again this kind of function was not the one needed in that stage). That’s why I immediately rejected the idea about it to be a NPN transistor.
What’s more, the connection of this (still unknown to me at that moment component) with the incorporated I. R. diode of an optocouler and the fact that it was a three pin component with its one terminal grounded, the other one connected to the cathode of the I.R diode and the last one open due to the missing resistor led me directly to the idea of the SMD form of TL431.
Latter on I simply confirmed my verification by downloading some datasheets and among them I saw that description in the “diodes incorporated” data sheet which closed the circle…
Best Regards
Albert van Bemmelen
November 24, 2015 at 2:31 am
Hi Paris, Just to be sure I bought today the Turuta SMD Codebook 2014 for 22 Euros, with 301.000 codes for active semiconductors: Diodes, Transistors, Thyristors and integrated circuits. And I searched but the E1 is no smd code for a (TL)431 component. (4396 pages !)
Which surely means that your experience and your drawing were very professional. But the printed E1 smd code marking had probably no real value.
Paris Azis
November 24, 2015 at 11:58 pm
Hi Albert
I hope you didn’t buy this catalog only to see if that E1 is included therein because I already feel distressed and even guilty for provoking you to the relevant expense!!…
Apart from that I thank you once again for your warm approval of my methodology when troubleshooting.
Finally experience is of course the best guide in this task, but very unfortunately it needs a lot of working years in order for it first to accumulate in our brains as a vital info and then to be converted or developed to permanent inspiring guidance.
This is exactly what calls for patience (a quality I also didn’t have when I was young as it usually happens) and this is the most difficult but also so important element to be obtained for a person involved in electronics (in general, but especially in the repairs’ field)…
My greetings to you
Albert van Bemmelen
November 26, 2015 at 11:44 pm
Don't worry Paris, I'm just so in to electronics that I need
all the info I can get and therefore I bought the new SMD
Codebook 2014. And the fact that my hobby mainly costs money
is not important. Everything does so why bother. On page 847
I found out that a SOT-23 type ZTLV431 exists with SMD code
S1A - giving 1.24 to 10V +/-0.5% at max also 10mA. On page
2071 I found a TLV431 with SMD code RAA. And on page 541 there
was mentioned a LM431 component with code 3A. And that same
type of component exists as codes: A5 to AA, and also EA1 &
EA2 or as N1A, N1B or N1C. I hope this info helps.
Paris Azis
November 27, 2015 at 7:06 pm
Hi Albert
You don't need to bother about that coding any longer. One way or another this repair is successfully over and ther set working just fine. Besides I was sure about that E1 component right from the moment I saw those 2,5V appearing at its open (reference) pin. And the final test proved that it really was a TL431 in smd form.
So "we are moving forward, to a new (successful) repair"...
Greetings
Henrique J. G. Ulbrich
November 20, 2015 at 7:36 pm
Brilliant, Paris. A lot of patience and perseverance, but anyhow one more mission accomplished. Congratulations. For me just a question remained: as it is not common to me to deal with TV sets, I could not understand what PFC means (the only I now is Power Factor Correction and perfluorocarbon). Anyhow, thanks for the sharing. Go on, all of us really appreciate.
Paris Azis
November 21, 2015 at 1:56 am
Hello Henrique
Thank you for your kind words. Patience and persevearance are key words in this task indeed! As regards your question, it seems that you already know the answer. It's your first (of the two) reference. The Power Factor Correction circuit, not that chemical substance.
Thanks again for your encouragement!
Best Regards
joseph
November 20, 2015 at 8:24 pm
Good work!. The resistor might have droped when you were heating with the hair drier since it was on the other side of the PCB.
Paris Azis
November 21, 2015 at 1:58 am
Hello Joseph
Thank you too for your support. And yes, this is exactly what happened (as I also guess)...
Best Regards
Parasuraman S
November 20, 2015 at 8:45 pm
A Sherlock Homes skill to find fault in the circuit! Hat's off to you! Very informative and valuable inputs! All the best to you!
Paris Azis
November 21, 2015 at 2:03 am
Hello Parasuraman
Thank you for your positive and encouraging comment. I keep in my mind those words of Enrique in his comment above "patience" and "persevearance"...I would also add "love in fixing it" to complete the cyrcle.
Best Regards to you too!
Tom
November 20, 2015 at 10:52 pm
Thank you, Paris! I really enjoyed reading your repair article, even though I am new to the electronics game and didn't understand all the details. I am a retired Metallurgical engineer and I always enjoyed trying to solve difficult problems, just like you do!! Your English is really good and your photos are outstanding. So, this makes you not only a great detective, but also a really good teacher. I will be looking for more of your articles as I try to learn about electronics. Once again, thank you!
Tom in Indiana.
p.s. Could you tell us about your camera and photo setup please? Thanks!
Paris Azis
November 21, 2015 at 5:08 pm
Hello Tom
It is nice to meet you here, in this blog. Perhaps I will learn something about Metallurgy from you! So, welcome into the (really magic) world of electronics.
I enjoyed myself being in this journey since my childhood and for almost forty years up to now as a professional…And I still keep on enjoying it…It was “love at the first sight” to me and hopefully you will love it too!
Best Regards
Paris Azis
November 21, 2015 at 5:38 pm
Hello Tom
As regards the photos, they are taken with my Panasonic FT30 compact camera which is capable of macro shooting. This was a gift from my daughter who is studying photography and she knew my problem to macro shoot with my cell phone camera…
Best Regards
Tom
November 23, 2015 at 12:10 am
Thank you, Paris, for the camera info.
Tom.
Paris Azis
November 23, 2015 at 5:24 pm
You are welcome Tom!
Greetings
Suranga Electronics Sri Lanka
November 20, 2015 at 11:12 pm
Best Repair Mr. Thanks for your Article. I Like this Repair.
Paris Azis
November 21, 2015 at 4:45 pm
Hello Suranga
Thank you for your support.
Greetings
Paris Azis
November 21, 2015 at 1:43 am
Hello Jestine
Will you please remove the last paragrapg, just before my photo, in the text above? It belongs to my previous repair article and it is irrelevant here..
Thank you in advance
henry
November 21, 2015 at 2:10 am
It is only determination that can give this kind of success, i really understood
how you felt seeing that the set is no longer in the condition it came. you are good i must confess
henry
Paris Azis
November 21, 2015 at 4:59 pm
I agree Henry!
Thank you for your positive comment.
Best Regards
henry nyeche
November 21, 2015 at 2:19 am
Good one i know how you felt when the set can no longer be in condition it came, and is only determination that give such result
henry
thanh
November 21, 2015 at 2:46 am
i think the first thing you should do is count how much the led blinked in each section. the number of blink show what is the problem so you can fix it much easier. good post
Paris Azis
November 21, 2015 at 4:57 pm
Hello Thanh
Thank you for your comment. Unfortunately the display red light was permanently flashing and it seems that this is no indication of anything.
According to the manual, the main processor in such a case sends three “power on” signals attempting to start the set and afterwards stops with the flashing being permanent…
Greetings
Anthony
November 21, 2015 at 3:57 am
Hi Paris,
Great determination and skill to beat this "tough dog" repair when most would have simply replaced the power supply
altogether ! It's always a pleasure reading your articles and seeing the steps you take to resolve a problem. Thank you again for sharing your experiences with us here.
Best Regards
Paris Azis
November 21, 2015 at 4:52 pm
Hello Anthony
Thank you for your kind words.
Best Regards
Gerald Millward
November 21, 2015 at 5:26 pm
Fantastic job Paris! Your friend is indeed fortunate; a technician trying to earn his living could not possibly afford to spend so much time on a repair.!
As a matter of interest, one of the penalties of being a fan like me of hot air rework stations rather than a soldering iron, is that a rework station heats the area around the component you are removing. Because of the tiny components and tight packing it is extremely easy to accidently remove or displace one of the others in this area on the same or other side of the board. This is the "hair dryer" effect you found. However, in using a hot air rework station you become very concious of this possibility and check carefully after each component removal that you haven't accidentally moved or lost any other.
Paris Azis
November 21, 2015 at 10:20 pm
Hello Gerald
Thank you too for your kind words. Moreover I will take more seriously into account your advice about working with hot air blow in suspect PCB areas…
Well, I know that a professional would not dedicate so much time for a repair like this. I have been myself a professional for many years in the past and therefore I am in position to understand this simple fact. Nevertheless, even at that time of “earning the means for our everyday living” I was doing such repairs after a proper agreement with my customer of not pressing me about the delivery time. Then, at a time when things were calm enough as regards the number of incoming defective equipment to be repaired, I was keeping on with such repairs.
Anyway I have admitted elsewhere in this bog, that I cannot resist attempting a repair no matter how difficult or obviously time consuming it might be. Since an age of technical maturity of mine things were working quite differently than before in my mind. The easy cases of failures were frustrating me without giving me the pleasure I had with them at my early years. I refer to worn belts’ replacement in video tape recorders as an example. On the contrary, the difficult failures, especially when they were pure electronic instead of mechanical ones and particularly those which could have an overdose of mystery in their appearance were (and are) my favorites.
I believe that I still learn electronics from the failures themselves…And somehow I feel that I still need this, as it at least offers me a lot of pleasure.
Best Regards
Robert Calk
November 22, 2015 at 12:31 am
I use a small tip on mine with high heat and the air about 30%, keeping the nozzle close to the solder joints, and rarely have problems. It also helps to keep the PCB from getting too hot.
Roop
November 21, 2015 at 6:28 pm
Fantastic. Keep up the good work.You are certainly an inspiration to me and now I know that one must never give up, regardless.
South Africa
Paris Azis
November 21, 2015 at 9:45 pm
Hello Roop
Thank you for your supporting comment.
Best Regards
peter O
November 22, 2015 at 10:40 am
As is plain from the numerous acknowledgments; this repair was a "tour de force" in the display of tenacity, competence & vast experience.
I genuinely doubt that most electronic repairers could have completed this without resorting a "a new PSU".
Hat off to you, you are indeed a marvel, & thanks for the very complete description of the repair.
Paris Azis
November 23, 2015 at 6:33 pm
Hi Peter O
Thank you for your very kind and encouraging comment.
However my purpose when writing all these articles is not to exhibit technical superiority against any other person involved in electronics’ repairs, especially against the other writers of this blog who expose themselves in public criticism in equal terms to these of mine.
My purpose instead is to offer enthusiasm to likely newcomers in this field, as in one hand I recognize the fact that repairs are rapidly diminishing due to many factors which makes it not possible for me to analyze them here for the time being and on the other hand I somehow feel that if we (the old and perhaps last Mohicans…) given that we are already very few all over the world (in this blog we seem to be like a family now…) then this knowledge of ours should not vanish. Somehow I feel that we must leave at least some of our experience to help the young generation to stand on their own feet…
Now let me please rephrase those three key words you already put in your comment: “tenacity”, “competence”, “experience”.
“Tenacity” should always be there as a permanent motivating factor (after our proper self-estimation of our qualities and skills). Overestimation (=arrogance) of repair’ skills could easily bring sudden death and equal effect can also happen with underestimation of the circumstances which is equal to blind stubbornness.
Over time, “tenacity” (as above) will bring with it “experience” (=not only technical wealth but also solid bases of personal wisdom) and this in turn will bring “competence” (= capability to withstand defeats and win battles in our everyday living and securing finally our survival in this life through personal excellence).
This is the proper sequence in arranging the order of these three key words, as I humbly think, or, at least, this is my point of view about it…
All the best for you!
humberto
November 24, 2015 at 1:34 am
Good repair Paris. Congrats. and keep up.
Paris Azis
November 24, 2015 at 7:57 pm
Thanks a lot Humberto.
Greetings!
Dennis Breda
January 16, 2016 at 2:59 am
You are very tenacious. Great report.
Paris Azis
March 25, 2016 at 2:18 am
Hello Dennis
Thank you for your kind words. Please excuse my delay to answer you...
Best Regards
Posian
June 25, 2016 at 7:44 pm
Hello Paris! I read your post because I think I have the same problem with same model tv; but in this case R109 is in place and it is 4701 marked, wich is 4k7 ohms (I also check it with the multimeter); could it be possible to be bad contact on this resistor or it could be something else? The tv takes the start command (the red led is blinking) but the image in not appearing; only after some good trying (10-15x) the image appear. (I am not a proffesional electronist)
Anyhow it is hard to say without checking all, I know, in fact what I want to ask is how to be sure that the problem is not just from the bad soldering of R109, if from measuring it shows the right value?
Thank you, and great info!
Paris Azis
February 21, 2019 at 5:12 am
Hello Posian
I have revisited this article after a long time since you put your comment. Although it seems meaningless now, after so long time, perhaps there is still a chance of survival of that set of yours (if not thrown away). I think that the problem is in one or more dried electrolytic capacitors. So do a thorough ESR testing of all of these, especially in the power supply and the inverters pcb for the back light of the screen. I hope that it is not too late for that set.
Makis Karag
July 22, 2019 at 10:20 pm
Hello,
I think this is the schematic of the PSU if anyone needs it.
https://www.electronica-pt.com/esquema/lcd/lg-lcd-08h-3237-rev2.0-eay40504401-eay40505001-crb31131901-crb31189601-26365/
Steve
April 3, 2020 at 11:13 pm
Thank you very much for detailed info, I have here the same board with no power from the pin's apart from the 5 volts, I have stand buy LED flash 3 times then extinguish, I have changed the caps but dont have that little 8 leg IC, I will try and get one to see if I can get my TV up and working again, does that I start the unit, wake up the system?
Thanks