Battery Problem In Head Lamp Retrofitted
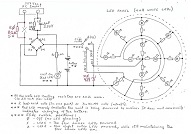
DEVICE: Head lamp
MAKE AND MODEL: FIX Model FXL722B
COMPLAINT REPORTED: All dead (no LED glowing)
TROUBLESHOOTING AND RETROFIT DONE: This is my own head lamp, rarely used.
Most of the time it is stored in a cabinet inside my wardrobe. I have another that is always in my car´s trunk. Prior to open the unit I put it under charge by connecting it to the wall outlet. After a charge period longer than normal, tried again. Nothing — No LED glowing.
Opened the set by loosening the four Philips screws. There was no need to clean, as the device was neat. No need to solder patches also. And the most important: this device has no electrolytic capacitors!
The head lamp is composed of five parts: the AC receptacle for charging from mains, a small printed circuit board, the switch to control the power to the LEDs, the LED panel and the battery.
A measurement on the battery showed no voltage. The battery didn’t show any indication regarding manufacturer, model, chemical type, voltage, country of manufacturing and so on. Nothing written in the involucre. No connectors – the two wires were soldered directly to the two battery terminals. All this posing a typical example of a bad quality product.
After desoldering, a closer look suggested that it was a lead-acid battery. In order to confirm this, I took the other device from my car´s trunk (that is the same make and model – both were bought the same day and in the same shop). A recharge had been done recently and it was working normally. After opening it, I measured the voltage, which showed a value near 4 V, suggesting a two-cell lead-acid battery (rated 2 V per cell). This battery also didn’t show any identification.
At this time I remembered that I have an emergency lamp also with problems, using the same type of battery. This emergency lamp was left in a drawer for a long time. Opened it and bingo! Not only was the same type, but also had all the necessary identification. It was really a lead-acid type, and in this case had a logo from the manufacturer, type (VRLA – lead-acid) and rates (4 V, 1.1 Ah), as can be seen below:
The next action was to get a new battery. It showed impossible. Such a kind of battery simply does not exist in my city´s local commerce. Not even in my whole country (Brazil). An Internet search revealed that this type of battery is a whitefly, even abroad. As a result, this leads to discarding not only the battery, but all the device itself. This is not fair: the lifetime of the device is just the life time of the battery! Just comparing: it seems to be the same when you buy a new car and when the gas tank becomes empty you discard the whole car! Of course this shows that China is not worried about environment nor to provide really good products. A perfect case of planned obsolescence. But not for me and for the most of technicians and engineers that follow this Jestine Yong´s site. Saving the most possible from the junk is a must.
The idea is to replace by another type of rechargeable battery, and the natural choice is Ni-Mh. I ordered four Ni-Mh cells and two battery holders for 2 cells each. Each cell is rated 1.2 V and 1800 mAh. In each cell it says “Charge in 15 hours”. Obviously, this is not a reliable information, since the charging time of any cell or battery is dependent on the charging device characteristics and on the C-rating (for information on the C-rating one can visit https://quadquestions.com/blog/2014/12/27/qav250-c-rating-explained/ or http://batteryuniversity.com/learn/article/what_is_the_c_rate). In order to achieve full charge in 15 hours, the value of C must be 120 mA (0.067C). However, each charger has its own regime and the charging time is ultimately dependent on the current provided by the charger.
The nominal voltage for a Ni-Mh cell is 1.2 V. So, four 1.2 V cells totals 4.8 V, which is 20% more than the original design value (4 V) of the head lamp. To make matters worse, a fully charged Ni-Mh cell presents 1.4 V, leading to a total voltage of 5.6 V. Obviously all four cells couldn´t be used, at the risk of the LEDs being oversupplied. Hence using three cells a rated voltage of 3.6 V (4.2 V when fully charged) is obtained, values in keeping with the original specification based on lead-acid supply (4 Volt nominal).
After a simple adaptation (taking an intermediate wire tap in one of the battery holders) I came to the setup shown below (so replacing the original lead-acid battery by the three Ni-Mh shown):
This was a provisional setup aiming at testing only. At the end of the work the wires were shortened and correctly arranged inside the box, in the name of security.
In order to estimate the charging time for this specific case, it´s necessary to know two things: the charging current provided by the head lamp circuit and the mAh ratings of the Ni-Mh cells acquired. The circuit was surveyed (reverse engineering) and showed to be as below:
It is an ordinary circuit generally used in these applications. A transformerless (economical) power supply charges the battery after rectification by the bridge rectifier composed of D1 to D4 (the type of diodes was not identified– must be basically 1N4007 or equivalent). Two components do not take part of the original circuit: the 82 Ω resistor RØ and the 4,7 V zener diode, both drawn in red color — see IMPROVEMENTS below). It is somewhat difficult to estimate the charging current based on this circuit diagram. It needs some calculations, that I´m not going to do now. This arrangement woks in practice as a voltage divider with two parts: the voltage reducer composed basically of the capacitive reactance of C1 (R1 serves only to discharge C1 after disconnecting from the wall outlet) and the battery itself. The diode bridge between them is not part of this divider, serving only to rectify the AC voltage. The characteristics of the battery guarantee that the voltage on it remains low, with its charge occurring in a circuit like a constant current circuit based on the reactance of the capacitor. With this, the voltage applied to slide switch remains the battery voltage, to be applied to the LEDs. The LED panel consists of 12 LEDs arranged in two sets: an inner set of 4 LEDs and an outer set of 8 LEDs. The slide switch has 3 positions: in the OFF position, no current is sent to the LED panel. In the position 1 (intermediary) only the four inner LEDs are powered (LED 1 line). This is done in order to preserve the charge of the battery along the time of use, since there are occasions in that not much light is needed. With this, the charge of the battery lasts more time. In the position 2 (LED 2 line), the eight outer LEDs are powered, while still maintaining the four inner LEDs supplied due to the special arrangement on the slide switch. This is the maximum light power, therefore with maximum current consumption. There is a problem at this point: If the battery is disconnected for any reason (by opening one or the two of their connecting wires or removing at least one cell), the voltage divider no longer exists and practically the AC input is almost entirety applied to the slide switch. If at this moment the switch is moved to power the LEDs, these LEDs can burn immediately…. This inadvertently happened to me with the group of four LEDs in the beginning of the maintenance work, which lead me to add a protection zener diode after replacing these four LEDs (see IMPROVEMENTS below). For my luck, the switch was not moved to position 2, otherwise all 12 LEDs might be burnt.
The LED (red emission) at left of the battery in the diagram always shines when the unit is connected to AC. One could think that it indicates the charging status, what is not necessarily true.
As the calculation of the charging current based on the circuit diagram is somewhat complicated, the solution was to simply directly measure the charging current. The connection in the intermediary point (between the two battery holders) was open and my veteran analog multimeter was placed in, which showed a charging current of about 44 mA. As the cell rate is 1800 mAh, it was easy to calculate the charging time: about 40 hours, in this case a value of C = 0.025.
After 40 hours charging, I disconnected the unit from AC and initiated the basic test. The device worked, i.e., LEDs shining. I started the autonomy testing sliding the switch to Position 1, which powered the four inner LEDs. In this condition, the voltage on the charged battery measured initially 3.8 V. The current measured was almost 100 mA (my veteran analog multitester again). In order to determine more precisely the current consumption, I carried out voltage measurements on the 4 LEDs powered in the LED panel, at this time with a precise Fluke digital meter. The voltage on 3 LEDs measured 3.0 V plus 0.8 V in the associated 33 Ω resistor. The fourth LED measured 3.1 V plus 0.7 V in the associated 33 Ω resistor. All coherent. In any case, measurements compatible with the battery voltage. The calculations showed that each LED was draining about 23 mA (92 mA total, against the somewhat inaccurate measurement near 100 mA from my analog multitester) Anyhow, I understand that by design this current could be somewhat lower, bringing about high duration of the battery charge and lowering the regime of the LEDs, thereby assuring their long useful life.
From time to time I monitored the voltage in the three cells, taking into account that when the discharge point occurs in this type of cell, the voltage decreases quickly. When the discharge test completed 9 hours and 30 minutes the voltage testing on the cells showed that one of them reached the discharge condition, going down to 0.2 V. Perhaps this condition lasted for some time (not detected). Obviously the other two cells, still with 1.2 V, were also quickly going to the discharge point too. Even so, the LEDs continued to glow at an acceptable light power. Even changing the slide switch to the position 2 all 12 LEDs continue shining, although with noticeable reduced brightness. With this, I conclude that the autonomy with only 4 LEDs powered is about 9 hours. It seems good, however in theory it must be about 18 to 19 hours, taking into consideration the informed capacity of each cell (1800 mAh) and the current drawn (23 mA each LED). Perhaps the battery was not full charged in the beginning of the test. I´ve not checked the autonomy with all the 12 LEDs, but this is easy to carry out approximately by calculation (a rule of three).
IMPROVEMENTS: Two refinements were implemented: The first one was to add a 82 Ω resistor in the AC input circuit (RØ shown in red color in the circuit diagram). This resistor protects the circuit from inrush currents at power on. It was installed in one side of the box, near the mains connector. Two holes were done in the plastic in order to mechanically fix the resistor.
I´ve read somewhere that it can act as a fuse. This certainly is not a professional approach…
The second refinement was to add a 4.7 V zener diode between the LED 1 line of the slide switch and the Common point (ZØ, also shown in red in the circuit diagram). This zener diode was installed on the LEDs printed circuit on the LEDs panel.
This is done to protect the LEDs in the case the slide switch is moved to one of the positions that powers the LEDs with AC input applied and the battery is disconnected for some reason. The zener guarantees that the voltage to the LEDs are kept at a safe value, protecting them against burning.
Final notes:
1) A good thing in this case is that each LED has a current limiting resistor. In poor products, these resistors are not used, with the LEDs connected directly to the low impedance of the battery, which can bring about high currents through the LEDs, shortening their useful life;
2) I decided to use two separate battery holders because I had doubts if a battery holder for 4 cells could fit inside the case – two separate battery holders could be best to accommodate. Afterwards I found out that this showed itself to be a correct decision;
3) All the retrofit mentioned above was carried out in the model FXL722B from my own. The experience acquired was used to do the same work in another head lamp from my son “Beto”: Model LED-AZ495 from AZPR also with the same battery problem. It is a device with basically the same building solutions and the same circuit diagram, also with 12 LEDs.
4) I suspect that the battery from head lamp in my car´s trunk is also going soon to reach the end of its useful life, as it was purchased in the same day. So, according to the experience acquired, my next action will be to preventively do the same work on it;
5) For those who intend to carry out similar retrofit in their own headlamps, I remember that the same basic concepts are applied to emergency lamps (obviously with LEDs, not with fluorescent lamps – in this latter case, the basic idea can be applied with some modifications). It is very common that these emergency lamps don´t have limiting resistors for the LEDs. Therefore, a good opportunity to implement them.
6) For the wording of this report (mainly in the initial part) I adopted part of the style used by our friend Parasuraman Subramanian. It´s a very practical and technical report style. The only change was to put each picture next to the respective text. Thanks, Parasuraman.
This article was prepared for you by Henrique Jorge Guimarães Ulbrich from Curitiba, Brazil. Retired telecommunication and electronics technician. Loves electronics, telecommunications, cars, wines and grand children.
Please give a support by clicking on the social buttons below. Your feedback on the post is welcome. Please leave it in the comments.
P.S- If you enjoyed reading this, click here to subscribe to my blog (free subscription). That way, you’ll never miss a post. You can also forward this website link to your friends and colleagues-thanks!
Note: You can read his previous article below:
https://jestineyong.com/a-bad-hv-capacitor-in-a-microwave-oven/


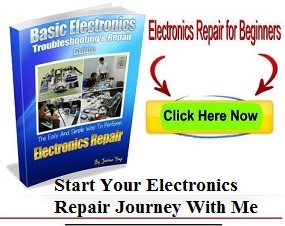
Albert van Bemmelen
October 15, 2020 at 6:26 pm
Nice article Henrique Jorge! About the 4.7V zenerdiode you used it probably is important to use a high wattage type (the 1-1.5Watt types exist). And instead of the old NiMh cells you also could have used Li-ion 18650 or other fitting cells. Battery holders for those are available too. With an extra Li-ion charger adapter board the output can be set to exactly 4V and this way also the Li-ion overvoltage protection is guaranteed. See this one:
Empty Li-ion cells are about 3.7V and 4.2V fully charged. So ideal for this led light. And they easily are 2000mAh or higher, and certainly much better than the original lead-acid battery.
Henrique J. G. Ulbrich
October 16, 2020 at 12:21 am
Thanks a lot for your comments, Albert. About the zener diode you are correct. I carried out in this way as I didn´t have in hands a more robust diode. However I thinked in two things: 1) The power dissipation can be improved by adding a transistor associated with the LED (which I didn´t do yet), and 2) The worst to happen is the zener becomes shorted-out, which is quite suitable, as it works in this case as a crowbar circuit, effectivelly protecting the LEDs. Better to replace one cheap diode than 12 LEDs……
About the use of Li-ion, you are right. I´d really considered this when I was planning to do this retrofit. An extremely sound proposal. It could be so, with success too and with the advantages you pointed out. The link you suggested is quite valid. As I have yet an emergency lamp to retrofit in sequence (mentioned in the article), there is a strong possibility I use your suggestion. More experience ahead!!!! And perhaps another article for this Jestine Yong´s site.
Parasuraman S
October 15, 2020 at 6:27 pm
Vow! So much on service of a head lamp! It shows I know very little about the function and principles of its working! Good to learn a lot, especially when it comes from professionals like you! Many thanks for sharing this vast knowledge!
Henrique J. G. Ulbrich
October 16, 2020 at 12:33 am
Thanks for your comments, Parasuraman. I always have a concern in adding a didactic explanation of how a circuit works. For this purpose, I generally carry out a reverse engineering, tracing all the circuit and drawing it. That's the reason why the drawing is so ugly, as done with my hands. Even so, an activity like this takes some hours... but enough to address the didactic purpose. Thanks for your encouraging words.
Imoudu Onwumah
October 15, 2020 at 6:32 pm
Wow! This's a genus layout context repair.It's only gurus like you can do this.Thanks for the share.
Henrique J. G. Ulbrich
October 16, 2020 at 12:44 am
Thanks for your comments, Imoudu. However I am not genius, just a man that thinks that all one is going to do must be well done. In my case, as a retired man, I have time to spend in searching the subject in internet and also spend more time in preparing the tracing of the circuit. However, I am aware of the fact that, when one has a repair shop, it is not possible to spend so much time in a repair. Many thanks for your post.
Humberto
October 16, 2020 at 11:00 am
Good solution implemented by you Sir. Congratulations.
Henrique J. G. Ulbrich
October 17, 2020 at 8:19 am
Muchas gracias por sus observaciones. Saludos.
Thanks for your comments. Greetings.
Mikael Hansen
October 16, 2020 at 10:16 pm
New NiMh cells often need a few charge-discharge cycles too reach full capacity.
Henrique J. G. Ulbrich
October 17, 2020 at 8:16 am
Right, Mikael. Perhaps this is the reason why I achieved only 9 hours of autonomy. It was just the first test. I´ll take care of this. Thanks
Paris Azis
October 17, 2020 at 2:53 pm
Hello Henrique
This was a real "Research & Development" article. Fully detailed in every aspect.
If your intention is to use NiMH cells I propose to you the Eneloop type produced by Panasonic. (It was invented by Sanyo, which has been bought by Panasonic and Panasonic kept the original marketing name Sanyo had given to this product).
They are designed to have very low leakage current, which means that once you charge them fully,they remain 80% charged after one year of no use. I think that this is ideal for the use you make with this head light. (I am not paid to advertise these batteries. Simply I am using them permanently and I know what I am saying about them).
The LiIon type looks better, but it is intended for everyday charge discharge cycles. If you store it either fully charged or discharged it deteriorates with time. These cells need to be stored (I.e. Not used for long time) having only 75% of their full capacity, which is difficult to achieve every time before storing them without using special instruments or sophisticated chargers. (I personally use the Turnigy Accucel 6 in its "storage" mode for this task).
The second proposal to you is to use higher current in order to reduce the existing long charging time within logical limits (I.e.7 hours, or 10 max.). In order to do so, you need to recalculate the capacitance of the input capacitor (practically to increase its capacitance), but keep in mind that above 100mA of output current these transformerless P.S.Us are not the best preference...
You need therefore to select another solution.
Thanks for sharing your experience!
Henrique J. G. Ulbrich
October 18, 2020 at 12:25 am
Thanks for your comments and suggestions. I´ll investigate these new options. However, one must take into consideration the availability and mainly the cost of this solution. An expensive solution for a cheap product doesn´t match well. Regarding to using higher currents to charge I agree, provided that the battery doesn´t be "uncomfortable" with the treatment... Surely you added a good contribution to the subject. Thanks again.