Do It Yourselves (DIY) AC Extension Box

Time and again, one or other tools as well as the facilities that we have in our workshop fail, putting our service work to jeopardy. Such a thing happened, when one of the Chinese Made extension boxes short circuited and started burning inside. Luckily, this happened when I was not away. I disconnected the input power, removed the loads and took the box outside the house and left it there until there was no more burning or smoke. Left it there overnight. Now an immediate need arose to get a replacement. But the replacement box, if bought from the open market also will be of such inferior quality. I have had a lot of collections in the junk and did not want to add one more! Just see one bag full of such boxes:
There are around 10 of such boxes, because of failure of the switches, plug, cord or surge protection circuits, or cable faults. That’s why I decided to make one of my own. I am sharing this experience here for novices and not for experts, for whom, this might be nothing!
Here is the list of things I gathered before venturing into this project: 1. Readily available switch box, which can accommodate four female plugs and its switches on the sides. 2. Female three pin 5A sockets, 3. Four 5A Switches, 4. Four Small size Red emitting clear LEDs (I chose clear LED, as it goes well with the white background) , 5. Three Meters 15A Cable (Chose 15A because there are four sockets and the load might be more, when all are switched on simultaneously. The required length of the cable should be decided first, before cutting it!) 6. One 15A 3 pin top, (I used a 6A male plug as I was not having 15A, and shall replace it with the proper one later. Before selecting a 15A, ensure that there is a 15A outlet on the wall!) 7. Four 100K 2W Resistors, 8. Four IN4007 Diodes, 9. Lengths of Red, Black and Green wires (please read article to know how to measure the length) and 10. One Rubber Bush. [Tested the Switches, LEDs and Diodes using Analogue Multimeter so that we do not end up in removing and replacing the defectives, if any found later! Similarly, checked that all screws on the plugs and switches were correctly getting tightened and there were no manufacturing defects.)
Removed the plug sockets and switches from its covers and kept all in a box in front of me, along with its screws that come with each. Fixed the sockets and switches on the top portion of the box, one by one, taking care that the switches and sockets are in perfect order and are uniformly facing in one direction. The difference in color of the switch (ivory) and socket (white) was purposely selected for easy view of the switch by its contrast. I arranged in such a way that I have the switches on the left and plugs on the right sides. The switches can be brought to the right side, if we fit the plugs and switches the other way.
As you will notice, I had fixed two sockets of international type and two sockets of Indian type.
As per standards, the phase (Line/live/hot) should be on the right, neutral on the left and earth on the top, and the switch should be on the input of the Line (live AC), when viewed from the top. The switch should NEVER be in series to the Neutral, because the device connected will be then live even when the switch is in off position, and the return live wire can cause accidental lethal shocks through the Device. Moreover, this might consume energy though to a small extent, especially when the weather is moist. The device will be at greater risks of damage by lightning etc. as the live line will be floating inside.
The next step was to drill holes just under the switch to insert the LED from behind. I took my small drilling machine (first picture below), and fit a suitable size drill bit matching the diameter of the top portion of the LED, so that the LED fits in snugly and tight enough. Drilled four holes under the switches, measuring its position, marking it so that they are fit uniformly. Drilled a large hole to insert the bush (Kindly see the picture of the bottom portion in the second row of pictures in this article), on the right side of the bottom box (I selected the right side, as the connection to the mains was on that side). The top portion can also be fit appropriately later, without bothering about this, provided the holes for fitting screws of the top portion are evenly placed on both sides. In this box, since this is a machine made one, the holes of the fixing screws were perfectly aligned, and we could tilt the top portion in any direction we want, before connecting the cable later.)
The drill bit I used for the large hole was from the set of wood drills, picture of which is at the last above. I used No.12, which was matching the cable size and used my power drill for this purpose.
While inserting the LED, I ensured that the anodes of LEDs were facing uniformly to the Line side. Now, coming on the subject of whether to use the diode or not or do we require a 2 W resistor etc. I followed the method, which I have found successful for a long life of the LED, from my practical experience. I studied many discussions on this subject in the web, but found the following matches with my experience:
https://www.instructables.com/id/LED-on-AC-Mains/
Started the wiring inside, taking up the common connections of Line, Neutral and Earth. In order not to clog the sockets with multiple wire ends, I took the correct length of each wire, Red for Line, Black for Neutral and Green for Earth, by placing the wire on top of the rear side of the sockets and switches bending it the way it should be wired. This method is to cut the wire to the required length beforehand, and to avoid the difficulty of handling loose wire or coil of the unused portion.
Removed the sleeve at only the place where the screw has to make contact. For this, first adjust the wire cutter to the correct size, just cut the insulation, use a player, hold it using the notched portion (please see second picture above), and slide the insulation to one side. Repeat the process until there is just enough room for making the contact. You may have to run the player gently but firmly until the end of the wire, to slide the insulation. Remove the screw, slide the wire through the hole until the bear portion of the wire is just in position, and then tighten the screw.
Now, that was possible, where the wire goes through the hole. But what will we do when such hole is not there? Just bend the exposed wire and using the player, twist it to bring it to proper size for insertion. The method is more or less same as explained earlier, but we have to pull the insulation to one side more making provision for the bend, i.e., double the length. Did the same thing for Earth and Neutral wires too.
While wiring the switches, I ensured that the hot wire passes through the idle portion of the switch when in off position, i.e., when the switch is in off position, the spring loaded contact inside the switch rests on the top portion and when pressed, comes in contact with the bottom. The series connection of the Live wire should be on the bottom pins of the switches.
Inserted one end of the 100K resistor to the Neutral, and cathode of the Diode to phase (line) and tightened the screws well. Soldered the other ends to the LEDs and cut short the protruding leads. Kept the exposed portions away to a safe limit.
Made an incision on the outer insulation of the cable at a measured place, by adjusting the wire cutter and exposed the three wires inside for final connection to the Box as well as to the Male Plug Top. This incision should be so precise not to cut or puncture the wires inside the cable. Then connected these to the respective pins, phase, neutral and earth. We should remember to insert the cable hold on the male plug top, place it in position, and tighten the cable holding screws, before fixing the wires to pins.
Using analogue Multimeter, and putting it in x1 position, tested the plug pins and ensured that these were properly connected to the board. Operated the switch on and off to make sure that these were also properly wired.
Finally, here is it, the Box is ready at-last, after a lot of ‘labour’ pains, cuts and bruises on my fingers!
I made two such boxes, one for my workshop and one for my living room. While the first one took a very long time to make, the second was done swiftly!
We can add a fuse or MCB in the box, if needed. I did not do it, because I have these in the isolation transformer itself.
Added this also to my ever growing ‘satisfaction list’, and heaved a sigh of relief!
This article was prepared for you by Parasuraman Subramanian from India. He is 69 years old and has more than 30 years’ experience in handling antique equipment like Valve Radio, Amps, Reel Tape Recorders and currently studying latest tech-classes conducted by Kerala State Electronics Technicians’ Association. He has done graduation in BBA degree, private diploma in Radio Engineering and retired as MD of a USA company. Presently working as Consultant to Hospital and other institutions.
Please give a support by clicking on the social buttons below. Your feedback on the post is welcome. Please leave it in the comments.
P.S-If you enjoyed reading this, click here to subscribe to my blog (free subscription). That way, you’ll never miss a post. You can also forward this website link to your friends and colleagues-thanks!
You may check on his previous repair article below:
https://jestineyong.com/servicing-christmas-light/


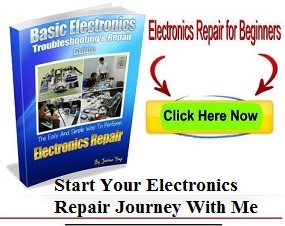
Albert van Bemmelen
September 4, 2018 at 9:34 pm
Good job! Having the 'repair room' at order is mandatory for good servicing! I myself placed a third power extension box (Belkin Powersurge) on the wall behind my TV yesterday. They together now contain about 23 Power 230VAC plugs, Power adapters and more extenders. And a couple more of those Power protectors I placed in my electronics repair room. Included in my living room is Oversurge protection for LAN cable, Telephone Line, and Coax cable. And I switch those all off with one Powerknob if I go to sleep or in case of lightning. I live in a Flat/building with many neighbours and when they are struck by lightning I take no chances. It has happened in the other building that all appliances were struck through the TV ground cable which functions as a conducting HV Bobine cable.
R MURALI
September 4, 2018 at 10:11 pm
Thank You Sir for guiding the proper way of making Extension Board.Very happy to read your Technical Guidance and Article.
Henrique Jorge Guimarães Ulbrich
September 6, 2018 at 12:43 am
Very good, Parasuraman. I have two comments: 1) I agree with the bad quality of Chinese products. I also prefer to build my own (and operative) solutions like you. 2) Your solution was aimed at Indian patterns. But just slight modifications will provide the same idea to any other country pattern, taking advantage of your good work.
Humberto
September 7, 2018 at 11:36 pm
A very good article. Nice photos.
Justice
September 13, 2018 at 8:18 pm
You put a smile on our faces ,Thank you .Interesting.
Claude
October 9, 2018 at 1:15 pm
Good simple explanations; Though very simple and common, will help beginners to do it the right way. Thank you, Mr.Subramaniun for your time in preparing this article.