Terminals Found In Reverse Order Of A Defective Transistor In A Rust Ruined TCL Induction Cooker

This IC (shortly referred to for Induction Cooker) belonged to one of my relatives and was brought with a request to see whether it can be brought back to life. The complaint was that it was getting on, but goes off quickly. This was not used for quite a long time, perhaps waiting for a chance to come to me! (LOL)
On opening, I was shocked to see such a lot of rust, dust, cockroach eggs and marks left on this once cockroach infested board. But I could not see a single living one. Looks like they too abandoned the site for want of food!
As you can see, the boards were fully ruined by cockroaches; especially the panel board was totally spoiled. You can also see fungus attack. What surprised me was how the cooker turned on when I tried before opening to confirm the complaint! The last picture above is after I brushed the board clean, but before using IPA. You can see rusted transistors with one of its legs detached! This part actually handles the pulse for the gate of the IGBT and will get on only after uController IC (Highway 08) gets startup clearance. You can also see fungus formation in the 20-PIN IC socket. Since it was evident that the primary supply was still functional as the main IC was getting on, I decided to go ahead with the marathon work of restoration. I cleaned the main board thoroughly using IPA and brushed every part and made it as clean as could be.
Replaced all the 8050 and one 8550 transistors, though a couple of them could have been reused as the legs got cleaned well. (This was a good decision, which can be seen why, later in this article!) Changed all the electrolytic capacitors and ceramic capacitors. The ceramic capacitors were also way out of its values, which you can see later in the pictures. Lifted one leg of all resistors that cannot be checked on board and checked its value. Replaced those which showed higher values. Replaced the 18V Zener. Replaced the IC socket. Then stripped of every component from the panel, including the jumper wires. Cleaned the board thoroughly using IPA and brushed it thoroughly. As the boards were having the value of components printed, I removed each one ensuring that the value is same as in the board. I took several snaps of this bare board before cleaning, so as to ensure that I had this information in case any of these prints get erased in the process. Almost all the components were rusted, including the LEDS. So replaced every one of them, including the jumper wires. Since I was not having the three digit seven segment LED display, tried to get one but in vain. So, I dug out the remaining tip of the broken pin just deep enough to solder a thin wire, as a special leg and fixed the display. Resoldered the SMD IC TM1628 (Display controller).
As fungus formation was noticed in the socket/jack of the panel connecting strip, replaced it with a Five Pin male socket (Out of the 10 pins, only the first five pins were used in the board) and then replanted the solder lugs to the new wires.
I took care and ensured that the wires are in proper place, by checking and cross checking the connections before removing these terminal lugs.
I repeated my cleaning of the boards and completed retouch of all soldering points on the main board. I even removed the SMPS transformer to clean the bottom portion. I provided a good 8 PIN socket too.
Then connected the boards. As I had already removed the IGBT for testing, I just powered the board without the coil. But the fan was not starting up, upon which I tried applying a little bit of oil, but in vain; so I replaced it. Then found that all functions were working well, showing the E0 error for not sensing the Induction load. A couple of portions of the second digit of the segment were not lighting up. But we could read the display.
So, disconnected and assembled the boards and fixed all except the panel. Kept the ceramic top and took the IC to the kitchen for a trial, before which I removed our Impex Induction cooker from the kitchen, remembering the earlier incident. (Caution – Never Keep One Induction Cooker On Another For Testing – A Lesson Learnt | Electronics Repair And Technology News (jestineyong.com) Kept a pot of water and started it up. It worked well and the water got boiled quickly. By default, the IC starts at 2000W, which can be reduced to our desired level, by pressing the (-) down button.
Switched off and brought it back to my workshop and fixed the panel also this time and then put only two screws of the bottom and brought it back for further trials at-least for a period of three days or more. The cooker worked very well for the last two days and I do not envisage any problems.
Now comes a twist in this IC story as mentioned in the caption as well as elsewhere. Out of curiosity, I checked a few of the removed components which looked ok after cleaning. First let me give the pictures of two fixed caps that showed out of range readings:
Then checked the 8050 and 8550 transistors. To my surprise, in one of the 8050, the Peak Atlas showed the terminals on the reverse; i.e., C, B, E instead of E, B, C and further there was a leakage current too. The HFE also was shown, but very low! See pictures below:
Well, I have absolutely no idea why and this is my first experience in the entire electronics service career! Perhaps eminent professionals would throw some light on this!
Here is the final picture of the components replaced, before which I conclude this article stating loudly and proudly “SATISFACTION GOT ADDED TO ITS COLLECTION BAG!”
This article was prepared for you by Parasuraman Subramanian from India. He is 71 years old and has more than 30 years’ experience in handling antique equipment like Valve Radio, Amps, Reel Tape Recorders and currently studying latest tech-classes conducted by Kerala State Electronics Technicians’ Association. He has done graduation in BBA degree, private diploma in Radio Engineering and retired as MD of a USA company. Presently working as Consultant to Hospital and other institutions.
Please give a support by clicking on the social buttons below. Your feedback on the post is welcome. Please leave it in the comments.
P.S-If you enjoyed reading this, click here to subscribe to my blog (free subscription). That way, you’ll never miss a post. You can also forward this website link to your friends and colleagues-thanks!
You may check on his previous repair article below:
https://jestineyong.com/restored-a-tampered-keyboard-and-made-a-kid-very-happy/


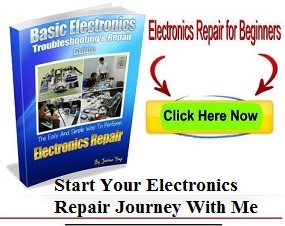
Gassan Ali
January 28, 2021 at 12:51 pm
Behold! Parasuruman unleashed his powers upon the poor induction cooker and it had no choice but to heal.
Parasuraman S
January 28, 2021 at 6:47 pm
Many thanks! Your comments are very encouraging!
Albert van Bemmelen
January 28, 2021 at 2:33 pm
Incredible done job! No words that can describe this well carried out 'massive' repair! About testing the transistors with the PEAK Atlas tester, I experienced a similar strange result when I tested a good E13005. At first the Atlas tester showed me a PNP transistor as result which obvious was wrong. And then when I re-tested it, it showed an 15 HFE NPN as result which was fine! So these testers go wrong once in a while!
Parasuraman S
January 28, 2021 at 6:49 pm
Many thanks for your comments and experience shared!
Albert van Bemmelen
January 28, 2021 at 8:45 pm
Because I often use several digital testers it also could have given a wrong result on one of my other testers. It is probably caused by measuring on those special HV transistors that usually have a very low HFE factor. Or in case of the 8050 example given in the article also caused by a low HFE of only 21.
Parasuraman S
January 28, 2021 at 10:47 pm
Yes, very true!
Yogesh Panchal
January 28, 2021 at 4:18 pm
Good job! Sir,
I think every country should ban some material for the use of particular purpose now a days more & more electronic components are made using cheap iron metal which get rusted most early instead of using Copper.at least sack of environment so that less material is go to ground fill.
Now a days i found LED/diode/Capacitors/IC's even connectors body like for USB port and many more are made of cheap iron Metal which get rusty very early in some environment. you can not reuse this material in electronics after the cleaning.
Though it hardly make economical difference of cent or two for manufacturer and while customer is ready to pay for the quality.
I think still 70% peoples are never mind to use the equipment till it fulfill their purpose by getting the equipment repaired instead of buying new.
As a technicians we only need to stop using this type of material and demanding good material from the market.
Parasuraman S
January 28, 2021 at 6:51 pm
You are very correct! Unfortunately, the buyers like us have no choice! The suppliers are united in all these quality matters!
Henrique J. G. Ulbrich
January 28, 2021 at 10:31 pm
I´d never found a problem with reverse terminals in components. It´s a surprise for me. On the other hand, I´ve encountered many components with rusted terminals. Poor quality! Anyhow, a beautiful work - greetings. An "almost condemned" device was brought again to life. Thanks for sharing
Parasuraman S
January 30, 2021 at 6:20 am
Many thanks for your encouragement!
Imoudu Onwumah
January 29, 2021 at 4:56 am
Good job as usual.Well, induction cooker is not common ever here,I've not seen one before.We use conventional "hot plate". Which of the two is energy conserving.Just for the asking!
Parasuraman S
January 30, 2021 at 6:21 am
It depends on power consumption rating, and also types of uses!
Gregory Brettell
February 6, 2021 at 7:51 am
Great work ... I think a lot of people would have given on repairing this item. Cheers!
Parasuraman S
February 7, 2021 at 10:18 pm
Many thanks!