Flasher Can Repair
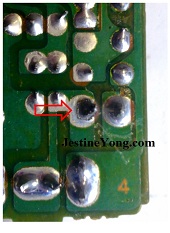
While working as an Automotive lecturer for TAFESA here in Australia, one of my students brought in a flasher can, which is used as a timed relay to activate the indicators on a car. He had replaced it at work as it had an intermittent problem and decided to bring it to class to see if we could diagnose the fault. Here is what we discovered.
Before getting down to checking the electronics on the board, we checked the relay side of the component. The coil had an acceptable amount of resistance. The contact points were not pitted and had good continuity when closed.
I then had a bit of a visual inspection, but couldn’t really find any obvious fault. It was nearing the end of the day, so I took the flasher can home for a closer inspection. When placed under my LED magnifying lens, the fault became obvious. Further testing proved my diagnosis.
A cold solder joint had developed at the output terminal of the switch points. This had created an intermittent fault that became apparent when the component heated up.
I returned to class the next day and showed the students what I had discovered. I had one of the students resolder the joint and then test the unit. We were able to connect a series of lights to load the system and then let it run for 10 minutes or so to confirm the success of the repair. This became a good teaching lesson for the class and the apprentice was able to take the flasher can back to work and show his employer.
This fault created a good opportunity to create a lesson developed on fault, cause and repair.
This article was prepared for you by Mark Rabone from Australia.
Please give a support by clicking on the social buttons below. Your feedback on the post is welcome. Please leave it in the comments.
P.S- Do you know of any your friends who would benefit from this content that you are reading now? If so, forward this website to your friends or you can invite your friends to subscribe to my newsletter for free in this Link.


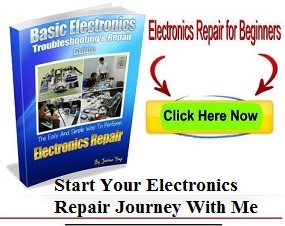
Yogesh Panchal
October 27, 2014 at 3:22 pm
Good job Mr. Mark Rabone and thanks for sharing.
Robert
October 27, 2014 at 3:28 pm
Thanks for the article Mark. I'm sure your students will remember to check for bad solder joints now.
Amir Mukhtar
February 7, 2015 at 7:06 pm
Thanks you Mr. Mark Rabone to Sharing Learnable article.
Sometimes DRY Joints became reason to device dead. However, Good JOB.
Thanks you for Article
Amir Mukhtar AShrafi
Robert Calk
February 7, 2015 at 11:26 pm
In my experience, bad solder joints/soldering is the main cause for device failure.