GQ-A305D Bench Power Supply Repaired
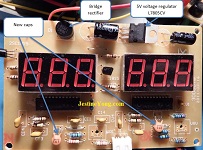
I bought this GQ Variable DC Power Supply, and when I went to test it I found out that it didn’t work! The power supply is a +/- 0-30V with 0-5A constant current and constant voltage, and coarse & fine adjustments. The voltage display would show the voltage, but I wasn’t getting any current. There wasn’t even enough current from it to light a LED.
GQ offered to exchange it, but didn’t offer to pay the shipping. I told them that I was tired of paying to send back defective devices. So I decided to try to fix it myself because I was sure that the transformer and relays were good. I figured that if I couldn’t fix it, I would rather junk it for parts than pay $20 or so to ship it back to them.
They were sure that the problem was somewhere in the Control board where the main front Pot’s are. So that board is the only board they would give me a schematic of. I figured that the problem was on the Mainboard, but they wouldn’t give me the schematic for it; and later started ignoring my emails. But they at least gave me that schematic. I can’t give you guys the schematic because I gave my word that I wouldn’t give away the schematics if they gave them to me.
I found a lot of bad solder joints and problems with this unit. And each time I fixed one problem, I found another. I nearly gave up on it. In fact, I did shelve it for several weeks. But I couldn’t give up completely because I knew I had a good transformer, relays, and main components. I checked the wiring also and they seemed to be good except for bad solder joints.
There were dry solder joints and problems galore! I removed the bent over cap and it checked to be good. The -15V regulator L7915CV had bad solder joints and when I removed the solder, a track lifted. So I had to solder a wire to make the connection. I had my Hakko 808 de-soldering gun on number 1 and still lifted that track and I also lifted a track on the Op-amp on the Control board. It was my fault that I had to replace the Op-amp because my probe slipped while I was doing voltage checks on it, which shorted it out. I was afraid the PCB’s were junk, but thankfully those were the only tracks that lifted on me until I got to the Display PCB.
While I was waiting for my trimmer resistors and components to get here, I decided to go over the boards again; and look what I found! A bad wire connection that I had previously missed! The wire comes from the emitter of the main NPN power transistor 2DS1047 that is on the big archaic heat sink in front of the fan. It was only hanging on by a couple of strands! Before, I was turning the unit around and checking for bad connections in the wiring. This time I just lifted the main PCB up and over and looked down from a different angle and found the bad connection. This is probably my main problem of not getting current! I’ll have to remember in the future to always check PCB’s from all angles.
After I found that bad connection, I found more. The wiring looks cheap and they seem to be old and brittle. So I’ve decided to just replace them all with new wire. I didn’t have any good 16 gauge 105⁰C wire, so I ordered some stranded red, black, and yellow spools. My new wire has 26 strands, rated for 600V & 15 A. It should be very dependable and handle the 5 Amps the unit can provide very easily.
Here are a couple close-up pictures of 2 more of the bad wires.
My control board is finished, cleaned, and ready to be installed.
The schematic says that VR1 should be 2.2K. But since the PCB is marked for it to be a 5K trim resistor, I installed a 5K. VR1 goes to the course adjustment POT for the Amps.
I ordered my NTE WH6 series wire from Radio Shack online. The wire I remove from this unit will go straight into the trash. Hopefully when I’m finished I’ll at least have a usable bench power supply.
I replaced the heavy wiring with some good wire and I still have no current. So I’m thinking now that maybe I have a problem on the Display PCB. I checked some of the components on it before, but not all of them.
When I checked a 200Ω resistor that goes to a pin on the current LED display on board, it checked open! When I checked the 200Ω resistor on board that goes to the same pin on the voltage LED display, it checked to be good! When I removed the resistor that checked to be bad, it checked good. So maybe my current LED display is bad? They are not very expensive, so I ordered some.
I removed or lifted a lead and checked every resistor and cap on the Display PCB. All of the resistors were good. One 10nF ceramic cap (103) was reading 15nF. It and the other 103 cap are very tiny. I went ahead and replaced them both with larger new 103 caps. The non-leaded solder really looks bad – I hate it.
This is the first time I’ve had to worry about a LED display, and I’ll admit that I’ve never even looked at the datasheet of one. I asked Mr. Yong about it and he gave me some help and a good link to go to. It’s nice having someone like Mr. Yong who is always eager and available to help – thanks Mr. Yong! I don’t see how he has the time to do everything he does. He must be a master of time management!
So I re-soldered everything back with some good leaded solder and re-wired the lifted tracks better. I also soldered the current LED display back and decided to see what happens. Hurray – I have current!!
I have a working power supply now! I think the bad diode in the LED display is making it hard for me to get the unit adjusted very well. When my new 0.56” 3 digit 7 segment LED displays get here, I will install one and see if I can get it to adjust better – but for now at least I can use it. I am happy that I finally got the unit repaired! It was time consuming, but I learned a lot. And I also get the satisfaction of a job well done. I also know that the power supply will be much more efficient and dependable now that I fixed a lot of bad soldering and replaced the main current carrying wires. The whole wires are actually soldered in – not just a few strands of them! I’m sure the power factor of the unit is much better now.
I hope you guys enjoyed this repair. Please give any comments or suggestions you have below. Thanks.
This article was written by Robert Calk Jr. He is an Electronics Hobbyist and loves learning electronics and device repair.
Please give a support by clicking on the social buttons below. Your feedback on the post is welcome. Please leave it in the comments.
P.S- Do you know of any your friends who would benefit from this content that you are reading now? If so, forward this website to your friends or you can invite your friends to subscribe to my newsletter for free in this Link.


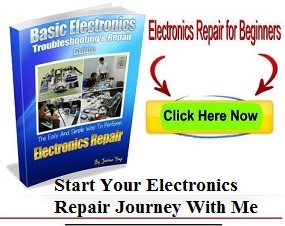
Memo
February 2, 2015 at 2:17 pm
Nice article. Thanks for sharing.
Robert Calk
February 2, 2015 at 2:43 pm
Thanks Memo. You are welcome.
Amir Mukhtar
February 2, 2015 at 4:43 pm
Nice Work
Keep Sharing Expertise
Amir Mukhtar
Robert Calk
February 3, 2015 at 4:20 am
Thanks Amir, I will.
Troy Woody
February 4, 2015 at 1:12 pm
Loved the article, and others you have posted. Got a few of Jestine's books. Just got a degree in electronics and these article are a huge help in applying what I learned to the real world. I bought this same unit, but luckily mine works great. Hopefully I never have to open it up. LOL.
Thanks again and keep up the great work.
Troy
Robert Calk
February 4, 2015 at 9:19 pm
Thanks Troy. Yes, some on youtube got units that worked also. Some times bad products slip through the cracks.
If I were you, I would at least open it up and check the high current wiring, but only if you have a de-soldering gun. The quality of the PCB's are not very good, and if you un-solder the wires and components the old fashioned way, you might lift every solder pad.
Troy Woody
February 5, 2015 at 6:29 am
well I spoke to soon. LOL. I went to shop today and went to use this and no current. I took it apart and sure enough it is the one of the worst soldering jobs ive seen. my prob seems to be the IC chip S3F945BZZ-DK94. My chip tester recognizes it and gave out 2 errors.
Robert Calk
February 5, 2015 at 9:59 am
I hate to hear that. My unit is analog. What kind of tester do you have?
Owais Akhter
June 14, 2020 at 11:48 pm
I have the same power supply which has 4 to 5 milliamps out in display when I switch into milliamps mode. But quite accurate in Ampare mode. Could you please mention which variable I should adjust to reach at nearest value on display?I have checked milliamps value connected with my Fluke 87-V and it's showing 12mA but power supply display shows 8mA only in mA mode switch.
Yogesh Panchal
February 2, 2015 at 2:18 pm
Excellent work Mr.Robert please keep do sharing.
Robert Calk
February 2, 2015 at 3:27 pm
Thank you my friend. I will share all that I can. I appreciate you sharing with us as well!
moshe
February 2, 2015 at 3:08 pm
VERY nice piece..thanks for sharing...i also had a problem with a bench power supply (an ATTEN) that ended up being a shorted mosfet - but i couldn't get a schematic out of them. Fortunatey mine is a dual supply so i could compare against the good side.
Robert Calk
February 2, 2015 at 3:32 pm
Thanks Moshe. Yes, it is much easier when we have schematics. At least they gave me the control board schematic, so it helped. Anyway, the unit is more dependable now since I upgraded most of the soldering and high current wiring. Plus it was good to gain the experience.
Biruk aweke
February 2, 2015 at 3:29 pm
Hi Mr.robert very nice repair thanks for sharing Biruk from ethiopia.
Robert Calk
February 2, 2015 at 6:05 pm
Thanks Biruk, I'm glad you liked it.
Dave
February 2, 2015 at 3:54 pm
Great article. I certainly learned where NOT to buy equipment. Thanks
Robert Calk
February 2, 2015 at 6:09 pm
Thanks Dave. The unit was very cheap. I really can't believe they can sell them so cheap. I watched a couple of reviews on youtube and the unit they received worked. Maybe it's a good thing it didn't work so I could replace the wiring and make it safer.
Jayant Gholba
February 2, 2015 at 4:20 pm
Don't you think all electronic engineers should black list GQ Electronics for bad workmanship?
Robert Calk
February 2, 2015 at 6:33 pm
I don't know, maybe mine was just a bad one that slipped through the cracks. The main components seem to be good parts. People on youtube seemed to get good units, or that at least worked. From now on I'll save my money and buy a used Rigol or something on ebay.
Gerald
February 2, 2015 at 4:27 pm
Hi Robert,
Whaoow, what a journey. Wonderful article and repair. I hope that you sent them the link for this article. You might get a job as a quality control engineer in their factory as they dearly need a good one...:)
Well done, congratulations and thanks for sharing.
Cheers,
Gerald
Robert Calk
February 2, 2015 at 6:44 pm
Thanks Gerald. I doubt that they would care. I gained some experience anyway. And the unit should be safer now.
Amir Mukhtar
February 2, 2015 at 4:45 pm
Thanks you Mr. Robert Calk Jr. To Sharing Details of Variable Power Supply Repairing.
Good Job and Thanks also, goes to Sir jestine for BLOG Facility.
Thanks you
A Student of Electronics
Amir Mukhtar Ashrafi
Robert Calk
February 3, 2015 at 4:25 am
You are welcome Amir. I'm glad also that Mr. Yong has this website where we can share our experience. He is very helpful and generous with his time.
Ajaz jee
February 2, 2015 at 5:21 pm
Good
Robert Calk
February 3, 2015 at 4:26 am
Thanks Ajaz.
Gerald Millward
February 2, 2015 at 5:45 pm
Robert - Your determination and thoroughness is an example to us all!
Robert Calk
February 3, 2015 at 4:27 am
Thanks Gerald. You are very kind.
Nobby Forster
February 2, 2015 at 6:29 pm
Well done Robert. For a hobbyist, you are super.
I wished you lived near by, I would be at your door every day.
Best Wishes for the future.
Robert Calk
February 3, 2015 at 4:29 am
Thanks Nobby. I appreciate that.
Mark
February 2, 2015 at 6:57 pm
Hey Robert,
How many times were you tempted to throw the unit in the bin? These sort of repairs are very draining, but the feeling you get when it finally works far outweighs the trials. At least you know you have a reliable power supply, not like the one that you bought!
Keep up the good work!
Robert Calk
February 3, 2015 at 4:35 am
Thanks Mark. I wasn't tempted to bin it, but I was tempted to put it in the spare parts box. I'm very happy that I got it working. As it turned out, the current display is ok. It had a bad solder joint either on the display pin or the resistor lead because it works great now and the 200 Ohm resistor checks good now on-board like the other one. That non-leaded solder is just worthless!
Mark
February 2, 2015 at 7:15 pm
Robert,
Good job. I'm confused on one point: the 200 ohm resistor for current display check "open" installed, "good" on bench. Why would you suspect display bad, since you were testing across resistor?
Robert Calk
February 3, 2015 at 4:38 am
Because the 200 Ohm resistor that goes to the same pin on the voltage display checked good on-board. It turned out to be another bad solder joint. The resistor checks good on-board now since I put some good solder on it.
Paulo Brites
February 2, 2015 at 7:23 pm
Excelent description of problem (a lot of them) At the end of journey you get a new power supply constructed.
I would like to translate your article e publish in my site (www.paulobrites.com.br) here in Brasil giving you and Mr.Jestine all credits of course.
It could be an alert for people buying things from non well known trends.
Congratulations for your precisious explanation.
Cheer
Paulo Brites
Robert Calk
February 3, 2015 at 4:44 am
Thanks Paulo. I hope the people in Brazil will enjoy it. Other people have received working units from them so hopefully not many people will get units with the problems that mine had.
Robert
February 2, 2015 at 8:00 pm
Wow Robert - you're an inspiration! I hope the manufacturers of this sub-standard PSU have seen your article and are now hanging their heads in shame.......but probably not eh? Congratulations on bringing it to life. King regards
Robert (Liverpool UK)
Robert Calk
February 3, 2015 at 4:47 am
Thanks Robert. I appreciate that. Hopefully my article will help other people repair their unit if they received one that didn't work.
Thommas
February 2, 2015 at 8:26 pm
Hi, great info.
I have a video cassette /dvd player,that when I plug it there no power at all.
Any help?
Thanks.
Robert Calk
February 3, 2015 at 4:54 am
Thanks Thommas. Bad solder joints are a big problem now since most manufacturers are using non-leaded solder. If you have checked the fuse and usual suspects, I would just re-solder every component and connection on the primary side with some good leaded solder and see if that gets the unit working. Use latex or nylon gloves when soldering with leaded solder and then wash your hands when finished.
Pepper
February 2, 2015 at 8:27 pm
Mr Calk,
It would appear that persistence is the secret to your success!?
GOOD job!
About lead-free solder; I hate it too. Seems like every solder joint
appears to be `cold'(dull appearance)! In fact, it is rather hard to
de-solder lead-free (maybe a higher melting point?) What I have done is
add a little leaded solder to a joint and the `solder wick'pulls it right up!
Lastly, I can't say enough good things about Mr. Yong! He has (and will)
helped so many - thanks...
Robert Calk
February 3, 2015 at 5:04 am
Thanks Pepper. You are correct. I'm glad I have my Hakko 808 to remove the bad solder with - it really makes life so much easier. They are worth their weight in gold, I really mean that!
I agree, Mr. Yong is a blessing! He is so generous with his time and he really does help people that asks him.
Bernie Scott
February 2, 2015 at 8:29 pm
Wow!!! Good job there man....You should charge the company for repairing their sub-standard equipment....I for one will not buy any of their equipment...I don't have the time to repair equipment that I purchase from companies when it arrives DOA....I don't think these companies would appreciate it if I sold them something that didn't work....I buy all my test gear locally and I buy it used....
Cheers,
Bernie
Robert Calk
February 3, 2015 at 5:11 am
Thanks Bernie. If I did charge them it would be more than I paid for the unit! lol
But to be fair, it does have some good components in it. And the transformer looks like a very good transformer. Whoever put this unit together was probably having a bad day.
tim
February 2, 2015 at 10:06 pm
Thank you for the informative article and step through on repairing the power supply. I have always wondered how the low initial cost DC PS compare to a 30 year old Beckman Industries that cost about 10x in price (back then). Having repaired a BK1660, I can now see the difference.
Great job, keep it up!
Robert Calk
February 3, 2015 at 10:05 am
Thanks Tim. I just bought this unit to power IC's and devices to test them. It is not suited for anything requiring high precision. I think it was only $75 US. But of course we do at least expect it to work.
Amendar
February 2, 2015 at 10:44 pm
Good job, thanx for sharing.
Robert Calk
February 3, 2015 at 10:06 am
Thanks Amendar. You are welcome.
Amendar
February 2, 2015 at 11:03 pm
Was it a used, or a new one.
A kind of cheating, a faulty device with tons of mistake in assembling,....
A cheap design, component and workout, not acceptable from so called COMPANY!
Robert Calk
February 3, 2015 at 10:10 am
It was supposed to be brand new. You can't expect top quality in cheap equipment, but they should at least work.
Humberto
February 3, 2015 at 12:40 am
Hi Robert, good article. Congratulations
Robert Calk
February 3, 2015 at 10:12 am
Thanks Humberto. I'm glad you liked it.
Luis Estrada
February 3, 2015 at 12:46 am
Stick-to-itiveness is one of the characteristics a good troubleshooter has and you certainly have it. Mr. Yong has often spoken about it. Good for you! Wish you the best.
Robert Calk
February 3, 2015 at 10:15 am
Thanks Luis. I appreciate that. Since the transformer and main components were good, I knew it was just a matter of time before I got it to working. I just had to find and fix all of the problems.
Andre Gopee
February 3, 2015 at 2:16 am
Wow what a lot of work going into that power supply... It seem frustrating doing all that work on a simple power supply. You have a lot of patience my friend. |Job well done. Thanks for sharing.
Robert Calk
February 3, 2015 at 10:19 am
Thanks Andre. Since I'm a Hobbyist I had time to spend on it. It sat on my table too long. I can't work on stuff all day like I used to.
Bart
February 3, 2015 at 4:22 am
Great Job and very informative article
Best wishes
Bart
Robert Calk
February 3, 2015 at 10:19 am
Thanks Bart.
mahmoud
February 3, 2015 at 6:06 am
dear Robert congoratulate for repairing the dc power supply.i think this bad power supply made by china therefore don,t tired.
Robert Calk
February 3, 2015 at 10:21 am
Thanks Mahmoud. I think it was supposed to be made in the USA if I remember right.
Waleed Rishmawi
February 3, 2015 at 2:22 pm
I appreciate your attitude in this repair. If I were you, I would send it back and claim my money back. a lot of work seems like went into this repair but your came on top. thanks for sharing this repair information. I have learned a lot from this article. thanks man friend. keep up the good work. you are no longer a hobbyist my friend, you are a pro.
Robert Calk
February 3, 2015 at 2:50 pm
Thanks Waleed. I appreciate the kind words. It would have cost me $20 or so to send it back because they didn't offer to pay the shipping. I was not going to do that. Anyway it worked out and I gained some experience.
Anthony
February 3, 2015 at 3:46 pm
Great work Robert, and the beautiful photos really do convey the very repair tedious job that lay ahead of you !
Perseverance really did yield a reward here and it does show that it does pay dividends !
Really great work and a fantastic outcome !
Regards
Anthony
Robert Calk
February 3, 2015 at 11:34 pm
Thanks Anthony. Yes we must have patience to persevere those tough dog repairs.
TAUFK LASKAR
February 3, 2015 at 8:08 pm
very nice sir,
it is amazing post.
Robert Calk
February 4, 2015 at 9:31 pm
Thanks Taufk. Your comment is appreciated.
Marulitua Hutabarat
February 4, 2015 at 10:32 am
Hi Robert.
Very nice article and complicated work.
Thank you to share.
Robert Calk
February 4, 2015 at 9:54 pm
You are very welcome Marulitua. I take pictures of everything I do. It was fun writing an article about this repair.
Right now I am building a jig on a small BB to experiment with a SOP-8 Synchronous Step-Down DC/DC Converter #FR9882 that I salvaged from a Router that quit working. I need a through-hole 10uH inductor that I don't have. So I'm turning a SMD Inductor into a through-hole for my BB.
I probably won't mess with it today since my yellow USB 3.0 Power Monitors that I bought from Frankie on his Ebay store 99centHobbies will be here in the mail today.
marco tapia
February 4, 2015 at 7:45 pm
Hi Robert, thanks to you and Mr. Yong for your articles in repair as it helps keep me up to date with certain problems in this field, love the details of your pictures as you take us on this repair adventure, love it, love it, thanks so so much for taking the time to post your article for us. 🙂
Robert Calk
February 5, 2015 at 10:06 am
Hi Marco,
You are very welcome. It was my pleasure to write the article - I enjoy doing it.
Paris Azis
February 4, 2015 at 11:39 pm
Dear Robert
This was a nice presentation indeed.
Starting from the qualitative parameter of the subject, I agree that this product is of low quality, although I disagree with opposite opinions expressed in this forum just for one simple reason alone, which I will try to explain.
This idea can best be expressed by a proverb used in my country, saying that “the bad (: quality) meat is for feeding the dogs” (: instead of humans). And just like it happens in real life we need to feed both “humans and dogs”, we equally need both cheap and expensive test instruments for quite different uses. Cheap products can be tested or powered with cheap instruments and vice versa. An example would be the need for a controlled PSU just for car battery charging. For this purpose one can use the type you repaired. But whenever the powered equipment is critical in both voltage accuracy and stability or output protection, then, of course, the use of equipment of higher quality specifications is essential.
A lateral but practically overall side of my view on this topic is that we need inferiority in order to appreciate superiority. For me personally, this is a life axiom. The process I have in mind is like the one the voltage comparators use in their function. They always need a stable (: unquestionably reliable) voltage reference in order to evaluate the voltage they control using their feedback (: subject to change) sample voltage. So, if the reference has variable character or even worse is lost, control is inevitably erratic or completely lost.
Now, I didn’t quite understand why this PSU was not “giving” much power output, and I am saying this because judging from the photos you posted you worked on the display unit and this circuit is apparently not responsible for a fault like this one.
As I saw in the posted pictures, the problem should lie in the main board. I can distinguish there the auxiliary power supply with the three pinned regulators feeding the two op amps (8 pin chips). The current regulator normally is the one of them, “seeing” the voltage drop on the high wattage-low ohms (white ceramic) wire resistor as current flow through it, used as feedback against a stable reference. That is, here somewhere you should normally have seen the trouble and not in the display unit. This is my point. But of course I don’t know how the circuit is being developed in the pcbs and I absolutely agree with the idea of the poor soldering of the components on the pcbs and the bad quality of the components’ joints due to the unleaded modern solder being used nowadays…In some cases I have seen, this looks like real disaster…They needed a total soldering rework, demanding complete removal of the original solder, translated in pointless spending of many working hours.
INTERESTED FOR SOME UPGRADING?
By the way, if the op amps are of the 741 type, one for voltage and one for current regulation as it usually happens in float type PSUs like yours as I think, I suggest you to replace them both with TL081, which is a direct replacement of 741 and it is much faster in response to changes in their inputs than the 741 ones. For the late type, the slew rate is only 0,5V/μsec, while for the TL081 is 16V/μsec. As you can easily understand, the practical benefit of these replacements in terms of speed of regulation and reliability will be huge, especially as regards short circuiting the output which is a normal demand for presetting the (non calibrated) current output of the PSU before even working with it! It will save you the series regulating transistor from a very likely death cause, which is the sudden short of the output!
Furthermore, if I may express my suggestions for upgrading the quality of this PSU considering that I am not paid from the manufacturer as I probably should (!!!), I would suggest you to add two more 2SD1047 transistors connected in parallel with the existing one (C to C, B to B, E
to E, using three 0.56Ω / 3W or (better) 5W current sharing resistors connected one-to-one to every emitter, while shorting together their three free ends which will consist the common emitter of the circuit thereafter) even on the same piece of the existing aluminum heatsink, although it is not adequate for the cooling purpose, which is mostly covered by the blower.
I propose this upgrade in order for you to secure better working conditions for the single regulating transistor. Consider that this transistor has to dissipate at least 150 Watts of power in case of short circuit for giving out 30V and 5A (30*5=150), and the calculation does not take into account the real rectified voltage across the main filter capacitor, but only the regulated DC output of it rendering it lower in wattage. That’s why I say “at least” above. My thinking is especially valid if there is no tap change provision for the transformer secondary feeding the rectifier bridge keeping thus the dump power in low levels.
As for the transistor parameters themselves, the 2SD1047 has these maximum absolute ratings: 140V, 12A, 100W. Keep in mind that this nominal power indication is a) far beyond the power handling this transistor normally has to withstand in this application of your PSU and b) is directly connected to the transistor’s crystal maximum working temperature which should always be kept below 150oC. All above according to the data sheet. That is, you cannot rely on this aluminum piece used as heatsink without the inevitable use of the external blower, which in turn means that your PSU is absolutely dependent on this blower even for relatively low loads in its output, with the original circuit design.
In other words, if the blower fails, this transistor “will meet its ancestors” in a very short time space due to excessive temperature rise in it!! At least, by doing this modification, you lower the transistor’s electrical stress to 1/3 of the original value, extending thus your own reaction time to save the PSU in case the fan stops while feeding a reasonable load!!...
I really wonder if there is, due to its importance, a load depended fan speed controller or the fan is being left to run at full speed all the time, as usually, which means that the PSU has already given a death date right from its birth one!! I didn’t see anything relevant in the posted pictures anyway and you are kindly requested to inform me about that, just to satisfy my curiosity…
I have seen this type of thermal failure many times in the past, especially in cheap computer PSUs and also in commercial SMPSs, and the process is always the same; a) blocked fan b) high temperature rise throughout the entire circuitry c) almost all electrolytics bulged or even desoldered from pcb or exploded, no matter if they were in the primary or the secondary circuit d) a lot of power semiconductors blown up, especially those in the primary side, such as the power factor cqt, the main rectifier diodes and primary power transistors…and the story goes on…
Best Regards
Paris Azis
Senior Electronics’ Technician
Athens Greece
Robert Calk
February 5, 2015 at 11:55 am
Hi Paris,
I'm just a hobbyist, but from now on I'll save my money till I can
buy better quality stuff. I got it mainly to test IC's & devices and power my BB projects that don't require precision. I must admit that the unit is more accurate than I thought it would be; within 1mV's and 1mA's. But the control board is the only PCB I had a schematic for. I was more less shooting blind and it's my first time working on one. But I got it done.
Thanks for the tip about the Op-amp. I didn't check on better replacements - I was just trying to get it fixed then. I have all of the datasheets.
Yes, the fan runs constant. The good thing is that I can hear it, so if it quits I'll hurry and shut the unit down. The transistor was $3.92 a piece, so I bought 2 of them a while back from Mouser.
I was also thinking of drilling some small holes in the "heatsink" to help cool it better by getting some air going through it instead of just going around it.
Anyway, thanks for the comment and tips!
Paris Azis
February 6, 2015 at 1:38 am
Hi Robert
I noticed that you state you are a hobbyist and that’s why I entered in upgrading details about your PSU.
Nevertheless, although being yourself a hobbyist, your repairing presentations have professional appearance indeed. If I also take into account the “blind shooting” of such cases, this adds more value to your work. As I see you are also very well equipped and that is a vibrant sign of a hobbyist!
Well, it was no surprise to me that the fan runs at full speed constantly…I wouldn’t expect anything better from a cheap design like this one and I thank you for satisfying my curiosity! Hopefully the annoying noise it produces will assist you in supervising it!
My last advice to you (if I am allowed) is; do not drill holes in the already poor heatsink. Instead, add on it as much aluminum mass as you can, attaching for example a (massive) aluminum cube of proper dimensions, the bigger the better, or (much better) use another (massive) heatsink having vertical fins. This type is much more effective.
A question is if the fan extracts hot air from inside the box or if it inserts cool ambient air into it. I think that in your case (inadequate heatsink) the best would be to blow ambient air directly onto the case of the power transistor. Finally, I hope there is an adequate number of holes in the external case for proper “breathing”…Good luck anyway!
Best Regards
Robert Calk
February 6, 2015 at 10:24 am
Hi Paris,
Thanks for the compliment. I appreciate the advice also.
The fan pulls air through vents on both sides and out through the back. It does pull quite a bit of air. The fan isn't too loud at all. I actually expected it to be louder than it is. It looks like a regular desktop computer fan.
I'll keep my eyes open for a good heatsink that will fit in it.
Robert Calk
February 6, 2015 at 2:46 am
Hi Paris,
After thinking about it, you may be right. I have a habit of while my de-soldering gun & iron are hot, I will re-solder everything that catches my eye. I didn't think about it at the time, but while I was soldering up the display board, I did re-solder some connections on the mainboard, starting with the jumper on the -15V regulator because I really didn't like the looks of it. They could have actually been the fix and I didn't even realize it.
Thanks for bringing that to my attention. If I ever receive some high-end equipment that arrives DOA, I'll document the repair much more carefully.
Paris Azis
February 6, 2015 at 5:16 pm
Hi Robert
It seems we have already a common habit! It is not bad at all if you can bring back to life a dead electronic device by simply resoldering bad joints. So the habit is effective.
On the contrary, it is a very bitter feeling indeed and meaningless to troubleshoot for many hours just to find a cold joint…! So, what counts is that you fixed it and you did this with no troubleshooting headache, that is, most effectively.
Keep in mind that if you do these modifications, this tiny box will serve you reliably for many years.
Here is another one for the fan. There are in the market cheap bimetallic thermostats for 45oC with their lead contact normally open until they sense this temperature. At this point they close contact, energizing the fan. They are specially designed for this purpose and also they can very easily be fitted on the heatsink. If you install it, you will extend the life of the fan for very long time.
And if you add transistors reducing their resulting thermal stress your cheap PSU will no longer be cheap and what’s more, it will be bulletproof!
As you see, I am targeting on a hobbyist’s feelings!
Robert Calk
February 6, 2015 at 8:58 pm
Hi Paris,
I'm glad I'm not the only one. I guess it's because I have the Hakko 808 and it's so easy now to redo solder joints that I'm quick to re-solder stuff without paying much attention.
When I make any modifications, I'll write an article about it.
Thanks.
Robert Calk
February 16, 2015 at 7:54 am
Hi Paris,
I've decided to do the transistor & op-amps upgrades on my power supply. I checked on-line and they say that any 5 watt resistors below 1 Ohm will do for the emitters. I have some axial 5W 0.51 Ohm resistors that I will use.
I don't want to spend much more money on the unit than I need to, so I'm going to leave the heatsink in and see what kind of life I get out of the fan. It would probably be cheaper to just replace the fan if it will last a year or two running constant.
But I will add to the heatsink's mass when I find some good aluminum to add to it. But for now I'll just upgrade the power transistors & op-amps. Thanks for the help.
Robert
Gevas Enguneering
February 5, 2015 at 5:13 am
Nice Work.!!
Robert Calk
February 5, 2015 at 11:57 am
Thanks Gevas.
ben
February 5, 2015 at 7:21 am
Great article Robert, I enjoyed reading your repair journey and I can totally relate to those lifted tracks some pcb's seem to do that no matter how much flux and 60/40 I use before I take too them with the de-solder gun...great read mate...
Robert Calk
February 5, 2015 at 12:00 pm
Thanks Ben. At least there was plenty of room for jumpers.
peter
February 5, 2015 at 8:08 am
Great job, good skills & amazing persistence.
Such a pity That products such as this are still found, built with little care & zero effective quality control.
There is absolutely no excuse for most of the defects you found.
Had I paid for this I would have used PayPal & their resolution process would have eliminated any return cost claim on you - worth mentioning maybe?
Regarding lead free solder - it seems to me that for small scale manufacturers it is a completely inappropriate process & is almost guaranteed to result in many faults some of which will only show as time passes.
I failed to notice the brand but certainly if I knew it I would blacklist the organisation.
Thanks for the detailed repair article.
Robert Calk
February 5, 2015 at 12:09 pm
Thanks Peter. Yeah, soldering is everything! You can't have good connections if you have poor solder & soldering.
But it is good for repair shops.
aword stephens
February 5, 2015 at 5:10 pm
Thanks Mr Robert your article is very good.
Robert Calk
February 5, 2015 at 10:45 pm
You are very welcome Aword.
Lee
February 5, 2015 at 9:59 pm
Hi Robert - Well Done!
I can clearly see you like this hobby!
And yes, Jestine is a master and has helped me too couple of repairs.
It is always a good thing to thoroughly check PCB’s visually from all angles prior to any rework.
I can see you have a Blue ESR Meter and atlas DCA75 - how do you rate these?
Which digital microscope cam do you use?
How do you check the Main Power Transistor?
What is the purpose of the 5K trimmer and how you adjust it properly?
Thanks!
Robert Calk
February 6, 2015 at 11:58 am
Hi Lee,
Thanks. Learning electronics is a lot of fun. I wish I would have got into it when I was young.
I love the meters! With the Peak Atlas DCA 75 Pro, all I have to do is connect the 3 leads to the transistor pins, then push a button. It is an excellent meter. It will identify components that are new and not even in the books or internet yet.
I have a little handheld microscope camera that cost less than $100. I think I bought it from Radio Shack online. It is a Celestron #44310. It takes pretty good pictures if your hands are steady enough. I take a few pictures of each shot, then when I transfer them to my laptop I pick out the best picture.
That 5K trimmer goes to the Amps Pots. The schematic of the control board that they gave me shows what the trimmers adjustments control. I just adjusted and played with them after zeroing the mA's until I got the unit working good while checking with my Fluke 87V. It is within 1mV & 1 mA now.
Ahmad
February 7, 2015 at 5:21 pm
Man u really have lots of patience..
We all never give up on repairing electronics.. no matter how many attempts it takes but we still do it..
Very well explained article..
thanx for your effort to share it with us..
Mr. Jesting
many a thanks to you for giving us this platform..
Robert Calk
February 7, 2015 at 11:20 pm
You are welcome Ahmad.
Abdul Haleem
February 7, 2015 at 11:43 pm
Congrats for the successful end of your arduous journey of repairing the PS. Could you pls tell me what kind of microscope camera that you have, price and where to buy it.
I too have admiration of the MAN Jestine Yong how he finds and manages time to graze all his emails and ANSWER them. When people buy an ebook from him some of them think that he has an obligation to answer their questions and throw few simple questions into his email box but he ANSWERS the question patiently, I have observed. Anyways thanks to you Robert and Jestine as well.
Robert Calk
February 9, 2015 at 12:13 am
Thanks Abdul. It's a Celestron #44310. I can't find the receipt. I either bought it from Radio Shack or frys.com. I think it was around $80 - $90.
humberto duarte
February 10, 2015 at 1:08 am
lot of work but great job I love it thanks for sharing it
Robert Calk
February 11, 2015 at 2:08 am
You are very welcome Humberto.
Shaddrach K Tarutia
February 10, 2015 at 6:46 am
Thankyou for new ideas
Robert Calk
February 11, 2015 at 2:09 am
You are welcome Shaddrach.
Daud
February 19, 2015 at 6:23 pm
good efforts.
Robert Calk
February 20, 2015 at 9:57 pm
Thanks Daud.
Raju varghese
May 25, 2015 at 2:50 am
Hi Robert,
This is an Excellent work & good efforts please keep do sharing.
fuba
August 12, 2015 at 1:26 am
great job!
but i think you spent more than 20$ for repairing!
Jimmy
May 9, 2016 at 9:32 pm
Hi Robert. Its been long enough now. Do all us hobbyists a favour and leak that schematic that you promised to keep to yourself. There is nothing around and it will be greatly appreciated by many. No doubt you have perused countless schematics on the net..where do you think they came from? They were leaked by people just like yourself in similar circumstances. Its your turn now Robert. Thanking you on behalf of hobbyists world wide.
Robert Calk
May 11, 2016 at 1:00 am
Sorry Jimmy, but I gave my word. I'm not perfect by a long shot, but I do try my best to keep my word. Besides, these older style PCB's are not too difficult to study compared to multi-layered PCB's.
Mick
August 23, 2017 at 7:25 pm
Hi Robert, it is now August 2017 and I just ordered one of these power supplies. Hopefully the quality has improved by now. If not, I will use your article as reference to make repairs / improvement. Many Thanks.
elec lam
November 20, 2017 at 12:43 am
i have 1 GQ-A305D power supply, when i put 4 variable back to position 0, but the clock still shows 6v, can you tell me how to fix it?