IGBT Shorted In Tecnica 164 Welding Machine
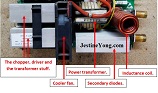
A few days ago, I got a Tecnica 164 welding machine for service. The customer told me the machine die after several hours of using it. It simply shut off and now won’t turn on even if the power button is switched on.
I have never repaired a welding machine and never used one before but I decided to open it and see what kind of parts found in this machine. The Tecnica 164 is one of the currently most use inverter welding machines.
Here are the photos of the opening procedure, I will try not to go to deep discussion because the repairing is easy and I think it would not be necessary to explain too much:
Now you can separate the PCB from the housing by pulling out the complete PCB. Be careful because there are two large capacitors. I didn’t found any solution how to discharge these two capacitors before the PCB separating process. If you touch caps you can get an electric shock! So, have patience and take care of your safety.
My first thought is to make a visual check on the parts and the pcb. Maybe there is some sort of evidence what could result in a shorter repair time or to decide does the stuff is repairable or not. Before I started with component checking I made for me some sort of blocks. Just to clear what sections are for what purpose. So I can arrange and compare the given failure what I got from the customer with the region/ block and search on that block the problem.
If no power then I should first check the power section or in this case the AC input block. No welding then I should check in the “welding process” and in the setup block but not in the AC input. Of course this is not a “must do” protocol but it helps me to see the whole thing from another angle.
First I discharged the caps. The discharging process already been discussed several times in this blog, so I won’t go into that explanation. I’m interested on that white big body 10W/R47 resistor, the relay next to that resistor and that heat sink. Under that heat sink is a rectifier bridge.
Let me describe this circuit a bit:
There is the R4 which is the big white resistor which is 10W/R47 in my case, but on the schematic is 8W. There is the RL1 which is the relay and the PD1 is the rectifier bridge. Just take a look at the resistors C22, C21 and C27 which are on the right side of the diagram.
So, the RL1 is almost de-energized when the power switch is pressed and no current will flow through the contact of the relays. The R4 will limit the current which is entering into the PD1 rectifier bridge, together this two parts charges the capacitors C21, C22 and C27. When the capacitors are charged then the relay is energized and the R4 is shorted by the relay RL1.
With this method the manufacturer prevents the formation of high transitory currents that could damage the main power switch, the rectifier bridge and the capacitors. I found the R4 was broken and through them could not flow any current and so the capacitors could not be charged and the RL1 would not energized. This fault was the “no power” failure.
The next step what I was interested was the “welding process” block. This is the second block where stuff can go wrong when the welder is overloaded or used for a long time of period without of cooling down. A shorted circuit in that block could make big problems because of the current which flows through that block which is needed because of the welding work.
Let’s check the “welding process” block:
Under the chopper, driver heat sinks there are two G30N60A4 IGBT transistors.
This part converts the continuous voltage from the filter into a high frequency square wave, capable of piloting the power transformer and regulates the power according to the required welding current/voltage. I checked these IGBT’s and all of them were shorted.
After I changed the IGBT’s I checked almost all the parts for eventually shorten regions, parts but wasn’t found any damaged elements.
I have to say about the “Setup” block, that block is for setup the unit working parameters. If that block fail then the unit would not work correctly but I assume it would still power on. So I did not pay any attention to that region until checking, just visual and check on few components.
After the repair work was done, I powered the unit on and wait for few minute to see if something goes wrong, but the machinery was working as it should. I called a friend of mine and asked him to test the machine several days in his workshop where he works with heavy metal welding stuff.
The welder was repaired and given back to the happy customer who had a nice smile on his face.
I hope you enjoy this tutorial and will save lot of your repair time.
This article was prepared for you by Christian Robert Adzic from Novi Knezevac-Serbia.
Please give a support by clicking on the social buttons below. Your feedback on the post is welcome. Please leave it in the comments.
P.S- If you enjoyed reading this, click here to subscribe to my blog (free subscription). That way, you’ll never miss a post. You can also forward this website link to your friends and colleagues-thanks!
Note: You can check his previous post in the below link:
https://www.jestineyong.com/what-no-one-tells-you-about-data-recovery-from-broken-eeprom-ic/


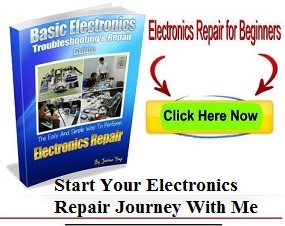
albert van bemmelen
March 22, 2016 at 2:56 pm
Thanks Christian. It is always a bit harder to disassemble these compact made units to be able to find the defect and repair the device. But afterwards you have made another Customer very happy!
Parasuraman S
March 22, 2016 at 7:04 pm
Another unique electronic tool repairing! Variety is what we get in Jestine Yong's blog! Many thanks for your descriptive article as well as the methods and explanation of the principles of working! You are very concerned about how we all understand on service, and include such details that are essential! Great dedication! All the best!
Kevin Gardner
March 22, 2016 at 7:26 pm
Christian, That is a great repair. I own a welding machine repair shop here in the USA and most of the time machines like those are scrapped for the smallest of internal failures because it is often cheaper to buy a new one than to fix the broken one. I have a pile of small welders similar to the one you repaired that I would like to think that someday I will be educated or experienced enough to repair and put back into service. But, I highly doubt that I will ever be that smart. To all of you truly smart guys and gals in the world please keep up the great work of saving electronics of all kinds.
CORRIETE CYRILLE
March 22, 2016 at 8:05 pm
great job done thanks to you for providing such a successful fix
Robert Calk
March 22, 2016 at 10:04 pm
Nice job, Christian. Thanks for the article.
Humberto
March 22, 2016 at 10:49 pm
Hi Chris, you have done a nice repair with good explanations and excellent images.
Gregory M Brettell
March 23, 2016 at 5:43 am
Thanks for the post and sharing your experience!
Gary Gemmell
March 23, 2016 at 5:59 am
Always the most interesting articles on Jestine Yong, Christian keep up the good work. Serbia is great country that helped us win the war i am jealous!
Gerald
March 23, 2016 at 8:39 am
Well done Christian. I love to see articles on different kinds of equipment and yes, sometimes disassembling is more intimidating than the repair itself. Thanks for sharing.
Cheers,
Gerald
Hicham
March 24, 2016 at 10:27 pm
Hi Christian,
Really i can say it's a great job you done, i am a welding machines technician Enginneer, almost after oscillator stage there is those igbts who get shorted, but sometimes there is surprises like exploding...
Thanks Christian for your interesting article and only i can say keep up the work.
suranga bandara, Suranga Electronics
March 25, 2016 at 7:29 pm
hi. Mr- Christian,
You done a very good and clever repair.
Thanks for your Article.
Henrique J. G. Ulbrich
March 27, 2016 at 9:20 pm
Very good, Christian. I am curious to see the welding process block. Don't you have the schematics of this interesting part?
Chris
April 28, 2016 at 6:12 am
Ulbrich:
Thanks for your comment, I have the whole schematics of this machine and you can download it from this link:
https://drive.google.com/open?id=0BzCmxPSYmVj2SE1tTWxPTXpmM1E
My best regards.
pasumarthi rameshbabu
July 7, 2016 at 12:46 am
dear sir,
I request you, i want mma/tig 250amp, inverter welding machine strip control connetion circuit,testing points.