New Wasmachine and Tumble Dryer Repair
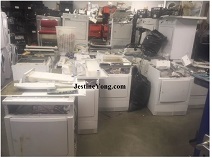
These days a single bad component can stop a complete machine from working. It can be a simple lambda probe in your car that needs fixing before the motor starts again. Or even 5 to 6 different hardware built-in safety protection procedures in a modern Beamer why a Projector won’t power up.
This repair is about at least 20 identical used AEG t55640 2500 Watt tumble dryers (and also washing machines) that I fixed in these last weeks that all suddenly stopped working.
There is a controller board in these machines that powers down when a LNK304 chip breaks down. And together with that LNK304 chip a single 47 ohm burns through on the controller boards. After both are replaced the machine will work again just fine.
These special LNK 302/304-306 chips can be found in all sorts of non-isolated power supplies like in rice cookers, dishwashers, and other white goods. What makes this repair interesting is that these LNK304 chips are excellent PWM modulated Buck controllers capable to withstand a HV 700 input
voltage. And only the LNK304 to 306 type off-line switcher controller has a built-in Auto-Restart function.
Next example circuit shows the way how the AC Line voltage is directly connected to the LNK304 chip. Only the shown resistor RF1 that also functions as a safety fuse resistor isn’t a 8.2 ohm 2Watt in our AEG tumbledryer repair but the already mentioned 47 ohm 2Watt component.
The non-isolated input circuit components are the fusible resistor RF1, D3 and D4, C4 and C5, and coil L2. (See Red circle).
The active power processing stage circuit components are the LNK304, D1, L1 and output capacitor C2.
C3, R1 and R2 are the Feedback components and are selected in such a way that the voltage at pin FB is a stable 1.65V at the chosen output voltage.
The D pin is the Drain Mosfet connection that provides internal operating current to both start-up and steady-state operation. The BP is the Bypass Mosfet connection for the internally generated 5.8V supply.
The normal LNK304 operation will terminate when the current that goes into the Feedback FB pin is greater than 49 uA. The internal LNK (LinkSwitch-TN) chip runs of the energy stored in the bypass capacitor thanks to the extremely low energy consumption needed. A capacitor of 0.1 uF (C1) is sufficient for providing enough energy for the chip to operate.
The circuit also provides undervoltage protection when the BP voltage drops below 4.85V. This will disable the Power Mosfet in our LNK chip until it rises back to 5.8V. (because only when the Mosfet is on , the LNK304 runs of the energy from the bypass capacitor). And the LNK is also over-temperature protected by a treshold set at 142 degrees Celsius which will disable the Power Mosfet. And there is an internal over-current protection too that also will disable the Power Mosfet. Resistor R4 is a small pre-load that prevents tracking errors between the output voltage across C3, at light load or no-load conditions. The forward voltage drop over both special UltraFast diode D1 and normal silicium diode D3 are identical. So the voltage developed over C3 tracks the output voltage. And resistors R1 and R3 are chosen so that at the desired voltage output, the feedback voltage at the FB pin exactly is 1.65V.
Regulation (at about 66 kHz) is maintained by skipping Mosfet switching cycles. When the output voltage rises, the current through pin FB will rise too, which will disable the Power Mosfet. This means that when less amperage is drawn at the output the output voltage will rise which will inhibit switching the Power Mosfet as in the previous regulation method described.
And in case no cycles are skipped during a 50 ms period (only the LNK304-306 types) the average output power will be limited to provide overload protection by entering an internal auto-restart mode. Next photos show the position of the LNK304 on the AEG controller board.
And following photo shows the mentioned fusible 47 ohm 3W resistor (R76) that is placed at the component side. Here a 3W type, but sometimes they are probably also just 1 or 2W. And if a 8.2 ohm 2W type in our example circuit is okay, a 47 ohm 1W certainly will do just fine too. Besides, if we choose a too high Wattage it won’t work as a fusible protective resistor anyway!
Next circuits, extracted from the Power Integrations Datasheet, show how we also can use this switcher IC to make a simple non-isolated AC Line operated protected LED Light.
As it seems, this LinkSwitch IC is becoming almost as popular as the old and still used 555 IC.
Above the internal circuit of the Off-Line Switcher LNK304-306 IC. Next photo shows where the frontpanel with here still the controller board in it was extracted.
It is still not entirely clear what makes all these identical machines suddenly fail. But according to my good shopowner friend Anton this likely occures when customers do not clean out the dust in their dryer machines on time. Which makes the tumble motor running harder, causing it to use more current, and often also destroys the motor capacitor at the same time. Anyhow after all my recent repairs it looks like these problems are real designer flaws. Maybe made on purpose to sell new machines? And it looks like something that is only happening in our modern day world. Something that would have been bad advertising for a manufacturer in the old days.
Following photo shows the entire component side of the controller board of the AEG tumble dryer. With the green colored 47 ohm 3W resistor on the top right, just above the blue AC switch. The LNK304 Off-line switcher IC is at the solder side about under the blue AC switch.
Previous photo shows the tracks after removing the old bad LNK304 chip.
Looking at the bright side, it could mean more jobs for repair engineers. Nevertheless I was only helping a good friend on a pro deo base. Hoping to make the world a little better!
By-the-way: If you wonder how you can tell if a LNK304 chip is defect? That one is most likely shorted between pins Source and Drain! But in most cases your RF1 resistor needs replacing too.
Albert van Bemmelen, Weert, The Netherlands.
Please give a support by clicking on the social buttons below. Your feedback on the post is welcome. Please leave it in the comments.
P.S- If you enjoyed reading this, click here to subscribe to my blog (free subscription). That way, you’ll never miss a post. You can also forward this website link to your friends and colleagues-thanks!
Note: You can read his previous repair article in the below link:
https://jestineyong.com/solving-a-chevrolet-spark-m300-blowing-fuse-problem/


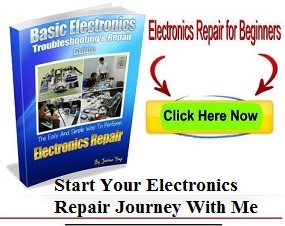
Suranga Electronics
November 27, 2017 at 9:46 pm
Hi Mr.Albert ,
Wow .. very nice Repair Services and More Details.
Thanks!
Albert van Bemmelen
November 28, 2017 at 7:37 pm
Thank you Mr.Suranga. After I already had fixed a lot of these tumble dryers I decided it was time to write an article about these machines. A copy of the AEG service manual would have been very helpful to find out how the output of the LNK chip is connected to the rest of the AEG controller circuit. But that was sadly missing. In hoping to find a reason for their failures examining the datasheet of the LNK304 (and 305 in other machines) was the only option. After the machines are defect the internal LNK mosfet is always conducting (in an on-state of about 35 ohms between Source and Drain) which would suggest a shorting output wich causes the input fusible resistor to burn through at the same time. Which in this case hardly is Fail-safe. (because only an output seriediode would make a fail-safe LED Light possible that would prevent a fusible resistor to burn open). Still any LNK output shorting problem is gone after the chip is replaced by a new LNK304 and new fusible 47 ohm resistor.
Geoffrey
November 27, 2017 at 11:17 pm
Very detailed and thorough explanation and following course of action to bring things right. Thanks
Albert van Bemmelen
November 28, 2017 at 7:46 pm
Thank you Geoffrey. Finding answers why identical machines quit working always lead to examining datasheets in absence of a good AEG machine service manual. Luckily the repair doesn't cost much because about 50 of these LNK304 SMD IC controllers cost just about 12 dollar. And 47 ohm 1 Watt resistors are cheap too!
Yogesh Panchal
November 27, 2017 at 11:49 pm
Albert,
Thanks for detailed explanation!
Albert in past have you replaced low Value Resister in-place of Ceramic or glass fuse? because i am not getting precise fuse of value say if i am having 3.15amp ceramic fuse in the circuit then what would be the nearby replacement law ohm resistor.
Albert
November 28, 2017 at 4:18 pm
Good question Yogesh, but I don't think I ever replaced a ceramic fuse by a ohmic resistor. Not even if it is a fusible one like in this tumble dryer repair. And in case you can't find a special fusible resistor we just use ordinary resistors that will burn through when the current reaches its calculated final level and the resistor its protective end of life state (if you use the right wattage type of course!). Ceramic fuses hardly have any ohmic value so you can't use them instead of a fusible resistor either (the silver or copper just melts/evaporates at the calculated current). Besides the fact that a fusible resistor also limits the in-rush current which a ceramic fuse will not.
Praveen Rajan
November 28, 2017 at 3:56 am
Wow, i would like to read more about service and repair of washing machine, dryers and etc...
Thanks.
Rajan
Albert van Bemmelen
November 28, 2017 at 6:30 pm
I certainly will keep you up to date with a new article if I have one Rajan! Repairing white good appliances is not something that I normally do very often. Also because these devices are too big to carry around and they simply take up too much space in my service room/electronics shack.
Robert Calk
November 28, 2017 at 4:01 am
Good job, Albert. Do you mean helping "pro bono"? We have a problem here also about some of them not cleaning the lint trap in the clothes dryer. Most people that don't have to work for anything, don't care about anything.
Albert
November 28, 2017 at 3:58 pm
I just helped my friend out on a friendly voluntary base Robert. Soldering those parts only took me about 5 minutes per machine so was no big deal for me, were it was a big help for him. I didn't even have to open or close the dryers which was done by his brother. And I used their soldering station equipment, so didn't have to carry that with me from home either.
About cleaning those dryers (with max 7 KG clothing in these AEG machines): Once the girlfriend of my colleague phoned from their home that her tumble dryer had caught fire probably because she had not cleaned it in a long time. And I just read about the fact that dryers cause almost a fire a day! Even about faulty tumble dryers that caused huge tower block fires! So I hope that this also will warn all tumble dryer owners to be alert and at home when the machine is active.
Anthony
November 28, 2017 at 8:22 am
Great repair story again Mr Albert Einstein ! I think you're correct
in that manufacturers design appliances that have flaws and weaknesses
seemingly on purpose so as to generate more sales perhaps?? Most electronic appliances these days seem to have only a one year warranty....Hmmmm...let that be a guide to the quality of the item
you're thinking of purchasing !
Kind Regards
Albert van Bemmelen
November 28, 2017 at 4:58 pm
In the EU most electronic appliances have a 2 year warranty Anthony. Why I wouldn't buy anything with less warranty time. But if you live outside Europe in another country they probably share other rules. Sadly still a lot of these devices fail right after that period. The best way to know if something is worth the money is to wait until it is on the market a little longer. Normally I therefore never buy anything when it is brand new. And in the meantime prices likely will conciderly drop which is even better!
Humberto
November 28, 2017 at 12:59 pm
Hi Albert, a good job and great explanations, as usual.
Albert van Bemmelen
November 28, 2017 at 6:34 pm
Thanks Humberto!
James
November 28, 2017 at 2:30 pm
Excellent Info yo', many hoorahs''
Albert van Bemmelen
November 28, 2017 at 6:43 pm
Thank you James! I always wonder how you are able to add that smiley character.
(And also how others manage to add their small photo into their personal avatar icon). I guess you must be a HTML5 website wizard?
Parasuraman S
November 28, 2017 at 8:54 pm
Excellent, excellent and excellent to the power of infinity. One of the best articles I read in this forum. Very informative, thorough and useful. The question is why is the component fail in the shop itself? What design problem the company has overlooked? Hat's off to your in-depth knowledge on circuits!
Albert van Bemmelen
November 29, 2017 at 2:32 am
Thank you for your very nice comment Parasuraman! One answer could be that the LNK304 (or 305) chips are not within spec? The problem with these big machines is that before we can test these we first have to completely assemble and close the machine before this is possible. So checking on voltages, temperatures or other values internally is hard to do. The length of all wiring cables is just made so that connectors only fit when the machine is completely closed. In AEG or other repair centers they probably have larger test cables and separate modules to test every part of these machines. My shopowner friend told me that sometimes machines get destroyed because customers switch on the machine without letting it cool down first, or they immediately switch it on again after they just had switched it off. That certainly would explain the in-rush current through the fusible resistor. Time will tell.
Parasuraman S
November 30, 2017 at 4:43 pm
One of my technician friends does regular servicing washing machine boards, A/C control boards etc. He has set up a dummy washing machine load for checking the board keeping it on table. I have seen him doing it with such an ease, it is an awesome sight to watch. He shorts the door lid switch, and gives some bulb load etc. which I am not able to explain thoroughly. In face I give my washing machine boards to him and get it serviced. He has all the tools and other things required to open the thick film of non-conductive and noncorrosive paste and reapply after finishing the work. He is such an expert that he makes holes on the top only for removing the defective component!
Albert van Bemmelen
November 30, 2017 at 8:27 pm
I understand that your friend obviously fixes these machines on a daily base Parasuraman. He likely must be dealing with one kind of brand when no board from other manufacturers will fit, if he uses only one prepared dummy machine. Until now I never needed to open any thick film or non-conductive or noncorrosive paste. The replaced components didn't have any paste. And removing defect components in the AEG machines by desoldering them is very easy. Drilling holes would probably only mean more work and could damage the (often varnished) controllerboard. Cheers!
Justice
November 28, 2017 at 9:13 pm
What a sophisticated and complex article it has been, but most importantly interesting. I will have to read over and over again, Thank Albert.
Albert van Bemmelen
November 29, 2017 at 3:02 am
Thank you Justice. Explaining the LNK304 controller chip indeed is rather complex. The datasheet exists out of 20 pages which I had to compress into this short repair article. (http://pdf1.alldatasheet.com/datasheet-pdf/view/273804/FERYSTER/LNK304-306.html). That is why I also try to simulate parts of the internal circuitry of the LNK in Tina Design Suite. I started with simulating the 3 mosfets at the FB pin. Strange enough my results in Tina do not match the mentioned 1.65V voltage. And if I use 3 depletion mosfets the logic results are almost identical to the results when 3 enhanced mosfets are used. Only the needed FB pin input voltage at the mosfet source to activate and switch the logic levels is much higher when enhanced mosfets are used. Which is strange when the LNK chip internally uses P and N-channel enhanced mosfets.
Albert van Bemmelen
November 30, 2017 at 7:04 am
PS: Tina designer Suite has many interesting options like the Analysis menu options : Transient and/or AC or DC analysis. Which draws automatically the excitations of any Circuit designed (drawn or made by input with the Tina Interpreter). In a wavediagram all voltages present over a preset time can be watch and saved. With this menu function it was easily possible to see that my first circuit with 3 depletion mosfets worked like the second circuit with only 3 enhanced mosfets did (enhanced like in the LNK internal circuit on the FB pin). And that they were each others exact opposites concerning their voltage levels. Were the Depletion mosfets voltage wave levels were descending the Enhanced mosfet voltage levels were rising and vice versa. Without this great function it would be very difficult to grasp the function of a designed circuit. And although Tina has many components in its database, the LNK 304/305 chip is not available (yet?), why I am trying to simulate it in Tina.
Albert Hoekman, Tiel NL
December 1, 2017 at 7:33 pm
Hi Albert, good job.
This is something else than sitting at your repairtable soldering at a LED bulb. ;-))
You are doing a great job on all different kinds of stuff for the home market! Keep on going!
Best regards, Albert.
Albert van Bemmelen
December 1, 2017 at 9:58 pm
Thanks Albert. You are right! Repairing machines that need 2500 Watt of power or more is indeed something different.
Carlito Lauron
December 9, 2017 at 6:41 pm
Hi,
A nice and interesting article to read, the detailed explanation are very informative and usefull,
Hope you will post more like this.
Best regards,
Carlito
Albert van Bemmelen
December 10, 2017 at 2:37 am
Thank you Carlito for your nice comment. I do hope that new interesting repairs will cross my path again soon.
Gary
April 15, 2018 at 4:01 am
So the net result is dont buy an AEG t55640 2500 Watt tumble dryer.
>;o)
Albert van Bemmelen
January 12, 2025 at 9:51 pm
My shop owner friend only had a few types of machines in stock. Probably all other manufacturers also use the same type of low standby LNK or similar chip in the primary circuit to save on electrical energy when they are switched off. And only a few have used modern solid state relays instead of the old cheaper electromagnetic relays.