Dyson DC08 Vacuum Cleaner Repair (With Video)
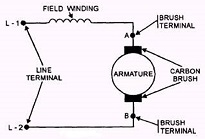
As with all things, parts eventually wear out and need replacement.
This Dyson vacuum cleaner has been part of our household since about 2002, when this model was first introduced. But, during use, it started to smell and finally stopped.
After disassembling the plastic housing, which included the wheels, filter assembly & cyclonic housing, the switch and motor were now exposed for testing.
Although I was sure that the switch had not created the fatal smell, I checked it and was surprised to find that the resistance changed during repeated testing – a sure sign that it had damaged contact points.
Testing of the switch was simple. By just bypassing the switch assembly, the non-working motor showed that the main problem was not with the switch.
After dissembling the motor housing, the commutator and brushes were examined. It was clear from the amount of carbon on the housing that the brushes would be worn. The segments of the commutator were darkened by years of arching and carbon build up from the brushes.
Next, the thermal fuse was tested and found to have continuity.
The armature was tested for continuity and shorts to ground and found to be OK. Testing of the field coils showed there was no open circuits or shorts to ground.
After removal of the brush packs, the fault became obvious – they had simply worn out and one brush had even worn past its end of life line.
A series wound or universal motor has only one path for current to pass. Therefore testing is relatively easy. Testing of the input and output wires will prove circuit integrity, checking all of the circuit in one easy operation. Of course it is important to check all components separately to ensure all sections are thoroughly tested. Complete testing would include the use of an insulation tester to check for any breakdown between windings in the field coils as well as the armature.
After purchase of a new set of brushes and a switch, it could be clearly seen how badly the brushes had worn.
Of course it is vital to clean the commutator to provide positive brush contact. Use of emery tape or sandpaper creates a clean, even surface.
Just ensure that any particles are removed and the segments are clean between the commutator. I used compressed air to accomplish this.
One of the advantages of a universal motor is that it can operate using either AC or DC voltage. So to test this motor, I simply powered it up using an old UPS 12 volt battery that I use for testing purposes.
This showed that the motor was now operating correctly.
Now was the ideal time to add tension to the power cord return spring by turning the cord around the retractor several times before refitting it to the housing. This will ensure that the cord returns all the way back into its socket.
After reassembly of all components, only I final thing is required – the dreaded road test!
If you are interested in this repair, you can see a video on my channel following the link below.
This article was prepared for you by Mark Rabone from Australia.
Please give a support by clicking on the social buttons below. Your feedback on the post is welcome. Please leave it in the comments.
P.S- Do you know of any your friends who would benefit from this content that you are reading now? If so, forward this website to your friends or you can invite your friends to subscribe to my newsletter for free in this Link.
Note: You can check out his previous repair article below:
https://jestineyong.com/how-to-repair-fish-tank-led-light-bank-with-video/


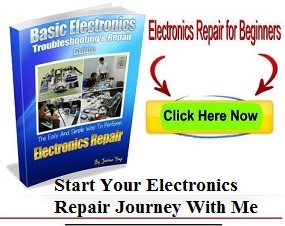
Parasuraman
August 27, 2018 at 6:19 pm
Very good informative article! Well done!
Mark
August 27, 2018 at 9:47 pm
Thanks for your comments Parasuraman
Albert van Bemmelen
August 27, 2018 at 7:23 pm
Dyson is known for its inventive new designs but this motor with old carbon brushes looks nevertheless very dated technology wise. And those brushes can still be rather expensive to replace. Good job that you were able to fix it!
Mark
August 29, 2018 at 5:24 am
Hey Albert,
From the research I have done, these older motors seem more reliable and have a stronger output than the newer ones. Actually, the brushes for this model were very cheap. But yes, I assume the later ones may use a brushless system now.
Thanks for your comments
Mihai
August 27, 2018 at 8:14 pm
Hello Mr. Mark, very informative article ! Thank's for sharing.
Mark
August 29, 2018 at 5:27 am
Thanks, Mihai
Rich
August 27, 2018 at 8:42 pm
Nicely done.
Mark
August 29, 2018 at 5:28 am
Thanks Rich
Robert Calk Jr.
August 27, 2018 at 9:56 pm
Good job, Mark. Thanks for sharing the repair with us.
Mark
August 29, 2018 at 5:29 am
Thanks Robert
Henrique Jorge Guimarães Ulbrich
August 27, 2018 at 10:44 pm
No transistors, no ICs. Anyhow, a very interesting maintenance work. That´s why Jestine´s site is so interesting. Very good, Mark. Thanks for sharing.
Mark
August 29, 2018 at 5:30 am
Yes this was an electrical and not an electronic repair, but I figured we all have repairs that we can share and benefit from.
Thanks for your comments Henrique.
Liviu
August 28, 2018 at 5:47 pm
Mark,
To clean the commutator better use a commutator cleaning chalk.
Mark
August 29, 2018 at 5:32 am
Thanks Liviu,
I will keep that in mind for the next repair.
YOGESH PANCHAL
August 30, 2018 at 2:26 pm
Good job! Mark
Justice (City of Durban --South Africa)
August 30, 2018 at 4:01 pm
Explicitly explained, nice work Mark thanks