Amazon Kindle Fire 2017 7th Generation Tablet Repair: Part 1!

My son had two Amazon Kindle Fire 2017 7th Generation tablets given to him by a friend because they would not charge their batteries. He asked me if I would take a look at them. I received one of them the first day that I will call Tablet1 which was dead and the battery would not charge.
A few days later I received the second one that I will call Tablet2. The battery wasn’t dead in it when my son received it and it played well with no issues. But when the battery went dead, it would not charge.
The USB Micro B charge port jacks really looked pretty bad, as you can see in the photo below. I figured that new charge port jacks would get these tablets charging again. I was wrong.
Above, I am opening up Tablet1. I have my DMM thermocouple taped onto the digitizer so I would not overheat the glass with my heat gun. I had the heat gun on low and it only took about five or so casual passes around the tablet to get the glass to about 130⁰F.
Heating the tablet helps soften the adhesive to make the tablet easier to take apart. The backs are not glued down on most tablets that I work on, but it is glued on this model. But it is not too bad.
I used my steel spudger to get into the gap and pry back the edge of the back cover so I could put the blue picks in. I started at the top right corner loosening up the adhesive a little, and then worked down the right side. When the temperature of the glass went down to around 90⁰F, I would heat it back up to 130⁰F again.
After I loosened up the adhesive all the way around the tablet and placed the picks, I then carefully went around again loosening up the adhesive until I started undoing the clips and loosening the back cover from the body of the tablet.
Just be careful and take your time and you should get the back cover off without breaking any clips or cracking the edges of the back cover.
You can see Tablet1 in the next photo with the back cover removed and lying beside the main body. After you remove the battery connector, you can take the other three connectors loose, unsolder the speaker wires, and remove the other screws. Then you can remove the motherboard.
The two photos above show Tablet1 opened up, and a close-up of the connecting side of the PCB in Tablet2. Below you can see the other side of the Tablet1 PCB.
Above is a top side close-up of the charge port jack. Below is a photo right after I removed the charge port jack on Tablet1. I forgot to take a photo of it after I cleaned the pads up better.
Above, you can see the new charge port jack after I soldered it onto Tablet1. Below, you can see the new charge port jack soldered onto Tablet2. Notice that I got a little bit of solder on the Tablet1 test pad marked, “VCHG”. That is a good way to tell them apart from each other so that I don’t get them mixed up.
The bar that goes across the back of the charge port jacks make it nearly impossible for me to use a soldering iron without getting solder everywhere. So I decided to use solder paste and my hot air rework station at 340⁰C using 40% air with my 8mm tip to solder them onto the boards, with my board preheater set to about 200⁰C. They turned out looking great!
While I am on the subject of rework station settings, I hear people all the time asking what temperatures and air settings that they should use. The correct answer is that it depends on what kind of rework station that you have and what you are soldering or removing with it.
Some rework stations have a fan blower for the air and some, like mine, have an air pump for the air. My rework station is an Aoyue Int852A++. It just takes practice with your rework station to find out what the settings are that work well for you and what size tips work the best for each job.
Plus, I don’t like holding my air tip too far away from the board. I like to see where my tip is pointing, especially when looking through my microscope. But it is the heat that matters anyway IMHO. Also, when you use a preheater, your rework station can use less heat. So, concerning air, I start low and increase it when I need to. But I will try increasing the heat before I try increasing the air.
I am very happy with my microsoldering – I am starting to get pretty good at it! And I always use my board preheater when I can.
As I mentioned at the beginning of this article, replacing the charge port jacks on the tablets did not fix the no-charging problem! So I removed and checked the SOD923F-2 ESD/TVS Protection diode marked, “PB” that I replaced with, “5P” – Part# CPDQC5V0CSP-HF.
The “PB” ESD/TVS diode in Tablet1 tested good with a basic zener test but I decided to replace them anyway. They are inexpensive so I decided that it would be better to not take a chance on the originals and just replace them. Plus I could not find a datasheet for a SOD923F-2 component with the marking code, “PB”.
The two SOD923 fast switching diodes beside it marked, “T4” – I replaced with Part# CMAD6001 TR that have the marking code, “Q”. They are right behind the charge port jacks. You can click onto the links to see their respective datasheets.
The “T4” fast switching diodes were testing to be good using my DMM’s and Zen50 until – “Close your eyes, Albert” – I checked them with my BK Precision 114A VOM (Volt Ohm Meter)! Ha-ha!
A lot of people, including our good friend Albert, think that the analog VOM’s are obsolete and not needed anymore in modern electronics. Well, I am going to prove them all wrong, right now! I found a through-hole diode a year or so ago that passed with my digital meters and failed with my VOM, but I lost it.
I am not going to lose these SMD diodes that check the same. Yes, it is not very common that this happens – but it still happens! And like Murphy’s Law says, “Anything that can happen – will.”
In the photo above, you can see that I have my tweezer leads on one of the “T4” diodes. I have Kapton tape over the metal surface of my Omnivise to keep the tweezer tips from grounding out and Rodico putty helping to keep the tiny diode from disappearing into the ether.
The negative lead is on the anode of the diode and the positive lead is on the cathode. I have a rubber band holding the tweezers together to free up my hands.
Rodico putty is not conductive as far as I have been able to tell. I have tested it to 1KV using my insulation tester with the leads a half inch or so apart. And it had no reading. And at 1000V it can read resistance up to 19.9GΩ.
You can see above that my Brymen shows “OL” in diode mode as it should if the diode is good, or if it can’t tell that the diode is bad.
Above in this photo, you can see that the VOM on X10K is showing a reading, which is normal since this VOM has reverse polarity, as most analog VOM’s do, and the negative tip of the tweezers is on the anode of the SMD diode.
In the photo above, you can see that the diode is turned around with the negative tip of the tweezers on the cathode of the diode, and the positive tip on the anode.
We can see in the photo above that the DMM is reading a Vf (forward voltage) of 0.8097V which is what we would expect for a good diode. That measurement also is within tolerances according to the datasheet.
And in this photo above we can see that the VOM is showing a reading when it should not show one since the negative tip is on the cathode. That means that the diode is leaking and the Brymen did not catch it! Neither did my Fluke 87V or my Peak Atlas Zen50 catch the bad diode! Only my VOM caught it!
So if anyone tells you that the VOM that has X10K (which means that it also has the 9V battery included along with the two AA batteries for a total of 12V) is obsolete and not needed in modern electronics, just show them this article! Now you can find faults that others will miss!
Had I not believed Mr. Yong’s teaching and believed all of the naysayers against VOM’s instead, I may have wasted a lot of time and eventually just threw the tablets into the junk bin. Thanks Mr. Yong for your great teaching and incessant willingness to help us out when we need it!
The VOM is also useful testing tiny components, like these SOD923 diodes, for pass/fail when you are looking through your microscope at the same time. You can see the needle on the meter swing when it is showing a reading out of the corner of your eye using your peripheral vision and you don’t have to stop looking into the microscope.
I should not have to remind yall how difficult it is to hold the test leads onto those very tiny components. And the tabs on them are not difficult to break if you are not careful.
I have gotten to the point that I don’t even waste my time checking diodes with anything but my VOM, unless I just want an accurate Vf. But I only trust my VOM when testing them to see if they are good!
It is also advisable to check transistors, MOSFET’s, and bridge rectifiers etc. with your VOM, as Mr. Yong advises in his great E-Books, because they have diode junctions. And if your DMM misses a bad diode junction, your VOM (with X10K) will catch it!
After replacing the diodes and the EDS/TVS diode in the tablets, the tablets would still not charge their batteries!
I knew that I would be getting power through the new charge port jack and components, but the batteries were still not charging! I suspected that the USB Charger IC’s were probably blown also. So I removed the boards.
Above, you can see the original USB charger IC Part# BQ24296M in Tablet1 after I removed the EMI/RFI shield that was covering it (the shield that I pointed out to you above in the fourth photo of this article). You can click the link to see the datasheet of the USB Charger IC.
I used 480⁰C, which is the maximum temperature for my rework station, with 50% air and my 8mm tip to remove the EMI/RFI shield. My board preheater was set to around 200⁰C, so the bottom of the board was probably actually about 90⁰C.
That is the highest air that I ever use to desolder/solder anything because if I tried to desolder an IC using 50% air with my rework station, I would be blowing capacitors and resistors all over the place!
I went ahead and ordered some new USB charger IC’s with the same part numbers and started removing the original ones without even bothering to test them. I need the practice soldering IC’s anyway.
Above is Tablet2. You can see that I pulled a couple of pads while wicking away the solder. I bought some epoxy overcoat CW2500 and a copper foil sheet to repair them with.
The repair of the pulled pads on Tablet2 will be in Part 2. The pads are very tiny so if it proves to be too difficult to use the copper foil, I will just use some wire.
But I would like to try and make the pads look like they were never pulled just for the practice and experience if I can.
I managed to wick the solder away on Tablet1 without pulling any pads, as you can see in the above photo. Where did that toothpick come from? The toothpick makes the IC look pretty small. The 24-VQFN Exposed Pad IC is only 4mm X 4mm.
Above, I have made putting the solder paste on the board look pretty sloppy. You can see the new USB charger IC on there and ready for some hot air. I was using a needle to put the solder paste onto those tiny pads. I need to get some stencils!
In the photo below, you can see the new IC soldered onto the board. I had my rework station set at 340⁰C with 30% air using my 2mm curved tip. My board preheater was set at 200⁰C.
My board preheater heats the board by convection. So when the preheater is set to 200⁰C, the bottom of the board is actually only about 90⁰C because most of the heat flows around the edges of the board and escapes.
I can mask around a board with Kapton tape to retain more of the heat if I need to, but that usually isn’t necessary. I wouldn’t want to get the board too hot and start melting the camera connector anyway. I did forget to remove a camera one time and melted it a little bit…oops.
After the solder was wet and the IC was settling down onto the pads good, I removed the hot air to put some flux around the IC. I heated the IC back up again and then gave it a little tap with my tweezers to make sure that it was wetted good and would settle back onto the pads and was soldered well, and then removed the hot air.
You can tell in the photo below that I am a firm believer in using plenty of flux. I believe that it is much better to use too much flux than to not use enough!
I then turned the temperature of my preheater all the way down, while leaving the unit on, so that it would let the board cool down slowly. That will help cut down on the chance of introducing thermal shock to the components and board as much as possible.
I probably didn’t have to worry much about thermal shock with this board, but I believe in developing good work habits! My advice is to always try to practice developing good work habits! When you practice good work habits enough, they will become automatic and you won’t even have to think about it.
You can see a photo of one of the boards on my preheater above. It seems like a lot of people don’t worry about thermal shock and do not use a board preheater. My opinion about it is, why take the chance?
Using a board preheater also makes hot air rework a lot easier since the board isn’t wicking away the heat as much as it would without using a preheater. It also means that you can use less heat for your work with your hot air since you are not losing so much of the heat from the board wicking it away. That has been my experience.
As you can see in the photo above, Tablet1 is charging great! I hope you guys enjoyed the article and I will see you in Part 2 soon!
Robert Calk Jr., is a Hobbyist from the U.S.A. that loves Electronics Device Repair. Please leave any comments or suggestions that you may have below. Thanks.
P.S- Do you know of any your friends who would benefit from this content that you are reading now? If so, forward this website to your friends or you can invite your friends to subscribe to my newsletter for free in this Link.
Please check out his previous repair article below:
https://jestineyong.com/brand-new-csi-station-2-in-need-of-calibration-and-servicing/


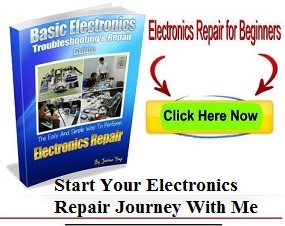
Anwar Shiekh
July 1, 2019 at 8:33 pm
When I risk pulling pads I prefer to call it a day
Robert Calk Jr.
July 1, 2019 at 11:26 pm
I just got in too big of a hurry. Thanks for commenting, Anwar.
Albert van Bemmelen
July 1, 2019 at 8:55 pm
Great job Robert! You did not give up after replacing the charge port connectors and replacing the diodes failed to restore the charger function. I wonder if replacing those diodes was necessary although you probably are right in using your VOM in testing those. I do not own a VOM or a surely useful Pre-heater but in case of any doubt on one of my digital semiconductor testers, I also can use the DY294 or other testers to test for any leakage. (Maybe a VOM creates those leakage currents because of its much higher internal battery voltage?). I also own a couple of the Peak Atlas meters and I always use more meters to confirm any measured result. And in case your diodes were of the protective tvs kind they probably indeed were damaged because they likely blew up the charger chip. A very professional repair Robert, especially replacing the 24-VQFN 4mm X 4mm IC. Your next article on the repair of the pulled pads will be a very interesting read for us in case we also wicked away any copper pads, which I think is always the most dangerous job after any chip or component is removed.
Robert Calk Jr.
July 2, 2019 at 12:47 am
Thanks Albert! I don't know what they did, but someone hit those tablets with some high voltage or caused a short or something trying to get the batteries to charge! The diodes are only pennies a piece so I would just replace them anyway.
I will test all four of the diodes and see how many are defective the same as the one in the article. I will buy some tweezers and modify them for my DY294 and include it in Part 2. It needs some tweezers anyway! Good idea Albert, thanks!
Right now I only have test leads modified for the DY294.
The VOM is a 3V & 12V insulation tester basically. It gives a better test at 12V (X10K) than my Brymen or Fluke will at 2 or 3 volts in diode mode.
For me using my board preheater just makes Rework easier no matter what anyone thinks about thermal shock, which mainly affects SMD capacitors according to my understanding about it.
When it comes to diode junctions I trust my VOM more than any of them. And Peak Atlas should have put 2mm connectors on all of the meters so we could change tips. I don't know why they would want to hamstring their devices.
Parasuraman Subramanian
July 1, 2019 at 11:17 pm
Marvelous service work there! Very elaborate and time consuming intricate work completed with the tenacity of a tiger! Well done!
Robert Calk Jr.
July 2, 2019 at 8:49 am
Lol! Thanks Parasuraman!
Randy
July 2, 2019 at 8:50 am
Nice job, Bob! I remember when you first started out here on this board doing electronic repairs, you have really grown in the complexity of the repairs you are doing now, nice!
Robert Calk Jr.
July 2, 2019 at 12:21 pm
Thanks Randy! I do not like to be called Bob but I realize that you don't know that. Yes, I have been trying to learn. But I am just a hobbyist and don't get a lot of devices to work with.
Most people would not spend the time on some devices like I do. But I try to learn from them even if they are not really worth the time and cost.
But I enjoy it! It gives me something constructive to do rather than just watching TV and playing video games all day like some people.
beh
July 2, 2019 at 10:28 am
ROBERT thank you so much for your very useful and comprehensive article specially about preheating of the PCB while we want to have some desoldering on it. here I am struggling with a LENOVO TABLET 5500 and its charger ic no BQ24196. your article is a great help for me.
Robert Calk Jr.
July 2, 2019 at 12:35 pm
Thanks Beh! I am glad that it helped you. I just replaced the digitizer on a Lenovo Tab E8 Tablet and it was the most difficult one that I have done so far. The back not only had adhesive around the edge, it also had a 2mm glue strip around the outside of the LCD screen to the digitizer! Maybe I should have made an article of it too?
Don't hesitate to ask me if I can help you with anything.
beh
July 5, 2019 at 10:37 am
since these machines are not made for repair after one time use you see how they sealed with glue and other stuff to make it impossible for repair. god bless you ROBERT.
Robert Calk Jr.
July 5, 2019 at 8:45 pm
God bless you too, Beh! The glue just makes it more difficult, but not impossible. You just need to use some heat, sometimes a few drops of alcohol, and be careful.
Yogesh Panchal
July 4, 2019 at 4:09 pm
Good job Sir,
For Removing charger IC Sometimes becomes tedious job if you do not have proper hot air gun. some technicians using Micro Butane torch like this
"Blazer GB2001 Micro torch"
https://www.youtube.com/watch?v=uz-_ROIn0bM
it's attainable temperature will be about 2,500°F.
you just have to do practice because temperature is vary on certain distance from flame.
Robert Calk Jr.
July 5, 2019 at 6:15 am
Thanks Yogesh! I removed the Charger IC very easily in less than 20 seconds. I have a butane torch but I would not use it on a PCB unless I had no other choice.
Adeleke Abel
July 5, 2019 at 4:12 am
Well done sir Rober for the comprehensive article. Very elaborate. I currently changed the same USB charger IC (24296M) on an Itel tab as the tab will not charge and noticed that the IC was getting hot when I plugged the charger in. After changing the IC, the tad started indicating charging but the power on the battery was reducing, I don't know what to do from here, any help will be appreciated
Robert Calk Jr.
July 5, 2019 at 2:13 pm
Thanks Adeleke. I have never heard of that before. I would suspect that something went wrong soldering the IC - maybe too much solder on the exposed pad is shorting to some pins. I would put flux around the IC and reflow it. If that doesn't fix the problem, I would remove the IC, replace it with fresh solder, and see if that takes care of it.
Ghashaan
July 5, 2019 at 4:54 pm
A long read with full of gems for newbies like me! Thanks
Robert Calk Jr.
July 5, 2019 at 8:27 pm
You are welcome, Ghashaan!
SHUBHAM PANCHAL
November 8, 2023 at 9:38 pm
Hi sir, May I know the part number that you used to replace the charging port connector?
Thanks.