Fabricating Bracket and Altering Speaker Connections In Philips Amp
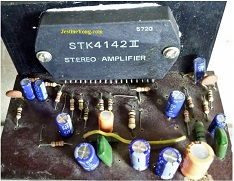
This Philips Amp belonged to my school class mate, to whom I had serviced an HMV Radiogram. During one of my friendly visits to his home, while the restoration of HMV Radiogram was in the final stage of completion, he mentioned about this Amp lying unused for a long time, as the output was distorted, after a modification of its Amp section by a technician.
After finishing the preliminary cleaning work, I opened the set. This amp, as you can see from the pictures that follow, being a discreet Amp, used transistors in its output. But these were removed and STK4152/II was used in its place. When I checked the board, I could see a lot of dry solders and ‘sick’ looking electrolytic capacitors, which proved to be really sick on ESR and capacitance tests later. The original Philips speaker connectors were bypassed by loose wires hanging out; there was no knob holding bracket for one of the graphic equalizer controls. The Amp was in a very bad shape altogether that any other commercial technician would have recommended ‘scrapping’ it! But, people like us who are hobbyists, take up such challenges, as it provides enough thrills at the end, which is the real fueling factor for us!
But, here again, I do evaluate whether my work would be rewarded by regular use by the owner or would it go waste by getting dumped in one corner after the excitement of reusing an old device dies. I either decline or receive and dump such sets at my end. There are another set of guys, who pick up all sorts of rotten things they come across, whether they really need it or not. I discourage such people, by neglecting their sets, keeping it in one corner, and giving excuses of one thing or other if and when they follow up. But these should be dealt with tactfully so as not to offend or spoil the relationship. So, that plugs such receipt of sets, taking undue advantages. Well, these are certain royal choices available only to hobbyists like us!
Started my most favorite work of replacing the electrolytic capacitors, starting from the Tank Capacitors. I replaced the 2500/100V caps with 3300/100V, as I was not having these nor were it available in the market. Removed the STK PCB module, replaced the electrolytic capacitors, patched up dry solder and cleaned it to the extent possible. Removed the graphic equalizer board and input board and did the same thing there also. Unfortunately, many of the Philips old sets do not indicate the polarity of the electrolytic capacitors on the board, because of which, we need to mark it manually each time before removing and ensure that the marking made is clearly visible and further do not get erased by mistake while cleaning the area, after removing the cap. All the boards, i.e., Main, Front Control and input board were all in bad shape due to dry solders and dried flux.
Took up modification of the speaker connectors, by replacing the Philips outputs with spring loaded one. Since the speaker connector bracket had provision, I also added two fuse holders to house protection fuses at the output. I did this, as I know from my experience with STK ICs that it can fail at any time, upon which, the working voltage would leak out to the speaker. These fuses would reduce the chances of speakers getting damaged, though not a complete solution. The fuse would blow, when large amount of DC current flows through it, as a result of the loads drawing heavy current then.
Now for a very interesting, challenging and amusing work that of fabricating a bracket to hold the knob in graphic equalizer board. I picked up a tin sheet, cut it using a special tool and shaped it the way another good one looks, bent the end portion, and applied solder in certain places to reinforce, and made it holding properly after several trials. Inserted a heat shrink sleeve where the knob was to be fit.
and also the portions that make contact with the plastic while moving up and down. You might also observe that the bracket looked like a gun! Now the pictures would speak. First you will notice the missing knob, then one of the real brackets, which I removed as a prototype. The last picture shows after it was placed in position. I fixed the knob at ‘balance’ position, as it will be used very rarely, and adjusted it after applying input signal and observing the wave forms in the oscilloscope and left it and also marked its position. Because, all said and done, the fabricated bracket was not as exactly as it should have been. The position was only very slightly shifted, and made no significant difference in view.
There was a blank or hollow portion where the function switches were housed. The knob with its outer cover was missing. I picked up one of my metal brushes, which had more or less the same shape, removed the bristles and wanted to fix this as its missing long knob. But while engaged in this, noticed a similar knob lying under my rack in front. My memory was this Amp was brought with one knob missing. But the one lying around looked similar and fit also correctly. Then I checked in the sets lying around in my rack and could not find any with missing knobs. (I also remembered to share this with my friend and mentioned that should there be a set with a missing knob when taken up later, I would remove this from his set and replace it with the make-shift-brush, which he agreed, as he was also not sure whether the knob was missing or not) Anyhow, I fit this there in its place. Then for the mask, I removed a plastic base of front board used in China Kits of CTV, which was lying in my junk collection, cut it and fixed it. Now the pictures would speak:
Then I fixed a cooling fan for the STK to keep it ‘cool’, as I know from my experience that this is a critical part that could fail any time due to overheat, though claims to be auto shut off in excess temperature.
The first picture what you see above is after I fit back all the board after finishing the work. Then I added the Fan, fixing it close to the Heat Zinc, tying it tight to the bottom.
Tested the Amp continuously for hours together and after it passed all my tests, handed it over to my friend, who was very generous in pouring a lot of admiration, which I valued and took pride with very much!
From my articles of such tedious jobs, you would have guessed that I would naturally sit on a set for days together, without taking up anything else in-between, which can be compared to software developers who are given a task. But the only difference is, they might have a set time target, but I do not have!
So, let me not forget to say that this jumped into my satisfaction bag by itself, before I could finish! Though I had taken the snaps of removed components, I could not find it in this folder. Looks like that is also misplaced like the knob! (LOL)
This article was prepared for you by Parasuraman Subramanian from India. He is 69 years old and has more than 30 years’ experience in handling antique equipment like Valve Radio, Amps, Reel Tape Recorders and currently studying latest tech-classes conducted by Kerala State Electronics Technicians’ Association. He has done graduation in BBA degree, private diploma in Radio Engineering and retired as MD of a USA company. Presently working as Consultant to Hospital and other institutions.
Please give a support by clicking on the social buttons below. Your feedback on the post is welcome. Please leave it in the comments.
P.S-If you enjoyed reading this, click here to subscribe to my blog (free subscription). That way, you’ll never miss a post. You can also forward this website link to your friends and colleagues-thanks!
You may check on his previous repair article below:
https://jestineyong.com/bad-diode-sb3100-found-in-samsung-lcd-monitor/


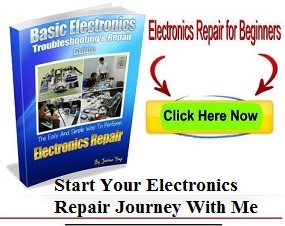
Albert van Bemmelen
November 5, 2018 at 3:49 pm
Your patience and skills are as always awesome Parasuraman!
The way in which you take care of repairing electronic devices that are in a really bad shape is unsurpassed! I first thought that you restored the amplifier back to its original transistors/mosfets, but I noticed you kept the STK module. So the engineer who made that modification did something right although he wasn't able to finish the job successfully. And checking and correcting the previous work done by others without any schematic is never easy!
Robert Calk Jr.
November 6, 2018 at 7:36 am
Good job, Parasuraman. You are right that we hobbyists will sometimes take on repairs that most techs would not.
James
November 6, 2018 at 4:43 pm
It's like watching the real McGyver in action, :[) LoL brilliant'
Humberto
November 7, 2018 at 12:34 am
You are a Master Mr. Parasuraman.
Henrique J. G. Ulbrich
November 10, 2018 at 5:24 am
Good, Parasuraman. I enjoyed very much reading your repair report. Keep on and thanks.