How To Repair Charging Problem In Samsung Smart Phone

Hi!
Yesterday I got a PCB from a customer who told me does something is wrong with this because the phone will not charge.I took the job and checked what type of PCB it is, made visual inspection and repaired. So simple was that. The PCB is a sort of board from a cell phone Samsung GT-I9301L.
Actually I put the board under my digital microscope. It is a very complex board with SMD parts on it. SMD is standing for Surface Mounted Devices, that means the parts are almost all of them are soldered on the surface of the PCB, not a through hole soldering technique.
I realized very fast the problem, two broken legs on the charging connector. But here we come to the simple but big problem.
Many of technicians would say, what about of garbage I say. Just let solder that two legs back and everything is fine. That would be easy and fine, but after an “easy” leg soldering the whole pcb can result in a bad pcb and a more expensive repair cost. And then we have a very nice problem done by the technicians.
So, here is what is going on:
– we have two legs to solder
– one of that two lags is connected to the ground ( here comes to the problem )
You have a small leg with a maybe 0.5mm diameter and a soldering iron tip of max diameter 0.5-1mm.
But you have the whole board as a cupper het sink. Whatever heat you set up to the soldering station, the small surface of the tip of the soldering iron is not enough to overcome the cupper surface of the gnd and can’t melt the soldering wire.
Maybe you can get some sort of melting but that would be a very bad join and I assume it would brick in a short period of time.
Most of technicians make two big mistakes.
- When they realize ( after 30min of trying ) does they can’t make a nice and good solder because of the mentioned problem, they take another solder gun with a bigger soldering tip and transfer more heat to the leg.
Yes, that’s nice. But I saw in several cases shorted connectors, and a molted connector after that kind of repairing. Because the inner side of connector is some sort of plastic. And most of the connectors are some sort of plastic where are the pins fixed.
- They take the hot air soldering gun and try to reheat the whole connector.
That results in most case in a damaged connector and very common in a damaged board.
With the hot air gun you can melt the connector, overheat the pcb, and in some case also can overheat some very sophisticated ic’s who didn’t like much heat. Sometime it’s possible to transfer more heat to sophisticated ic’s what the ic’s can’t handle through the ground traces too, which can damage the ic, even they are not near where you blow the how air…
Here is what I prefer for everybody to overcome all this problems and end the job in a short time.
I will suggest all the time, when you deal with a pcb where are SMD parts and you have to make some precise and complicated repair, to use the so called “Pre-heater”, check on the Net where to buy one or you can also make one. You can also prepare the board in a pcb vise and preheat the pcb with your hot air gun and then make your soldering but quickly. I soldered also the pins by preheated pcb until this repairing. Don’t overheat the pcb, just pre-heat. The temp of the pcb should be maybe around 100-150C.
Use always a pcb vise when you deal with SMD soldering. If you put your pcb to a desk, it could drain down the temperature from your pcb and your soldering work can be hard. The desk, bench whatever under the pcb can act as a heat sink plate. Never forget to use liquid soldering flux or flux pen! This will come very handy to make nice and clean soldering.
The pcb was sent back to the customer and after he put it back to the phone he sent me a message does the phone is actually charging. The board is repaired. Mission successfully completed!
The focus in this article was actually not about a simple repairing, the soldering of a bad join, but more on the technique I use, which is I assume on a proper way. The meaning of this article was to transfer some experience what I collected and the price I “paid” for the last 20 years, and to share my technique for the future generations who are at the beginning.
I hope you enjoyed this tutorial and will save lot of repair time.
This article was prepared for you by Christian Robert Adzic from Novi Knezevac-Serbia.
Please give a support by clicking on the social buttons below. Your feedback on the post is welcome. Please leave it in the comments.
P.S- If you enjoyed reading this, click here to subscribe to my blog (free subscription). That way, you’ll never miss a post. You can also forward this website link to your friends and colleagues-thanks!
Note: You can check his previous post in the below link:
https://jestineyong.com/how-to-build-your-own-rs232-to-ttl-converter/


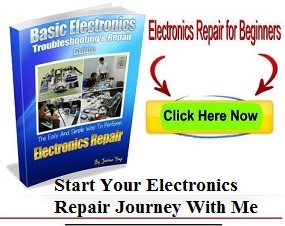
Bjonn
September 30, 2017 at 5:37 am
Thank you, very good advise.
Thank you for sharing!
moshe jacobson
September 30, 2017 at 8:20 am
very nice christian!!
thank you for sharing.
what preheater do you use?
Chris
October 3, 2017 at 5:33 pm
Hi!
Thank's for supporting my article.
I use two type of pre-heater.
1. In the lab I use Metcal PCT-1000 from OKI most of time.
2. At home I use my hot air soldering station.
I have many years of experience on this field and I
simply pre-heat my pcb by hand with my hot air solderer.
In this case, you must be very carefully not to overheat the pcb.
Keep in mind, the max pcb temp should never go over around 150C.
My best regards.
Albert
September 30, 2017 at 9:34 am
A pre-heater can be very handy Christian if needed. Special preheaters are also often used to easily replace broken glas touchscreens from tablets and smartphones. Thanks for the good advice. Using solder paste instead of using plain solder also may be a good idea when it involves soldering small smd components?
Chris
October 3, 2017 at 5:24 pm
Hi!
Thank's for supporting my article.
From my experience, using soldering paste is a "must"
when it comes to smd part soldering.
There is now place to use a plain solder wires.
My best regards.
Parasuraman
September 30, 2017 at 10:11 am
Very, very useful information! Preheating pcb is news to me! A big thank you, though I do not undertake such tiny devices for servicing!
Robert Calk
September 30, 2017 at 1:53 pm
Good job, Chris. I love my flux pens! I need to build myself a pre-heat table. Most I've seen on the Net are pretty expensive.
Yogesh Panchal
October 1, 2017 at 12:11 am
christian, Good Job!
Muslin
October 1, 2017 at 11:42 am
Thank you for that wonderful and educative info, Am a beginner ad my challenge is sometimes the articles are full of technical acronyms which put me on sidelines.
Thank you
Justice
October 2, 2017 at 3:20 pm
Thanks a lot Christian and Albert's comment, your educative experience is what is key and needed by the all new beginners like myself.Pre-heater is also new to me, thanks a million.(from South-africa)
Ulises Aguilar Pazzani
October 26, 2017 at 9:24 am
Good after noon Mr Adzic. nice repair ,Sir I got to cell phones with charging problem put away going to check them out ,thks forthe information
ombra32
January 12, 2018 at 8:04 pm
Very useful! Thanks!