Replacement Of Polarizer Sheets In Acer Monitor Model X163W

I saw a few monitors lying unused in the hospital where I work, because of the bulged polarized sheets. I took one of them one day and tried replacing the sheet assuming that the only top sheet was in this condition. I bore with the stinking smell of this sheet, which I heard is poisonous too to touch and inhale the emanating smell. Of-course, I was wearing gloves and a mask too!
The stinking smell soon spread around my house causing discomfort to my wife who was in the recovery stage after a mild stroke. After removing the torn sheet, and removing the solidified gum, using gum remover spray and IPA and a sharp blade, the surface became clean:
Then I fit the panel on the monitor frame and connected LVDS cable and applied power. I was sad to see that even the bottom sheet was in a bad shape and needed replacement!
That meant not only I may have to go through the unpleasant experience but also put my wife to difficulty. So, I set it aside and carried on with other works.
But when the hospital ran out of standby monitors as one by one reached this condition, I decided time had come for me to rev up and attack the looming problem as my intervention was found as a desideratum or need of the hour.
Though I requested my techie friends to offer any help, none responded as doing such a laborious work spending hours together enduring the unbearable smell and possible risks cannot be recovered in the form of a decent monetary return because of the availability of very cheap monitors in the market. Well, I, for that matter, am different and am always fueled to propagate in progression in such situations and surpass such an imbroglio. Having aroused my inherent instincts and now poised to fetch positive results, I combed the area looking for a vantage place to go and do the skin replacement work on the panels. I remembered that one of my close techie-friends, who had decided to call it a day and gave up his shop to someone else, found sitting lonely in the home was really a torture and opened another shop near to his house, which was only a few KMs away from my home. I thought that was the ideal place to do the ‘butcher’s job’ on these panels. Then I collected four such monitors and went to his shop on one of my off-days, taking due permission to do so, fully indicating the associated troubles which he might have to put up with. But he gave me a green signal and offered a warm welcome. He was focusing only on AC, Washing Machine and Microwave Oven Boards and his customers were mostly from the techie world. He made special arrangements for me by offering a vacant computer table and making arrangements for my seat without hindering his work or his clients. He offered help also as and when found necessary. I took up the work on this monitor first, as only the back sheet was to be replaced. I spent hours together on cleaning up the surface in which he too participated during short breaks, which gave me relief to recover from the dreariness. I had to use a good amount of the glue remover and number of tissue papers following it up with fine cleaning by use of IPA too. Though I had carried blades for scraping the hardened gum, he too went out and bought paper knives and a paint scraper used by painters, which were found very useful and effective. The method is to apply the gum remover solvent, wait for a few seconds and then start cleaning from one corner using a sharp blade held in 45 degree angle not to cause a scratch on the glass panel. Then the gum would peel off in flakes and we need to be careful when we are in and around the COF area not only to ensure that the solvent get into the bonding but also not to cause an accidental tear by the sharp blade we used. The peeling should be supported by frequent spray of the solvent and IPA too occasionally. When I used the pushing method, my friend used the drawing method from the other side, while holding the panel tight enough not to cause a wiggle. This was to avoid a clash of blades when hands of both of us reached the centre. Well, finally the panel looked clean and shined like a mirror. We need to ensure that not a single dust of any kind is stuck on the panel when we paste the polarizer. I used a 32” TV front and back polarizer films.
The method for fixing the film on a monitor is different from that on a TV. The angle of the polarizer might be different in monitors because of the high resolution and sharpness required. Fixing the film on the backside of the panel can be easy as we only need to take exact measurements and cut it and paste it. The film has clear protection sheets on both sides; i.e., the sticker side and the other side. The film for use in the rear and front are different. So, normally I get it marked by the supplier in order not to spend time finding out which one is what. I removed one rear sheet which I had carried with me, and placed it on the panel, marked all the four sides by a black sketch pen and cut the sheet to the correct size using a pair of sharp scissors. Then removed the protection sheet from the top and with the help of my friend, who held the film in position, I gently removed the protection sheet from the sticker side and placed it horizontally on one side of the panel, applied pressure with my fingers and held it in place. Then slowly and progressively, applied pressure using the putty applying tool mentioned earlier, while my friend synchronized the action by releasing the protection sheet from underneath. Slow and steady wins the race is what the old adage says and that was true in this case. A few times we had to peel the film in order to remove the bubble formed in spite of all precautions taken. Anyhow, the sticking of the film was completed within a few minutes, upon which both of us took rest to give time for our hands and senses to recover from the fatigue caused by focus and concentration. Now you might guess why the technicians are reluctant to take up such jobs! We took a lunch break and I returned home for refueling the body and he went to his. After finishing the food quickly both of us rejoined at his shop and kept the panel on top of the frame and applied power to check whether there were any visible marks on the panel. There was none. Remember that the front film was yet to be fixed and no picture could be seen at that stage.
Then we kept the front side film and checked the angle at which we got a good image of the multicolor pattern. Luckily it was ok when we kept the film vertically. So once again I went through the process of marking the film and cutting it to size. After that, we two managed to fix the film on top of the panel like how we did earlier. By this time, the experience made things easier for us too. He too was familiar with sticking films on car windows and his knowledge helped me too! I brought a glue remover-cum-panel film fixer (scraper) picture of which is given below. The blade of this is stainless steel and blunt so that we can use it for removing the hardened gum and for fixing the film by sliding it over it applying adequate pressure for bubble free finish.
We did the fixing of the film keeping the panel connected with LVDS cable an on its seat inside the frame. After cleaning the surface with IPA, we applied power and were glad to see the crystal clear contrasting image! I brought it home and fixed it on its case and fixed the stand too. A word of guidance about this stand: The stand has two screw covering rubber covers without removing of which, we cannot see the mounting screws. These can just be plucked:
After fixing the stand, I applied power feeding a signal from my VGA checker, about which I have already covered in my earlier articles. Don’t you all join me in my joy to see the results?
Mission accomplished with astonishing results because of which the satisfaction got itself glued to the collection! The IT Administrator was more than happy to see the finish and the new look of this lovely monitor and shared the following photo (second one) after fixing it on a counter. I collected only a nominal charge from the Hospital just to cover my cost as my techie friend strictly declined to accept any payment from me for the time spent and assistance provided.
This article was prepared for you by Parasuraman Subramanian from India. He is 74 years old and has more than 30 years’ experience in handling antique equipment like Valve Radio, Amps, Reel Tape Recorders and currently studying latest tech-classes conducted by Kerala State Electronics Technicians’ Association. He has done graduation in BBA degree, private diploma in Radio Engineering and retired as MD of a USA company. Presently working as Consultant to Hospital and other institutions.
Please give a support by clicking on the social buttons below. Your feedback on the post is welcome. Please leave it in the comments.
P.S-If you enjoyed reading this, click here to subscribe to my blog (free subscription). That way, you’ll never miss a post. You can also forward this website link to your friends and colleagues-thanks!
You may check on his previous article on Restored A Service Declined Board Of White-Westinghouse Humidifier Model WDE401


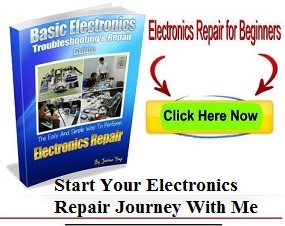
Waleed Rishmawi
November 30, 2024 at 2:17 pm
that is a lot of work and smelling stuff to be going through but you made it happen..good job and have a blessed day
Parasuraman S
November 30, 2024 at 5:20 pm
Yes, a lot of work, but the result compensated for it! Many thanks for your comments, dear friend!
Anwar Yunas Shiekh
November 30, 2024 at 5:12 pm
Amazing work, requiring great patience.
Parasuraman S
November 30, 2024 at 9:23 pm
Many thanks, dear Anwar!
Albert van Bemmelen
November 30, 2024 at 7:22 pm
I have no idea what this repair was all about dear parasuraman. Because I didn't even understand what exactly was wrong with those screens and how that had happened? And I really think that you shouldn't have taken such risks of doing stuff like this to begin with!
Because as you know and also most likely written in Jestine's and other tv repair e-books the warning that the plasma in tv screens is very poisonous. Like also the mercury in those old backlight cfl tubes.
And our health is more precious than the condition of any very degraded tv or monitor! Also because a new monitor can be bought but not our health even if you work your good deeds for any hospital! And I would hate to see you leave this blog because of a last repair you successfully fixed!
Parasuraman S
November 30, 2024 at 9:38 pm
First of all many, many thanks for your comments showing how concerned you are about me, though we live in different parts of the globe. Shows the humanitarian side of you! Let me try to answer some of your doubts to the best of my ability: (1) Please visit this site to know more about LCD screen and its parts: https://electronics.howstuffworks.com/lcd.htm. (2) Then see this video:https://www.bing.com/videos/riverview/relatedvideo?q=how+to+replace+polarizer+film+on+monitors&mid=63F438771E992D8D1A0463F438771E992D8D1A04&FORM=VIRE
(3) I just replaced both the polarizer sheets from behind and front side of the panel. The sheet is self sticking type and the gum on it gets dried up causing the sheet to peel of due to heat and ageing.
I have written one more article with more details with stage by stage snaps taken on another polarizer replacement case that might clear any further doubts you might have.
Once again, it was very nice of you to have offered your cautions! My countless thanks, dear Albert! Your words 'And I would hate to see you leave this blog because of a last repair you successfully fixed!' really touched me!
Albert van Bemmelen
December 1, 2024 at 3:16 pm
Thanks very much Parasuraman! I've saved that youtube video and the webinfo about replacing those sheets for future reference. But I do not think that those new sheets for that matter are even available here? But it is clear why you said: 'though we live in different parts of the globe'. Because even defect transformers get serviced where you live, which is a non existing service in my country!
Parasuraman S
December 1, 2024 at 9:03 pm
Yes, true. Many countries disuade board level servicing and promote board replacements or set replacement itself. There is a lot of difference in developing and developed countries. Even in India, things are changing drastically and many electronic technicians are diversifying or looking elesewhere to meet their daily needs! I know many have opted to become autoriksha or car or van drivers!
Mark J
December 1, 2024 at 4:07 am
Parasuraman whatkind of VGA checker do you use? Great job on the repair.
Parasuraman S
December 1, 2024 at 10:14 am
Dear Mark, I have mentioned about this in my previous articles and have also shared its photo. Kindly see this: https://jestineyong.com/servicing-coby-lcd-tv-monitor/
Albert van Bemmelen
December 1, 2024 at 3:50 pm
You can also easily make such a VGA screen tester with a cheap PIC microcontroller circuit. Like this one => http://wiki.pic24.ru/doku.php/en/osa/articles/vga_terminal
I made this one that originated from a Russian designer who used an 12MHz overclocked PIC16F84 microprocessor. From which the website doesn't exist anymore apparently? But I have the circuit and the PIC hex code if someone needs it. This vga tester with up and down push buttons to select the vga test => https://www.amazon.com/Comimark-Signal-Generator-Display-Tester/dp/B087LZ5Z7Z
Albert van Bemmelen
December 1, 2024 at 3:58 pm
Here you can also find a matching 3D case design for the mentioned VGA signal generator screen tester =>
https://www.thingiverse.com/thing:4350438
Albert van Bemmelen
December 1, 2024 at 4:25 pm
I just found the link to make the vga tester from Alexandr Musatov here =>
http://www.ebastlirna.cz/modules.php?name=News&file=print&sid=159
Mark J
December 2, 2024 at 9:47 am
Albert thank you again for the information.
Parasuraman S
December 1, 2024 at 9:07 pm
Thanks, Albert for providing more information on VGA tester.
Parasuraman S
December 1, 2024 at 9:09 pm
Thanks, Albert for providing this information.
Mark J
December 2, 2024 at 9:45 am
Albert thank you for the information and the web page link.
Parasuraman S
December 2, 2024 at 4:52 pm
Many thanks!
Mark J
December 2, 2024 at 9:42 am
Parasuraman thank you for the web page link.
Yogesh Panchal
December 1, 2024 at 6:48 pm
Excellent!Repair with so much effort.
Changing the polarizer film is a very difficult task. It works at a fixed angle so we have to take film that is twice the size required. When we serve others our health comes first because we also have someone dependent on us.so my request to everybody to take care of your self & take proper health precaution while repair/Service .
Parasuraman S
December 2, 2024 at 4:51 pm
Many thanks for your lovely comments and advice! Taken to heart! May God bless you!
PHILIP
December 3, 2024 at 11:22 pm
Good material article, thank you. As I read on I thought as usual you would pass the panel problem to your techi friend who lives 20 km from your house. But you were overcome by a strong passion for your proffession and went ahead to dismantle the panel yourself, the toxic gases notwithstanding. I believe that in some dangers that we (many proffessions) expose ourselves to, protection comes from devine intervention. Think of this, I'm an untrained techie but some years ago, without being aware of the deadly high voltage I surprisingly handled or mishandled for that matter several sets of CRT TVs without being zapped. Also, I hope you find enough time to keep our mum company as she recovers from the mild stroke, I wish her well.
Parasuraman S
December 5, 2024 at 10:13 am
Very personaly touching comments! May God bless you, brother! Many thanks for taking your valuable time to post this! With the blessings of all of you and Jestine Yong (whose family is doing daily prayer for our sake) she is getting better and is able to handle the kitchen work alone with very little assistance from me! This blog is a window for universal love for each other and sure, the blessing for that should go to our Jestine Yong, who is in fact, many may not know, is doing a yeoman service!