Someone Asked How to Find Dry Solder Joint

50% problems in Electronics are because Dry solder of components. (Sharing here some example photos collected from google Search for reference). A dry solder joint is a soldering defect that occurs when the solder does not properly wet or adhere to the component pins and PCB pads. It results in a weak and unreliable electrical connection.
Factors such as insufficient heat, oxidized surfaces, improper soldering, or using low-quality solder & Solder Flux cause dry joints. Proper soldering required to Heat up circuit Trace & component pin at the same time with proper temperature which suit quality & type of the solder wire.
However, a cold solder joint is an imperfect connection formed when the solder fails to melt properly, resulting in a weak bond between Component & circuit board traces.
It’s often characterized by a rough or lumpy surface – cracks may also develop in the joint over time. Or some Disturbances happened such as vibrations between the board and the component when the solder is cooling.
Most old leaded alloys (Solder wire) made shiny joints.
The new lead-free alloys usually make dull joints, and that’s normal. (Dull solder shine sometimes miss lead us as a Cold or dry solder when Lead-Free solder is used). we need to refresh the solder applying Flux & leaded solder.
Here are some examples.
For confirming dry solder on through hole components like Electrolytic Capacitor, Mosfet, transistor, diode etc…, put your one hand fingertip on suspected component solder joint side pin & using your another hand gently move or shake the component from top of the component, you will feel movement on your finger tip on solder side if component pin is dry solder.
Sometime we need Magnifier Glass or microscope to find out Hairline crack in solder joint. Instead of wasting time if you have doubt just refresh the solder joint applying good quality flux & solder wire.
For proper soldering follow the tip…
Soldering Process step wise.
This article was prepared for you by Yogesh Panchal who works as a Computer Hardware Engineer in Mumbai India.
P.S- Do you know of any your friends who would benefit from this content that you are reading now? If so, forward this website to your friends or you can invite your friends to subscribe to my newsletter for free in this Link.
Note: You can check his previous repair articles on No Display In Samsung Syncmaster 933SN Repaired


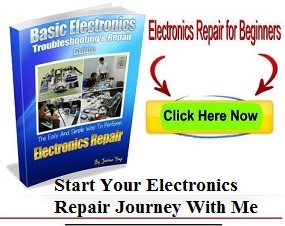
Albert van Bemmelen
September 7, 2024 at 8:00 pm
Finding dry solder joints indeed is gotten harder after the solder changed from lead/tin based to lead-free tin/silver solder.
But I guess that in case of doubt it never harms to re-solder over any questionable solder joint. And at home I still mostly use the 60/40 based tin/lead solder for the best joints.
Anwar Yunas Shiekh
September 7, 2024 at 10:26 pm
I also have a stock of 60/40 solder for repairs
Yogesh Panchal
September 9, 2024 at 2:28 pm
Best Combination Anwar bhai
Yogesh Panchal
September 8, 2024 at 6:18 pm
Albert,
I also use 60/40 solder wire which is having flux inside the core of the wire.
Kevin Davison
September 7, 2024 at 8:27 pm
Very concise and well put together. An excellent series of explanations!
Yogesh Panchal
September 12, 2024 at 10:25 pm
Thanks!Kevin
Parasuraman S
September 7, 2024 at 9:18 pm
That was a wonderful article for which you have put a lot of efforts to collect data. Very nice of you to have highlighted the need for proper solder! Many thanks, dear Yogesh!
Yogesh Panchal
September 8, 2024 at 6:19 pm
Thank you! Sir
Mark J
September 8, 2024 at 2:17 am
Yogesh good article. Thank you for sharing.
Yogesh Panchal
September 17, 2024 at 10:53 pm
Thanks!Mark J
Anwar Yunas Shiekh
September 8, 2024 at 5:44 am
What is the best flux for repairs?
Yogesh Panchal
September 8, 2024 at 6:24 pm
Anwar Yunas Shiekh,
You can use rosin flux for through hole components & for the SMD Components Try AMTECH -559-V2-TF there are some new products also available.
GIFT ELIJAH
September 8, 2024 at 6:12 am
A very interesting topic that has been neglected by most techs, thanks very much for reminding me that blowing after soldering is a bad practice. Correction is noted and bad habits of blowing will be stopped. Special thanks.
Yogesh Panchal
September 8, 2024 at 6:27 pm
Thanks! GIFT ELIJAH,
More practice is required for SMD Soldering in mobile & laptop repairing.you can practice on junk PCB.
PHILIP
September 9, 2024 at 1:58 am
You certainly couldnt have been more elaborate Yogesh. The entire demonstration with nice drawings beats a video lesson by far. Please allow me to add that a small steel-wire brush is such a necessity that constanty gets rid of the never ending dust accumulation at the tip of the soldering gun, which otherwise prevents full heat transfer to the soldering wire to melt effectively. And I remember once Albert adviced us to adapt the habit of using a face mask as soldering wire smoke is harmful when inhaled. And how about putting on gloves to prevent burning our fingers? Burning fingers is what makes us sometimes to blow to soothe them
Yogesh Panchal
September 9, 2024 at 2:45 pm
Thanks! for you input Philip,
you are right Philip,steel wire brush is very useful for cleaning soldering tip rather using File tool or sand paper. which shorten the life of soldering iron tip.i personally use utensil scrubber steel.as far as fume is concern it is toxic for health always use Fan to exhaust or blow to keep away fumes from inhaling.using gloves depends on personal preference & personal comfort.
Jose
September 11, 2024 at 8:41 pm
I was one of the ones that asked about cold joints. Many thanks Mr Panchal for a very clear and thorough article.
Yogesh Panchal
September 12, 2024 at 10:26 pm
your welcome Jose
Hilario
September 29, 2024 at 6:37 pm
Hi,
This is very good article and I appreciate alot.It is possible Send This article in PDF so I can download please.
Yogesh Panchal
October 2, 2024 at 5:27 pm
Hilario,
Thanks! for your comment.
just open the article in Google web browser Select highlight the required material form google chrome give print command, in print destination select & save as PDF.