ATX PSU modified into a car battery charger- part 1
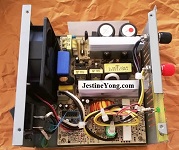
Some months ago a friend of mine gave me a main board of an old defective ATX PSU, just for me to use it as a spare parts source. All it was a populated PCB only. No covers, no cooling fan etc.
Well, some days ago, I had a phone call from my younger brother Aristos. He was explaining to me about some trouble he had with his car, specifically with a malfunctioning switch which recently left him with a totally flat battery, early in the morning, while he had to leave for work… During the discussion he started asking me about details in order for him to decide about buying a good car battery charger. Then I had the idea! To see what was wrong with that PCB I had available and instead of using it as a spare parts source I could possibly restore it and afterwards modify it making of it a 12V car battery charger for my brother.
You can see this PCB below:
I found all those missing parts from whatever salvaged I had available and managed to restore it in an acceptable final appearance of a PSU, after repairing and modifying it.
You can see below its final shape, after having completed all the modification work.
When I started troubleshooting it, I noticed that it had its fuse intact. That was good news, as I realized that it had a “not starting” problem.
I was very lucky so far and things seemed to be much easier now. I already had the good news that the primary switchers were intact. Nevertheless I typically proved this by taking static measurements on them. Everything was in perfect shape as I expected.
I continued with a fast check on the secondary side semiconductors, not expecting again to find anything wrong there. Just for confirmation that this side was trouble-free too. In addition I “scanned” all the electrolytic caps for bad ESR. No problem found.
Now was the time for dynamic checks. I connected the “soft fuse” (the test lamp) in series with the mains input of it and plugged it into the mains. I saw only a short glow of the lamp and then nothing. That was also a good sign. Next I checked the standby power supply, those 5V on the violet colored cable, and this was also fine.
The following voltage tests I run on the mains rectification and filtering were OK, my auxiliary (standby) PSU was already OK and the voltage to the PWM modulator IC was there, but when trying to energize it there was no signal at its outputs to drive the power transistors.
The PWM IC used in this PSU was the TL494, well known for decades now. As I recall the first time I saw this chip was back at the beginning of the eighties. At that time I joined the Panasonic servicing staff here in Athens-Greece. The actual IC was an equivalent version of that TL494. It was a μPC494 made by the Japanese company NEC. At that time I was so amazed by the way this power supply worked, after I had repaired it, that I bought some pieces of this chip in order to start experimenting with it…First love…never forgotten…This chip introduced me in the magic world of the SMPSes…Those were the days…
So I knew very well now what I had to do next. I checked all the voltages around the pins of this IC, in order to locate a possible “output inhibit” condition. Nothing relevant found by the measurements. The sawtooth oscillator’s frequency was in place, but the “5V reference” was missing and there was no activity at its outputs. So the decision was easy. This IC should be replaced. Indeed, after the replacement and connecting the PSU again to the mains (after bridging the free terminals of the green cable with a black one at the motherboard connector end, which equals the start command) the fan I already had connected to it started spinning. The indication that the restoration was already done was present. I further proved that by measuring its output voltages which were all at the correct level.
Next to that, since there was no further intention of mine to use this PSU for powering a computer even for a single time and in order to make things much easier in case of a possibly new repair of it in the future, I decided to strip it down removing anything that was not needed from the secondary side of the PCB. In other words I removed all the components related to the +5V and +3,3V outputs along with anything related to them and I saved these components as spare parts for future repairs. I left only the +12V output circuitry there.
You can see the almost naked secondary side of the PCB along with the components I removed, below:
However I had two basic problems to solve. The first was the output voltage.
As you know, in order to charge a 12V car battery one needs a slightly higher voltage than that. Otherwise there is no charging at all. The typical voltage used in cars is 14,4V. For floating use (keeping the battery permanently charged over time, in standby state) the typical voltage is 13,5V. So, I had to increase the voltage output of this PSU…
My brother on the other hand was very demanding! He wanted not only the boost charge function, but also the “maintenance” or “floating” one. Therefore I had to take this requirement in account and provide him with two switchable output voltages. One for boost charge, which I decided to be 14,7V and the other one, for the floating function, at 13,2V.
The second problem to be solved was the obvious need for an inclusion of a current limit protection in it, which would protect it against overloading and also against any accidental short circuiting of its output cable clamps before connecting them to the battery to be charged. Originally this PSU had not such protection circuits for any of its outputs. This explains the reason of the instant blow of various power semiconductors when these cheap designed PSUs either exceed their maximum power output capabilities or, especially, when their outputs face a short circuit.
Click HERE to go to Part 2
This article was prepared for you by Paris Azis from Athens-Greece. He is 59 years old and has more than 30 years’ experience in electronics repairs, both in consumer and industrial electronics. He started as a hobbyist at the age of 12 years and ended his professional carrier as a senior electronics technician. He has been a specialist in the entire range of consumer electronics repairs (: valve radio and BW TV receivers, transistorized color CRT TV, audio amps, reel and cassette tape recorders, telephone answering and telefax devices, electric irons, MW cooking devices e.t.c) working in his early stages at the official service departments of National-Panasonic first and JVC afterwards, at their premises in Athens.
Then he joined the telecoms industry, working for 20 years as field supporting technician in the sector of DMRs (: Digital Microwave Radio transmission stations), ending his carrier with this subject. Now he is a hobbyist again!
Please give a support by clicking on the social buttons below. Your feedback on the post is welcome. Please leave it in the comments.
P.S- If you enjoyed reading this, click here to subscribe to my blog (free subscription). That way, you’ll never miss a post. You can also forward this website link to your friends and colleagues-thanks!


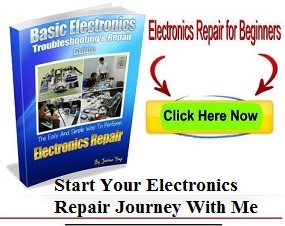
Humberto
April 14, 2016 at 9:39 pm
Hi Paris, I confess this article is very interesting, and I'm very eager for seeing Part 2
Paris Azis
April 15, 2016 at 1:09 am
Hi Humberto,
Thank you for your kind words. Just click the second part and see it. It's available.
Thank you also for the photos you sent me about the voltage level detector/protection circuit. I hope you received the answer I sent directly to you.
Greetings
Suranga Electronics Sri Lanka
April 14, 2016 at 10:44 pm
Hi. Mr Paris. Great Repair Article
Thanks for This.
Paris Azis
April 15, 2016 at 2:59 pm
Hi Suranga
Thank you for your support.
Best Regards
Parasuraman S
April 16, 2016 at 8:53 am
Let me be very frank; I can never venture to do anything like this on my own, because of limited knowledge in Electronics! But I am a very good 'copier' and perhaps emulate it in my own crude way! So, many thanks for this article, and hat's off to your knowledge!
Paris Azis
April 17, 2016 at 2:51 am
Thank you Parasuraman for your very touching comment. I really appreciate it. Hopefuly you can build your own charger! Thanks again!
Best Regards!
Dwayne Arthur
April 16, 2016 at 5:06 pm
Good work , I'm impressed with Your ingenuity.This reminds me of what I learned years ago when I was a consumer electronics student .
Once you know how a device or a certain block in a process works you can follow the signal flow , and eventually you can repair and redesign any device .
Paris Azis
April 17, 2016 at 3:05 am
Hello Arthur
Thank you for your kind words. It is obvious to me, reading the last phrase of your comment, that "you've got the idea".
Well, all I am doing is convincing every time myself that somehow there is no garbage in electronics...At least not all of any failed equipment which is available. Even a total dismantle of it in order to get healthy spare parts out of it is worth the effort (I believe).
This charger is therefore nothing else but a result of this thinking of mine...
Greetings