Systematic Repair On A Device With The Help Of DCA 75 Pro And Hand Drawn Schematic

I was asked to repair a not working Silk ’n Flash & Go hair remover. So I took it home. At first I had no idea how to open the device. So I looked for any information on the internet on how to disassemble this device but I couldn’t find anything whatsoever. And certainly no schematics or other related info.
Afterwards it took me quite some time before I finally was able to open the sturdy plastic housing. I found that the best way – and probably the only good way – to do this is to start disassembling the device by removing the bottom cap from the handle first! There are no screws used!
Above photos show the top view of the box, and the bottom label on the device with the power input jack for the 12V 3.0 Amp power adapter.
It is made in Israel and is just genius in design because it also uses a sensor to protect using the unit on wrong skin colors (safety sensor).
Previous 2 photos showed the 12V 3.0 Ampère adapter label and the inside box view. And this Silk ’n hair remover is sold with 2 removable heads, called cartridges. Next photo shows one of them.
The ‘laser’ head probably is filled with krypton or some kind of other gas that is activated when the high voltage reaches the tube and the conducting spiral around it. The transparent light conducting plastic ‘eye’ below the tube is the light conducting plastic to the safety sensor on the inside board that protects from using the head on wrong skin types.
On next photo the top view control panel is shown which worked perfectly but the tube simply refused to flash when the button in the handle was pushed. Only the + and – energy level control worked (3 horizontal active green leds shows maximum energy setting). And also the on/off standby button control worked splendidly too.
The heads called ‘cartridges’ plug into the front of the inside board by a small printconnector. And they can easily be replaced if they are defect. The whole device looks a bit like a model from the star ship NCC-1701A from science fiction series Star Trek. And after examining the internal electronic design it just as well could have been a design from the future! And next photos will show how the device looks after the bottom cap was removed and after the control panel with all electronic components was extracted. Only the special high voltage Photoflash capacitors are placed in the handle with the power input jack and the push button. And to remove and open the plastic case only clips need to be unclipped. And the purple push buttons top is partly glued with tape. After all photos also a small circuit will explain how this well designed hair remover system, that also uses a TDA 4862G PFC controller chip and a 44 pins PIC16F1939 microcontroller, exactly works.
Last photo showed the circuit around a transistor with smd code A2 next to the HV coil. And a thyristor Q5 a CR08M 600V 0.8A was shown. Both tested okay.
I was able to let the build up energy flash into the head by carefully connecting pins 1 and 2 (cathode and anode of thyristor Q5) manually with a screwdriver. But it never worked by pushing the button on the handle. Here follow some DCA 75 Pro test result photos of mentioned transistor with code A2. And a closeup of that circuit on the bottom pcb side after the transistor was removed for testing.
And because also the with my Peak SCR-100 tester tested CR08M thyristor was not defect, I continued the search for the not working heads.
It could be something to do with the safety sensor D3 but testing that component would not be so easy! And testing the TDA 4862G wasn’t easy either. Also testing the two precision Opamps with smd code B48 (TI OPA2348 types) was hard because of the small size of the pins to begin with. Other components used were a 6 pin code 162F Q7 chip that probably was a transistor to regulate the Fan motor, and a FMMT 459 HV switching transistor that tested good, plus several RS1M diodes.
The 8 pin 78L05 regulator chip was working perfectly too because the TDA 4862G (on pin 8), the Fan, and a mosfet 340N08 (pins 5 to 8 all 5V) 80V 23A N-ch type, hard to get because often not available, all measured the 5V. And the control board panel and the leds all worked splendidly too. But probably depending on what manufacturer made the 340N08 mosfet it was 50V instead of the given 80V?
Checking the 340N08 mosfet Q2 in-circuit was not possible. Next photos show the result checked with the DCA75 pro after desoldering. In first photo I also removed the bottom Fan to check where the gate pin was going to by soldering a flexible red wire to its gate and measuring the top board side pins.
It was going to a resistor to pin 7 U1 (mosfet driver pin of the PFC controller TDA4862G). Following photos show that the mosfet was okay. So this was completely logical. But maybe it now never worked? There were quite a few test results given by pressing the right button on the DCA 75 pro.
So this clearly showed that also the mosfet was okay. And the mosfet conducting resistance was less than 1 ohm. Below the wires I soldered on its pins before I was able to test it.
Next photos show the safety sensor with the head plugin connector. The sensor has likely 3 color filters red,green and blue and is helped by the 2 side leds for brightness. After all in the dark there are no colors visible. The sensor is probably read with the firmware in the PIC controller with both precision opamps (TI, 8 pin ic code B48).
On above photo the Fan was removed to check for the tracks underneath and to find the gate connection to mosfet Q2 (pin4). On the left D3 (safety sensor) and led lights D4 and D5 are shown. Next circuit was made to analyze this complex design in order to find the culprit easier.
Conclusion: I couldn’t find any defect component. And before I had removed the 340N08 opamp Q2, I noticed that it was not placed in the center of its solder pads. So measuring if contacts pin 1 to 4, especially pin 4, were making real contact to the board was uncertain. But after I had placed it back correctly in the middle of the pads the device immediately worked! So it could have been a bad working mosfet. Why the wife of my friend’s father had not been able to use the Silk ’n Flash & Go device for a long time. But it was more likely because she was using the device wrong at a distance from her skin. So that the sensor can’t scan the skin and the ‘laser’ never triggered. And because that didn’t work she then also pressed too hard on the silicon rubber like buttons on the top panel which caused them to block and stick inside the panel, which I also had fixed.
When I already brought it back to her the very next day after she had given it to me, she was happily surprised it was working like a new one!
The CR08M thyristor from ON semiconductor in the drawn circuit looks like being connected wrong with Cathode and Anode in not conducting direction. But its pin configuration is exactly like the datasheet from ON semiconductor showed. And probably just looks wrong because not all connections to HV coil and thyristor and the HV transistor are drawn. And the coil also had 3 connection pins of which 2 were directly connected which could explain the odd looking circuit. But mosfet and thyristor are really connected as shown.
Although this was a very complex electronic device it was a very decent and safe made product. Even while it uses a dangerous high voltage circuit and intense streams of light that remove hair in a blast!
After this repair I patiently wait on a device that does the opposite to help me from getting any bolder (LOL).
Albert van Bemmelen, Weert, The Netherlands.
Please give a support by clicking on the social buttons below. Your feedback on the post is welcome. Please leave it in the comments.
P.S- If you enjoyed reading this, click here to subscribe to my blog (free subscription). That way, you’ll never miss a post. You can also forward this website link to your friends and colleagues-thanks!
Note: You can read his previous repair article in the below link:
https://jestineyong.com/osram-quicktronic-qt-1×58-modern-dimmable-fluorescent-light-repair/


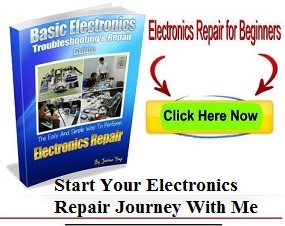
Gassan
November 16, 2019 at 4:44 pm
Lovely small device with a intimidatingly complicated circuit board! I wonder about how much it would cost!
Anyway, I loved reading the details of disassembling and troubleshooting. DCA Pro is on my shopping list now.
Albert van Bemmelen
November 16, 2019 at 7:07 pm
The Peak DCA Pro 75 is indeed worth buying! So is their SCR-100 tester, because it is able to also test all the higher gate triggered Triacs and Thyristors the normal cheaper testers never can test! And the ease of using these testers is also because they always work and are powered by one cheap alkaline AAA penlight battery instead of the more problematic 9V block batteries normally used in DMMs. (electronically switched off or pushed on/off, since a real off switch is absent. And to replace the battery we just need to open the tester by removing the back screws. I am still using the original 1.5V battery that was provided a few years ago).
Robert Calk Jr.
December 2, 2019 at 2:29 am
Hi Albert. I just found another component that passed with my DCA75 Pro but failed with my lowly little VOM. It is a #QM3016D - TO252, N-ch MOSFET.
Andrea Del Corso
November 16, 2019 at 4:56 pm
As usual a special repair with as many explanation very interesting.Many thanks !!8
Albert van Bemmelen
November 16, 2019 at 7:26 pm
Devices like these we indeed not often see in repair. Probably because they are still quite expensive and not the typical type of bodycare products most people normally would buy. Modern products like these are heavily controlled around complex firmware in a special designed microcontroller. Which makes fixing faults in that design impossible and limits any repair to component level repair only.
Parasuraman S
November 17, 2019 at 12:36 am
An exhaustive description of a strenuous trouble shooting done on a device, which I have never even heard of! The schematic looks like a computer graphic, what I mean, so perfect! Hat's off my friend! I am lost! Well done, might be a praise too meagre for a fantastic job like this!
Beh
November 17, 2019 at 12:57 am
New electtonic mashines are getting more and more complicated and most time the user do not know how to use the device they think the mashine is not working Albert i admire your courage for opening this machine because these machine are not made for repair congratulations for your discovery
Robert Calk Jr.
November 17, 2019 at 4:25 am
Good job, Albert! I have never opened up one of those devices before.
Devon Wilson
November 17, 2019 at 11:24 am
This is truly a great job. Fortunately, you're methodical and experienced in electronic troubleshooting. Thanks for sharing.
George Greenfield
November 18, 2019 at 11:11 pm
Great repair. You did good getting into the device ! A lot of time that takes the most time of all.
I too am a great fan of Peak hand held test equipment. I have all of them at my work place. Very handy..
George
Albert van Bemmelen
November 19, 2019 at 10:43 pm
I also have a lot more digital testers George. Including special ones for Optocouplers, Amplifier chips, Opamps and TTL/CMOS IC's. But for Thyristor/Triacs, and Transistors the Peak DCA75 with the integrated Curve tracer and the SCR100 are likely the best for that category! Although the DCA75 also tests Zenerdiodes upto 12V, and Regulators. But for that I also can use my DY294 semiconductor tester which can do that too and some other tricks.
beh
November 23, 2019 at 9:05 pm
Albert, please tell me what is your amplifier chips tester name? ......thanks ..beh
Albert van Bemmelen
November 25, 2019 at 8:54 pm
I may already have mentioned this one before Beh? See this link