Vibrograf B200 Mechanical Watch Calibrator Repair
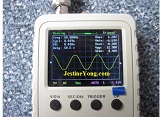
This repair is about a Vibrograf B200 mechanical watch calibrator. It plots the mechanical ticks of a watch on a roll of paper by picking up the vibrations with a special sensitive microphone and comparing that with an exact known oscillating quartz crystal frequency signal. Sadly fixing these about 45 years old devices (1974) is not easy because finding a service manual or even a complete circuit is very hard! We only found a document with a block diagram in it that merely showed how the boards where connected, which is not enough for functional analyzing what defect board needs fixing.
It all started when my professional educating watchmaker friend Charles told me that his Vibrograf (that I also successfully had fixed in the past some years ago) no longer worked after he had replaced the bulged e-caps he found on one of the boards in this machine. The motor no longer worked and he brought the Vibrograf B200 in for inspection. Next photos show the board with the previous bulged and now replaced e-caps.
He replaced those capacitors, two 220uF/40V and one 470uF/25V capacitor, after he started noticing that the volume adjustment of the amplified mechanical sound pickup sensor behaved erratic. But after replacing those capacitors and cleaning the inside of the Vibrograf B200 the motor and the volume control no longer worked. I started by examining the 10.560 KHz Quartz generator board. Below photo shows this board nr. 330.1140.1/910, and checked the output with my good old about 30 year Tektronix 2465A 350MHz oscilloscope.
For making this article acting more as a complete service document, I also added a view on the solder side of this board.
Next photos shows the splendid signal output frequency of this 11.12.75 dated board when connected to an about 20V DC supply voltage. So no worries there! Plus also a few photos that picture this great looking with Swiss precision made Greiner B200 device. Followed by the converter board, nr. 330.1140.860.13. Also top and solder side, that I checked on component level because checking these boards functional wise without any service manual is close to impossible.
I checked all resistors, diodes, capacitors and all transistors, and picture below shows all max Hfe values from every single BC182A npn transistor. Transistors red dot marked. Everything tested fine! After that I even checked all 7 TTL IC’s! (desoldered with my S993A desolder gun). All tested fine, the sn7472 on my 1995 ELV IC tester, and all others on my Elektor 1998 IC tester (only my old msdos ELV IC tester was able to also test the special 7472).
First of course I already had checked both fuses (one on the back) and one on next shown power board nr. 330.1140.880. I already had fixed this board in the past once by replacing the bad diode on the left of the 500mA 250VAC fuse. (the bigger 4th top diode on the right). Also here are board top and solder side shown.
Also this board was fine so I continued my search for the reason why the Vibrograf no longer worked. On next photo the transformer input selector, the manufacturer label and the T125mA 250VAC fuse on the back are shown.
Next I decided to check the switches and the tracks on the bottom board. By removing all screws and connectors. One of the connectors with board number 330.1140.710 was soldered on one copper pin to the bottom board with number 330.1140.820. And first had to be desoldered to avoid breaking any wire connections to the input plugs on the back.
The left input connector is for our pickup microphone to amplify the ticking of any mechanical watch. The DIN chassis on its right is for connecting a headphone.
Next photo shows the wired voltage input 120/220VAC selector with the 0.125A fuse on the right.
Above photo showed the transformer voltage connector with board number 330.1140.800 with date 1.9.75. Next diagram shows the voltages of transformer number 1140.780 and the voltage selector.
The voltage between both orange wires is about 43 V AC. And between both yellow wires about 8,7VAC. Both grey wires go to the 230V AC on/off switch on the 50 Kohm potentiometer on the front.
Previous 2 photos showed the complete bottom board solder side and a close up on the frequency selector switches with 28800 18000 19800 21600 selection modes. Next a close up on the Auto mode selector switch (the 2 x 6 pin row right below MMS marking).
Again every component, switch and copper connection tested fine. So I re-assembled the bottom mainboard back and re-connected all connectors to it. Of course I already had checked the 3 wire motor coil connections (one middle coil wire and 2 on the coil sides) with my Blue Ring tester and there was no internal short whatsoever. So the motor probably wasn’t causing the problem either. And all transformer voltages were fine and the 2 transformer coils with numbers 1140.790 and 1140.830 tested fine with the Blue Ring tester too!
So I focused on the third board, with number 330.1140.940 with date 7.8.75. Again viewed on component and solder side to be as complete as possible to make this a useful service document.
And this was the board on which my pro watchmaker friend replaced the previous mentioned 3 bulged e-caps. Again I measured every component and connection and even draw a circuit from it.
Again I couldn’t find any bad component passive or active. All transistors (all BC182A again!) tested fine when every single one was desoldered and tested with my Peak Atlas DCA75 Transistor tester. I even again wrote down the maximum Hfe current amplification factor of every BC182A in the drawn circuit. Hoping this way being able to analyze the not working Vibrograf B200 better. But it didn’t! Nothing was defect! But I did find the issue what caused all this after showing next board 330.1140.940 first!.
On above Amplifier board my friend previously had replaced the mentioned 3 bulged e-caps. Now nothing tested bad and nothing on this board was causing any problem.
Until I asked my friend about next issue I noticed. The fact that the 2200uF capacitor, and the 7805 regulator on the converter board measured no voltage at all. And before that I already noticed the strange way that the bottom board pins almost touched a leg of a diode on the Convertor board (860) and a coil on the Amplifier board (940) after which I had shown following photo on Messenger about this to him. His answer was that it probably was intended because it was Swiss made precision. See next photo. But still nothing worked (only the small light bulb next to the on switch in the 50Kohm potentiometer worked as it was supposed to). So I continued checking the 6V AC voltage.
Previous photo showed how I connected my oscilloscope probe to check the 6V ~ AC signal on the Mainboard. It was fine.
So I still had to figure out why there were no voltages when measured on the 2200uF and 7805 on the Converter board. Nothing was defect and still nothing worked.
The answer was surprising and could have saved me 2 days of testing, and was found when I read the webpage of this proud French Vibrograph B200 owner: http://www.pascalchour.fr/mesures/vibrograf_b200.htm
There I noticed that the previously mentioned and thoroughly tested Amplifier and Converter Boards were simply placed in the wrong mainboard connectors. I just needed to swap both boards and every question was finally answered!
That explained why nothing was amplified, the motor didn’t rotate, and no voltages were measured on certain parts of the circuits. So maybe my trusted friend was just testing my capabilities as repair engineer or he wanted to make sure to have a decent service manual at hand in case the device really starts to fail in another 5 years when it is 50 years old. And I’m just glad I was again able to help my friend and old colleague who I know had a lot on his mind lately. Especially in these Covid19 times!
I’m sure other Vibrograf B200 owners will be happy to know that this machine is made to probably last another 50 years! And to conclude this article hereby a few photos with the boards in the right place that show the again fully working mechanical watch calibrator. Luckily placing the boards in the wrong connector didn’t harm them in any way. Maybe Swiss precision even took care of that event?
Latest Update:


Albert van Bemmelen, Weert , The Netherlands.
Please give a support by clicking on the social buttons below. Your feedback on the post is welcome. Please leave it in the comments.
P.S- If you enjoyed reading this, click here to subscribe to my blog (free subscription). That way, you’ll never miss a post. You can also forward this website link to your friends and colleagues-thanks!
Note: You can read his previous repair article in the below link:
https://jestineyong.com/lacie-1tb-network-space-nas-repair/


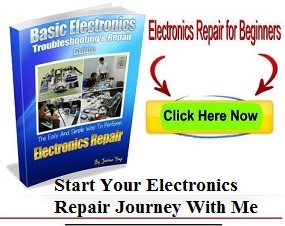
Yogesh Panchal
September 12, 2020 at 2:21 pm
Excellent! Repair Albert,
Good Home work before proceeding the work by marking components on the Paper and understanding the circuit on the paper before start the work when you do not have Schematics.
Fabulous condition of the PCB after 45 years.
Albert van Bemmelen
September 12, 2020 at 9:59 pm
You are right Yogesh! The old pcb boards indeed look like they were produced yesterday. Why they probably will still work after another 50 years or so.
Parasuraman S
September 12, 2020 at 5:44 pm
Voosh! What can I say? I am dumbfounded! Bowled down! What an amazing and unparalleled way of trouble shooting and solving! Oh My God! That too diagram manuscripts! Vow! I feel exhausted by reading the article itself! Excellent job there! Many thanks for sharing this sweating service!
Albert van Bemmelen
September 12, 2020 at 10:08 pm
Thanks Parasuraman! I however do feel a bit ashamed for making yet another very long space taking article while you are recently doing your best to make your articles more compact. I hope I am not the reason for that.
Parasuraman S
September 14, 2020 at 12:26 am
No, not at all! It is a very interesting reading! Articles such as yours should be descriptive and lengthy enough not to miss anything! You are sharing your knowledge, which is always a flow. It should be allowed to flow out easily! Well done!
I opted to make my article compact for saving time and efforts. But at times, they are lengthy as the case may be!
Mario Di Stefano
September 12, 2020 at 5:44 pm
Fantastic job!!!
Also the reverse - engineering job you did, if nothing less than SUPERB!!!
Thanks for sharing!
Albert van Bemmelen
September 12, 2020 at 10:17 pm
Thanks Mario! But of course I never would have had the chance to reverse-engineer this special device if my friend wouldn't have destroyed his important Vibragraf B200 unintendidly (twice).
Andrea Del Corso
September 20, 2020 at 9:09 pm
Eccellente lavoro,come al solito,bravo Albert,e,grazie per la condivisione.
===============================================
Excellent work, as usual, good Albert, and thanks for sharing.
Nigel
May 8, 2021 at 5:06 pm
Very enjoyable read, thank you for sharing & the detailed photos. Once explained, we can all see the original problem but as technicians, I'm sure we've all had many times when we've spent hours chasing a friend/customer-induced 'fault', rather than a real equipment fault!
If you get to work on this machine again, perhaps some labels or different colour varnish dots could be applied to each board & the the mainboard, to assist your friend with future board placement & orientation?
Guido Velásquez
November 17, 2021 at 6:25 am
Hello, brilliant job. I have an Elma Mini Test machine that stopped working. However, my knowledge of electronics is very limited. Furthermore, in our environment, it is very difficult to access spare parts. I have it in storage for when the opportunity arises. Maybe you want to help me.