NARVA LED Inspection Light Repair

The definition of wisdom is ‘applied knowledge’.
What has that got to do with an inspection light, I hear you say?
After one of my last articles dealing on battery replacement on a stick vacuum cleaner, the comments section below lit up with remarks stating that I should have not soldered directly onto the batteries to join them in series. Others stated that they, like myself, had never had problems in the past. Others said that the excess heat created during the soldering process may shorten the battery life. It was also stated that Lithium Ion batteries were very susceptible to overheating and can in fact burst into flames as I’m sure we have all heard happening in laptops and mobile phones.
So are we willing to learn from the years of experience of others? If we are wise, we will.
https://jestineyong.com/electrolux-vacuum-cleaner-battery-replacement/
One of the most helpful comments made was that batteries are available with tabs, spot welded by the manufacturer, attached so that the soldering can be done on the tabs rather than directly onto the batteries and help alleviate the heating issues.
So I decided to listen to the experience of others on my next project – battery replacement on a Narva LED inspection light (it seems like I am always replacing batteries, but they still need repairing or replacing).
The light is fairly simple in construction with 30 LED’s on a circuit board with individual resistors to create the LED drive voltage.
The crucial step to diagnosing this repair was to put the battery under load when testing. As you can see in the first photo, the battery was delivering the required 7.2 volts, however, when the battery was put under load, after the light was switched on, it very quickly dropped to an unacceptable voltage, where the lights could no longer operate and the charge light came on. This was despite the battery recently being on charge.
Rather than buying a direct replacement of the battery pack, I decided to build up the pack myself, adding individual batteries in series. Once again, thanks to others I was able to make the repair easy, safe and long lasting.
As with my other battery replacement repair, I once again decided to ‘Super-Size’ the batteries to gain longer operation times.
The original batteries were Ni-MH 1100mAh, so I replaced them with a higher available value – Ni-MH 1600mAh (designed to provide MORE POWER!!)
Now this is where listening to others comes in. With these ‘tab’ style batteries, two advantages quickly become evident.
- There was no need to remove the old tabs from the original batteries (a real pain!)
- Soldering the batteries in series was extremely easy, due to the fact that you are only heating a tab, not an entire section of the battery.
From experience I have learned to double check the voltage of the new batteries before soldering. There is nothing more disheartening than soldering all your new batteries into a pack only to find out that some of the new ones were faulty!
I also found it helpful to hold the batteries together when assembling with insulation tape. This makes the job of soldering much easier. Before assembly, a voltage test of the battery pack as well as testing the operation of the light before assembly is essential. In this case, the battery pack was assembled successfully and the light was at full power even before charging.
I guess the moral of this long-winded story, is that we should be willing to listen to others, since no-one knows it all. Thanks to this blog and other tutorials, I have learnt a lot from others with much more experience than myself.
Thanks!
If you are interested in a video of this repair, please follow the link below:
This article was prepared for you by Mark Rabone from Australia.
Please give a support by clicking on the social buttons below. Your feedback on the post is welcome. Please leave it in the comments.
P.S- Do you know of any your friends who would benefit from this content that you are reading now? If so, forward this website to your friends or you can invite your friends to subscribe to my newsletter for free in this Link.
Note: You can check out his previous repair article below:
https://jestineyong.com/samsung-p5110-tablet-touch-screen-replacement/


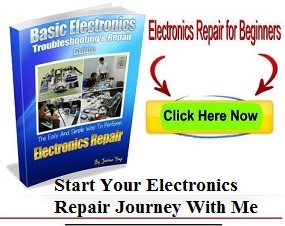
Yogesh Panchal
January 21, 2017 at 5:16 pm
Good Job! Mark.
PARASURAMAN S
January 21, 2017 at 5:24 pm
Wonderful! Informative article! Well done!
Albert van Bemmelen
January 21, 2017 at 7:22 pm
Thanks for the article Mark. Like you I'm very interested in replacing old Battery Packs by new Li-ions Batteries. And now I am starting to repair the Battery Packs of Laptops. Which not only involves replacing the old ones by new ones but also requires resetting the Eeprom in the Pack that protects the Li-ions and keeps track of its life span. The latter can easily be done with the program BE2Works but it does cost about $200 and a little adapter (The CP2112 USB interface that automatic will be recognized by Windows after plugging it in).
And of course I use a Spot Welder Machine (the 709A+) to make new Packs.
The demo program only reads the Packs by using the I2C protocol to read-out the Eeprom with the old Battery data. And the previous program was called Smart Battery Workshop and used an LPT interface that easily could be build.
I recently bought a Book at Biblio that gave following information on how to handle those Li-ions:
1.Charge Li-ions often, except if they are stored for a long period. And avoid deep discharges.
2.Keep Li-ions cool, avoid leaving them in a hot car.
Never Freeze Li-ions ever!
3. If your laptop can work without battery and usually works on a power adapter then remove the battery and store it in a cool place.
4.Avoid purchasing spare Li-Ions for later use. And keep the date of purchase. Do not buy old stock even if the price is attractive.
A lithium-based battery has no memory effect which means you never have to discharge them to maintain capacity.
Li-ion batteries prefer a moderate discharge. Partial discharges produce less wear than full discharges representing a cycle less the loss of capacity.
The decline applies to all batteries but most to Li-ion batteries.
A discharge of up to 80% is the value equipment manufacturers handle in their calculations.
Li-ions also wear when not in use. Save batteries preferably in a cool place and at a loading of up to 40%. Never fully charged and discharge Li-ion if necessary before storage.
15 degrees celsius storage temperature is the temperature at which the manufacturers store them at a loading of up to 40%.
A Li-ion battery has a time clock that starts ticking the moment it leaves the factory.
The electrolyte slowly eats the positive plate away in the battery pack.
Until the internal resistance is so high that the battery will not deliver power anymore.
Cheers !
Mark
January 23, 2017 at 7:26 pm
Hey Albert,
Thanks for all the informative information.
You would think that batteries would be a simple topic, but the more I read and learn, the more I realise how complex they are.
At the moment I am writing for a company over in Germany, developing an online training course for Electric Vehicles. These battery systems are extremely complex, with current sensors, voltage sensors, inverters, liquid cooling systems, regenerative braking to charge the batteries during braking & the list goes on! As an example, the Tesla S model uses over 7000 18650 batteries to create the battery pack! Amazing! Yet they are able to recycle almost all of the batteries.
There seems to be no end to the advancement of technology!
Gary Gemmell
January 22, 2017 at 12:55 am
Very true Mark I like your style!
Hmm for some reason Paris Aziz name and email address are appended to this input form - nevermind i have put my own in.
Albert van Bemmelen
January 23, 2017 at 4:40 pm
Jestine, please see my Post with the name of Parasuraman S in top after his article. That also went wrong in the way described. The e-mail addresses of others strangely popped up. They normally never do. Thanks! Albert.
Mark Tembo
January 23, 2017 at 11:07 pm
Thanks for emphasizing the usage of Solder flux. It's really very important!
Humberto
January 24, 2017 at 12:34 am
Great job Mark, congratulations.
Robert Calk
January 25, 2017 at 2:49 pm
Good job, Mark. Thanks.