Neglected Earth Wire Blew The Mosfet And PWM Of OSS Team Soldering Work Station T-12X

This was a proud addition to my tools and use of it each time brought more and more happiness as I was able to handle very difficult jobs of micro soldering and de-soldering very easily. After putting to use this and my KADA 2018D+, I had in fact given away around half a dozen of standard irons, keeping only one or two to be used in case of emergency. But having sucked in by this pride and the resultant amusements, I overlooked one important factor. This unit comes with a three pin main cord, which is of German model, with a female Earth pin along with two male pins for Phase and Neutral. As I was not having a mains cord with three male pins, I used this cable and totally forgot about it, engrossed and enthralled in the new experiences.
One day I was working on a CRT TV Board and while removing its two pin plug from the mains without switching off its two way mains switch, it accidently touched the case of this iron. I heard a loud noise and my T12-X went dead. I immediately realized what would have happened. The CRT TV like in any other SMPS circuits has AC Mains Filter Caps in the rails before and after the inductance transformer. This holds some charge for a few seconds even after switch off. This got discharged on to the body of the T12-X which resulted in its failure. In order to ascertain the extent of damage, I quickly opened the cabinet and found that the 3.15 A fuse was blown and the Mosfet was found cracked! Well, that cut my over-pride to acceptable standards! (LOL) The discharge would have upset the frequency driving the Mosfet beyond saturation point! I used my Kada Iron to remove the mosfet.
I saw a six pin IC reading the number as 63N05P used as its PWM. Though I searched for its datasheet in many places, I could not get it and when I sought help through my techie friends in the Whatsup group, one gave me the number as OB2263. Got its data from here OB2263 Datasheet PDF – Datasheet4U.com and traced the startup voltage pin. I replaced the fuse with a different type of fuse that is used in LED TV circuits. Then applied power and checked whether it was getting the voltage, and found it to be zero. There were series of SMD resistors from the B+ line reading the number as 153. Though voltages were seen up to the last one, it was zero after the last resistor, indicating a failure of PWM. The resistor was also getting warmed up. So I removed the PWM and got voltage there when rechecked. A few pictures are given below:
My next step was to check whether there were any further defective components. Ring testing showed healthy, with all LEDs glowing on the primary switching winding. Next step was to ensure that the iron would work once PWM is changed. So, I used the following four wire module and connected the Green wire to B+ (300V DC), black to its hot ground, and white to opto-coupler pin 4 and red wire to the run DC.
As per the instruction sheet that comes with this module, Green wire need not be connected, if startup voltage track and run DC track joins at the same place. So I had removed one SMD resistor reading 153 from the startup track to cut the startup voltage, as it is generated within the IC from the green wire connection that goes to from B+. Alternatively, you can give the connection to the original run DC pin and remove the Green Wire. I used a 11A 800V Mosfet and kept the drain pin straight for soldering directly to the board and bent the other two pins (gate and source) forward to solder the PWM Board onto it. Following pictures might be of more help:
Then fixed the Mosfet with its heat zinc to the main board. This is how it looked:
When I applied the power through a series bulb, the output was measured as 23.67V and when I verified this with the user manual, it was confirmed that this unit produces 24V for the iron.
So, I was confident to connect the front panel and checkup. It worked very well! So fit the boards back.
If we press and hold the knob for a few seconds, it will enter into settings mode. We can adjust various settings including language and I selected English. As for calibration, I had no thermometer that can withstand at-least 350◦C, I have to do it after receiving that I ordered. The method suggested is to keep the thermometer and see the reading and adjust the temp shown to match that, plus or minus 5 degree. All these are clearly written in the user manual with pictures that anyone can follow easily. I have ordered for the PWM IC and shall resort to restoration to the original condition, if and when the iron fails. For the time being, my repair was found sufficient enough!
Work accomplished and great satisfaction got added to its collection, trimming my pride to the required level and teaching me a good lesson too!
This article was prepared for you by Parasuraman Subramanian from India. He is 72 years old and has more than 30 years’ experience in handling antique equipment like Valve Radio, Amps, Reel Tape Recorders and currently studying latest tech-classes conducted by Kerala State Electronics Technicians’ Association. He has done graduation in BBA degree, private diploma in Radio Engineering and retired as MD of a USA company. Presently working as Consultant to Hospital and other institutions.
Please give a support by clicking on the social buttons below. Your feedback on the post is welcome. Please leave it in the comments.
P.S-If you enjoyed reading this, click here to subscribe to my blog (free subscription). That way, you’ll never miss a post. You can also forward this website link to your friends and colleagues-thanks!
You may check on his previous article on INTERMITTENT ON-OFF PROBLEMS SOLVED IN PHILIPS DVD PLAYER MODEL DVD625K/691


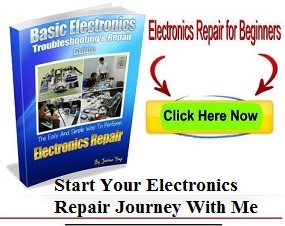
Hakan
December 31, 2022 at 2:27 pm
Hi,how can we find replacement numbers for example 0B2263 instead of 63N05P without your friens? Which method or Web sites help us on this matter?
Parasuraman S
December 31, 2022 at 9:23 pm
Well, I have no idea. These friends have attended many technical classes, from where they have jotted down the details, which they share to close contacts. Many thanks for your comments!
Imoudu.O
December 31, 2022 at 7:50 pm
Wow!!.I knew it's baba(meaning grandpa)acticle from the start of reading...unique.
Per pwm module used, it means wire green and red serves the same purpose.
Secondly what is the purpose of using mofet 11A 800V for? Thanks for sharing sir.
Parasuraman S
January 1, 2023 at 8:56 pm
That's to ensure that a replacement mosfet is better rated than the original to obviate any future failures. Many thanks for your comments!
Dan
January 16, 2023 at 2:59 am
A very interestin repair, A repair well done, where can i buy the 4 wire PWM module to replace the mosfet. do you have a websitefor it?
Ravi
January 8, 2024 at 3:15 am
There are two mosfats what is the job of another mosfat.
And what is the number
Albert van Bemmelen
December 31, 2022 at 8:22 pm
Another very interesting repair that involved using a universal 4 wire PWM module Parasuraman! I still must take on using one of those in the near future too, but I'm not sure if I already have the module you used here. The T12 soldering iron is I beleave a well known newer soldering iron. I have one or two of those on my 709A Spot Welder and other stations for finer smd work. The T12-x station you used is however new to me.
Parasuraman S
January 1, 2023 at 8:59 pm
Yes, dear! It is recently introduced and now widely preferred and used by technicians. It is one of the best I have used so far. Very quick to get hot and ready to use with temperature control. Many thanks for your comments and encouragement!
Waleed Rishmawi
January 2, 2023 at 3:59 pm
good job on the repair. I was glad the damage was managable. thanks for sharing and have a blessed day
Parasuraman S
January 3, 2023 at 1:03 pm
Many thanks for your continued support and encouragement!
Mathew Charles Karonga
January 4, 2023 at 3:09 pm
Greeting
Thanks for sharing such a well detailed article.
We always have something new to Learn from your articles.
I do appreciate you willingness to pass your knowledge to the next generation.
Stay blessed
Parasuraman S
January 4, 2023 at 7:19 pm
Knowledge will only increase by sharing! Many thanks for your comments!
Yogesh Panchal
January 8, 2023 at 10:54 pm
Good Job!Sir,
Proper Tools make our job more enjoyable.As in last article you used a microscope for micro jumper work.
Parasuraman S
January 9, 2023 at 12:27 pm
Yes dear! Many thanks for your comments!
Hollis LuQuette
January 16, 2023 at 2:17 am
Those style soldering stations are great tools to have, the KSGER is a close cousin to the X types, they all are 24 volt T-12 style irons.... The bad thing is the Earth ground is not connected to the aluminum cases because of the coating on the cases.... Buddy with The Radio Shop on you tube and John Salt have great video's explaining the issue and show how to remedy that issue...I don't have a soldering station like those but I am saving up for one ...
Bala Chandar
July 26, 2023 at 10:35 am
Thank you very much Parasuraman for your detailed article on troubleshooting the the power supply of OSS Team T-12 soldering station. I had exactly the same problem with my Team T-12 X-Plus model and your detailed article was a huge help in making my soldering station functional again.
I am describing what I did and that may be of help to some. I ordered ES-55 Version 2.1 PWM module from easyspares.in (Rs 60 + shipping). Removed the damaged MOSFET 10N65C and the PWM IC 63N05P. Soldered MOSFET 11N80C and the module board the way you have done, connecting all 4 wires to the right spots. The 33uF 400V filter capacitors were not damaged but I replaced them with 33uF 450V caps for a higher safety margin. Since the 450V caps are slightly taller, they had to be fixed in the horizontal position. Replaced all four M7 diodes of the bridge rectifier.
Sunil
October 31, 2023 at 5:38 pm
I want to ask that what is the value of the smd resistance which placed between gate to source of 10n65c Moffett bcoz the smd resistance burn and i am not able to find out the value plzz help