Blomberg 19” LCD screen TV/ Monitor with intermittent shut downs, repaired
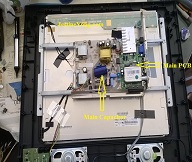
A friend of mine who owns this TV set asked me to take a look on it as the set was shutting down its function while being in normal operation and this was happening irregularly. The set’s front view is shown below.
I took it home, installed it in a place and put it in operation. To my surprise the set was functioning normally for more than one week and I thought that my friend had a problem in his electrical installation at the power receptacle. Nevertheless I hesitated to call him at that time and preferred to wait for some more days.
Well, after one more day the set started to shut down repeatedly and irregularly. The problem was already there. I opened the set removing its back cover. This below is its internal view.
I had repaired this set once again two years ago. The set had blown the input fuse and the input smoothing capacitor, right after the line rectification, due to a power line overvoltage. In a strange way, all rectifier diodes were intact at that time. The capacitor I replaced is the big blue colored one, attached horizontally to the power supply PCB. At the right side of the power supply, is the main PCB.
Below you can see (limited) information about this set.
I started troubleshooting with the verification of the various voltages around the set and found them all right. I was then oriented towards the system control IC. It was not possible for me to find relevant information for it in the web.
Anyway, I found a similar IC and I guess that both of them are produced from the same company. The type of the one I found was MST 776-1 while the one I searched for had more and different digits after the first 77. Unfortunately I didn’t take a photo before the repair so that you could see this I.C now. The photos you see were taken when I finished with it.
I suspected that something is wrong with this I.C, but I could not prove it taking measurements as usually, due to the lack of any information. Then I applied the “finger-as-thermometer” test on it. Well, fortunately I reacted instantly removing my finger from it avoiding a serious scald. This IC although working perfectly, it was doing so under marginally overheating conditions.
I turned the set off waiting for it to cool down. Right afterwards I turned it on again and put on the upper surface of this IC a K type thermocouple connected to an ordinary multimeter switched to thermometer function. Its indication jumped to 72 degrees Celsius within two minutes of operation (!!) and stabilized there.
I realized that the IC shuts down due to activation of an overheating protection circuit, but still I couldn’t figure out how to overcome this problem. Finally I used a heatsink from a salvaged ATX PSU and I attached it onto the upper surface of that IC having previously applied an aluminum based thermally conductive compound on it.
For doing this, I had beforehand to remove two small electrolytic caps from the upper components’ side and solder them on the solder side of the main board in order to have all the upper space available for the heatsink attachment.
You can see the heatsink in the photo below. The processor is underneath, at the right side of the cable connector shown, almost at the middle of the PCB. I attached it using three tinned copper wire retainers soldered directly on the chassis around it.
Now if you ask me why this IC overheats so much or if this problem revealed itself after the previous failure or if it was there from the very first moment of the operation of the set not being observed, I really cannot give you a reliable answer.
The important thing is that for more than six months since I returned the set to my friend, including the very hot summer months, I have no “negative feedback” from him and therefore I consider I resolved the problem mechanically, hopefully for a long time to come!
This article was prepared for you by Paris Azis from Athens-Greece. He is 59 years old and has more than 30 years’ experience in electronics repairs, both in consumer and industrial electronics. He started as a hobbyist at the age of 12 years and ended his professional carrier as a senior electronics technician. He has been a specialist in the entire range of consumer electronics repairs (: valve radio and BW TV receivers, transistorized color CRT TV, audio amps, reel and cassette tape recorders, telephone answering and telefax devices, electric irons, MW cooking devices e.t.c) working in his early stages at the official service departments of National-Panasonic first and JVC afterwards, at their premises in Athens.
Then he joined the telecoms industry, working for 20 years as field supporting technician in the sector of DMRs (: Digital Microwave Radio transmission stations), ending his carrier with this subject. Now he is a hobbyist again!
Please give a support by clicking on the social buttons below. Your feedback on the post is welcome. Please leave it in the comments.
P.S- If you enjoyed reading this, click here to subscribe to my blog (free subscription). That way, you’ll never miss a post. You can also forward this website link to your friends and colleagues-thanks!
Note: You can check out his previous repair article below:
https://www.jestineyong.com/paco-der-2000-automatic-voltage-regulator-repair/


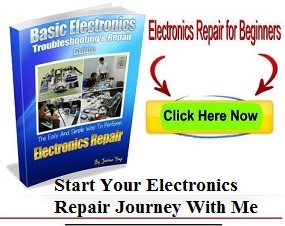
Gopal Sharma
September 26, 2015 at 1:26 pm
Nice repair technique Mr. Paris Azis. Thanks for sharing.
Paris Azis
September 27, 2015 at 9:10 pm
Hello Gopal
Thank you very much.
Best Regards
Mark
September 26, 2015 at 2:34 pm
Hey Paris, thanks for your article. Sometimes to carry out a repair, we have to 'think outside the box'. A simple solution for an otherwise complex issue.
Well done!
Paris Azis
September 27, 2015 at 9:26 pm
Hello Mark
You are right. That's why I always insist on the idea that a technician must use all of his (or her) imagination power in order to come up with the better possible resolution to the problem he/she faces instead of being forced to quit the repair or end up in the worst case scenario, namely to return the defective device to its owner in an irreparable condition for any other capable thechnician who might try to repair it (due to the damage he/she caused to it following either ineffective methods, or improvising with it with no method at all)...
Best Regards
Albert van Bemmelen
September 26, 2015 at 4:32 pm
Hi Mr. Paris, well done! Your article is written in clear and perfect English however this part did make me wonder: " I found a similar IC and I guess that both of them are produced from the same company. The type of the one I found was MST 776-1 while the one I searched for had more and different digits after the first 77. Unfortunately I didn’t take a photo before the repair so that you could see this I.C now. ". It kind of indicates that you also did exchange the original MST 776 I.C. by another one you found?
But since you probably only searched on the www and there found a similar type, I take it you only added the Cooler on top of the originally Bad working MST 776 without replacing it? Which was a great solution!
Paris Azis
September 27, 2015 at 9:50 pm
Hello Albert
I didn't find this I.C anywhere in order to replace it and see any difference (if there would be any).
Therefore I was forced either to use a 12V fan like the known types for P/C PSU units cooling, which would be an effective but nevertheless annoying solution due to the noise it produces especially during the night, or come up with another solution (which I did), or finally quit the case (which I never do if I don't consider in advance all the other possible options I may have, which usually leads me to reach and apply the proper solution).
Well, it happened to me many times up to now, this solution to be purely mechanical...
Thank you for your warm support!
Best regards
James
September 26, 2015 at 7:16 pm
Thanks for sharing this very practical solution for this TV problem Mr. Paris Azis.
Glad to know that you're with Panasonic before. I have used 4 Panasonic Box Fan in my home for several yrs and now all of them have a common problem --- The louver either stops ot turns very fast(about 4 time its normal rotation speed). I've opened one and checked its diodes and Capacitors' ESR and all seemed to be OK. I wonder if it is all due to the small motor that turns the louver through a rubber gear(the gear looks alright without any sign of wear of aging). If it is due to the motor, could you pls advise me its spec and also where I can order/buy several replacement motors? (I've called the panasonic service center here in Hong Kong but they said they only provide repair service and do not sell any spare parts)
It would be best if you can have an article sharing how to fix this kind of fan problems.
Thank you!
Paris Azis
September 27, 2015 at 11:31 pm
Hello James
First of all I was working as a Panasonic service technician before 1986. Unfortunately at that time there were no such box fans in production and therefore I cannot give any straight answer to your problem. We had only the classic types of fans, where their speed changing was based upon tapping their internal windings connections and of course there was no louver at all installed on them.
In your case anyway, since there are electronics involved in the speed regulation process, if I were in your shoes, I would first start with checking the rotating mechanism itself. Then, if everything would prove to be in proper operating condition, I would go to the electrical part. In this stage I would try to locate the problem by separating the motor from its circuitry and feeding it directly with power for a given speed. Then I would have the picture of the problem clear. If the motor would work steadily in constant speed, then the problem would obviously be hidden in its electronics. Now, given that you have already done some essential tests, I believe that you are very near to the solution you seek…
The only failure I strongly remember with these fans is that either after extended operation of them or especially at their first try to operate them at a new summer season after being left standing for almost one year, the rotors of their motors were stuck due to the grease used to lubricate the rotor axle within the (sleeve or ball-) bearings having become in a petrified condition. The problem was every time eliminated by thorough cleaning and re-lubricating those bearings. There was no electrical failure with their motors whatsoever
Thank you for your good words.
Best Regards
James
September 26, 2015 at 7:28 pm
When the louver(s) stop, it just stalls, it will rotate again(but at 4X speed) if I give the louver a push/turn.
Yogesh Panchal
September 26, 2015 at 8:26 pm
Good job sir, thanks for sharing.
Paris Azis
September 27, 2015 at 9:54 pm
Hello Yogesh
You are always welcome.
My Best Regards to you as well.
Zed Pato
September 27, 2015 at 12:35 pm
nice technique sir!!!!
Paris Azis
September 27, 2015 at 9:56 pm
Hi Zed
Thank you too.
Best Regards
Robert Calk
September 27, 2015 at 4:22 pm
Good job, Paris. Were you touching the IC's checking their temperature while the unit was on?
Paris Azis
September 27, 2015 at 10:22 pm
Hello Robert
I simply put momentarily my finger on the upper surface of this “post stamp” chip. This was the only place available to measure temperature as there was no heatsink on it before I put the one.
As a following test, I measured the magnitude of the temperature by using the method already described in the article.
Best Regards
Ulises Aguilar Pazzani
September 28, 2015 at 11:55 am
Great Jb Sir
Paris Azis
September 28, 2015 at 3:55 pm
Hello Ulises
Thanks for your support.
Best Regards
James
October 1, 2015 at 4:26 pm
Hello Paris,
Thanks a lot for your valuable advise.
I will check the motor separately to identify whether it is the motor problem(e.g., needs lubrication) or electrical problem first.
In the past few days, I've also read some articles about fan motor speed problems, and nearly all of them trace back to a 0.xxuF 3XX volt cap. I think I might have overlooked the several 0.XX uF 3XX volt big mylar caps in my last trouble-shoot (because the ESR meter only target at bigger eCaps and are less effective in detecting small (0.XX uF) caps), I think I will de-solder those 0.XX uF caps and check their capacitance. I think if the problem is not due to the motor, then those caps will be the most probable cause.
Thanks again for your advise and look forward to reading more articles from you and learn from you.
Beat regards,
James
Robert Calk
October 1, 2015 at 7:41 pm
Hi James,
I was thinking maybe you have a bad cap or two also. You need to get an insulation tester to help find bad ceramic, mylar & etc caps. In my article, " Lights of America Shop Light Repaired", I found a bad cap with my insulation tester that checked good on capacitance. What the insulation tester showed was that under voltage the cap was acting like a resistor. That's why we need to check caps at high voltage because if they leak they behave like a resistor in the circuit.
Paris Azis
October 8, 2015 at 12:45 am
Hello James
I think I saw similar failure cases in the web, with those mylar caps defective. Anyway, keep in mind that you can use very safely your ESR meter down to 0,1μF, provided that your meter can measure up to 100 Ohms ESR. The only thing you need is a reference table. You can make your own table by buying a new set of them, starting from this value above and ending in 1μF. Once the table is available, you can go on with testing. No problem at all. I test all bipolar caps down to 0,1μF. This is the down limit, only because the meter cannot measure above 100 Ohms ESR!
Best Regards
Paris Azis
October 8, 2015 at 1:08 am
P.S James,
You can also follow Robert’s advice for a full test of these caps.
If you don’t have an insulation tester is not a problem. You can always rectify the mains voltage and then connect the capacitor under test with a 3 Watt (max). incandescent lamp, then feed it with the rectified d.c voltage and see if the lamp lights even barely but permanently. The normal function is to see some light, but momentarily (until the cap is charged). The smaller the power of the lamp, the better the sensitivity of your test is.
The best of course (preferably after the visual test) would be to connect a d.c mA meter in series with the cap/lamp circuit and see if there is any current flow. If there is, then you have a problem with the cap under test. Simple isn’t it? (Keep your eyes open when working with high voltage anyway)!!
B.R