Membrane Keypad Replaced With Micro Switches In ONIDA Microwave Oven
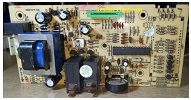
This Onida Power Grill 21 Microwave oven belonged to my younger brother. He brought it to me with the complaint that it was getting on, but not heating up. As they sparingly used this, it was lying in this condition for several months in their house, before it was finally moved to this “in-house-workshop.”
As usual, my first duty was to clean the inside thoroughly, which I did. Found a lot and lot of cockroach excretions and eggs! Found eggs laid even inside the connector pin of high voltage capacitor!
On checking, I found that it was getting on, but none of the switches were getting pressed. It was like stone! No response on pressing any of the controls. Result of dumping it in one corner, and allowing it to be a cockroach haven! Anyhow, I continued my investigation, after disconnecting the power and discharging the HV Cap. First check was door switches and found these to be ok. The temperature sensor was also ok. If the precaution switches as well as sensors are ok, ‘No heating up’ problem in any microwave oven usually starts with blowing of High Voltage Fuse, HV Diode leaky, Capacitor short or failure of its main part, the Magnetron etc. I checked the magnetron using Analogue Multimeter and found the filament showing 3 Ohm resistance, and no leak from filament to ground in highest ohms range. Then checked the Diode and found it to be ok, as it showed no reading from both directions. Removed the securely housed High Voltage Fuse and found it to be blown: (The first picture below is after removing the magnetron for visual inspection of any crack, burnt mark or any such visually detectable defects. The magnetron was fit back before further investigation.)
It was a 5KV, 0.7A Fuse. I got one from one of my technician friends, which was 5KV, 0.65A. Before putting it in, I placed a thin Linz wire removed from shield of a shielded cable, shorting the blown fuse. Removed the connectors from the primary of the HV transformer and applied 230V directly, after ensuring that the door was closed (to avoid exposure to radiation). It stayed put, indicating that there was no short down the line. So disconnected and discharged the cap and replaced the fuse with the one that I got from my friend.
As no controls were working, I removed all the connections from the front panel and removed the PCB as well as the control panel keypad. Found a lot more cockroach eggs securely bonded in all the available crevices. Appreciating and admiring its ingenuity, cleaned all of them thoroughly. Found the PCB in very bad and dirty condition. Cleaned it up thoroughly. Did a dry solder patch up from one end to another. Replaced the electrolytic capacitors. Turned my attention to the membrane keypad. Found that the carbon coating on the edges of the connector had worn out. In fact it was falling off by itself, showing its poor quality. (This keypad was replaced a couple of years’ back by the company technician due to similar complaint ‘no response’) Made enquiries for a direct replacement. The price quoted was exorbitant. Hence with the consent of the user, I decided to provide micro switches. Here are a few pictures of the panel, the microcontroller IC used, the part number of the membrane keypad, the keypad itself, and the membrane pealed into two (top and bottom) to study its connections.
Tried stapling the end to overcome worn out carbon layers, but still it was not showing continuity, as the thin layers had cut tracks.
Four tracks came out from the bottom and four from the top of the membrane keypad (which you can see as marked in the above pictures.) Gave numbers of the connection pins, 1 to 8 from bottom to top. Drew a diagram of top and bottom connections manually and looking at the front panel, prepared a matrix in the computer before starting the connections of micro switches. Drilled holes for the switches through the front panel sticker, selecting a suitable place, which will not prevent reading of description below or seeing the symbol printed above. Marked the numbers on the inside of the panel. Wired the inter connections as per diagram. Then connected 8 PIN relimate connector.
While giving the connections we need to mark the numbers of switches in the same order as in the diagram, i.e., in the diagram, it is from right to left, but on the back side of the panel, it should be written from left to right. Otherwise the connections will go wrong! In fact, I corrected the numbers written on the other side of the panel, after noticing the error! That’s why I am mentioning it here for those who might attempt to do it! After insertion of each micro switch, I bent the left leg to top and right leg to bottom, so that I can segregate the top and bottom connections to match with the membrane keypad. After wiring, I had even marked the connection pin numbers for easy wiring of the relimate connector. While soldering the legs of the switches, I pressed it down to the plastic base for proper bonding and to avoid a shake while being operated. Now have a look at the pictures:
Incidentally I noticed that the colours of the wires in the new connector was following the colour codes commonly used for Resistors, i.e., black for 0, brown for 1 etc.. So, it was helpful when I connected the ends to the panel. (The manufacturer could have avoided the black and started with brown!) Replaced the existing connector with a relimate 8 pin connector on the PCB:
In this microwave oven, there was no feedback from any of its loads, which the uController IC senses as a protection or adjustment and there was no pulse generation based on any such feed backs. Probably, all microwave ovens are designed like this. The 230V AC connection is controlled by two relays, one for the oven and another for the grill coil, which gets activated based on our selections, but wired through on/off (Door open/close) switches for safety purposes. The job of the uController was just to switch the relay on and off based on pre-programmed time. So, I gave 230V AC to the input of the step-down transformer on the PCB and tried the switches. It was working perfectly and matched with the displays.
So, fixed the panel back and put back the covers too. Fixed a cellophane sheet on top of the panel to avoid exposure to moisture making it tight enough but not to press down any of the switches. Used cellphane tapes on the sides to avoid water seepage when controls are used with wet fingers. Unlike the membrane switches, these micro switches can get easily rusted/shorted due to moisture. Tried the oven once again for heating up a cup of water and frying an Appalam (Pappadom) made by my wife from Tapioca. (https://www.thefreedictionary.com/Appalam)
Cleaned all the sides of the oven, including the three pin top and cable, and made it shine like new. Here is a picture of it and that of the parts replaced:
(My sister-in-law called me up while writing this article and thanked me for the special care taken and also to say that she was very happy with the micro switches and found it very easier! She was in total praise of the cleaning work done by me!) Thus a very satisfying and enjoyed job got rocketed to the ever gulping ‘satisfaction bag’! (Ha! Ha! What a thrill!)
This article was prepared for you by Parasuraman Subramanian from India. He is 69 years old and has more than 30 years’ experience in handling antique equipment like Valve Radio, Amps, Reel Tape Recorders and currently studying latest tech-classes conducted by Kerala State Electronics Technicians’ Association. He has done graduation in BBA degree, private diploma in Radio Engineering and retired as MD of a USA company. Presently working as Consultant to Hospital and other institutions.
Please give a support by clicking on the social buttons below. Your feedback on the post is welcome. Please leave it in the comments.
P.S-If you enjoyed reading this, click here to subscribe to my blog (free subscription). That way, you’ll never miss a post. You can also forward this website link to your friends and colleagues-thanks!
You may check on his previous repair article below:
https://jestineyong.com/restored-a-philips-radio-that-got-spilled-with-dosa-batter/


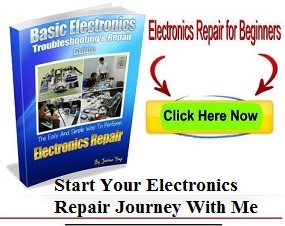
Fernando andales
May 29, 2019 at 9:09 am
I would like to thanks for new idea mr parasuraman unending support.
Thank you very much.
Robert Calk Jr.
May 29, 2019 at 9:57 am
Good job, Parasuraman! Another great lesson of improvisation!
Devon Wilson
May 29, 2019 at 10:10 am
Thanks for sharing. That must have been time consuming and tedious. Be aware that you can get electrocuted by leakage microwave energy even when the door is closed.
Gregor M Brettelle
May 29, 2019 at 11:35 am
Nice thorough article and very creative ... the worst part ... those roaches - yuk!!
Thanks for posting.
Albert van Bemmelen
May 29, 2019 at 1:39 pm
Another well done repair in the satifactory bag! How you fixed a cellophane sheet on top of the panel to avoid exposure to moisture is not clear but that mustn't have been easy either I imagine? And being Dutch I learned a new word today about the 'relimate' plug you used.
Parasuraman Subramanian
May 30, 2019 at 9:52 am
First of all measured the width and length of the cellophane paper required to cover the keypad. Then fixed the top with a cellophane tape, ensuring no wrinkles. Then slowly spread it down applying just the pressured required to remain tight enough, but not pressing down any of the buttons. Then fixed a tape at the bottom. Then slowly did the same from left to right. By luck of the customer as well as mine, as one can say, the fixing was perfect at the first attempt itself! As I have observed guys fixing mosquito prevention grills with Velcro on the windows in my house, I followed more or less the same method.
Waleed Rishmawi
May 29, 2019 at 2:08 pm
a very detailed successful repair. a big congrats is in order. i like the button idea. I never faced such challenge and i do in the future, I know what to do. thanks a lot
Mario
May 29, 2019 at 2:15 pm
Hi!
Your idea is *good*, and the way you realized is also interesting! Your fighting against the e-waste is very appreciable! Bravo!
Luciano Khware
May 29, 2019 at 2:30 pm
Great Job sir, You always inspire me with your electronics repair articles
Regards!
AdamS
May 29, 2019 at 4:28 pm
An ingenious and intricate repair. Parasuraman, you are a craftsman!
Henrique J. G. Ulbrich
May 29, 2019 at 6:03 pm
Excellent, dear Parasuraman. A work done with patience and dedication. You are right when you say that microswitches suffer from moisture. Some months ago I had to replace two microswitches in my bathroom scale; they were affected by the moisture normally present in this ambient.
Ghashaan
May 29, 2019 at 8:46 pm
I'm gonna keep this article for later reference. I love appliance repair. Your solution is very creative and I'm glad that it proved to effective.
Martin Moises Rojas
May 29, 2019 at 9:46 pm
muy buen trabajo
=============
Very good work
Parasuraman Subramanian
May 30, 2019 at 9:38 am
Many thanks to one and all for your encouraging comments! May God Bless You all!
James
May 31, 2019 at 1:30 pm
Yea, gots to love us some cock roaches yo' :[) LoL
James
May 31, 2019 at 1:44 pm
Wow man'! that's a $300 engineering job and a half, personally I would of just bought them a $20 used microwave oven from the pawn shop :[) LoL, but that's some master crafstmanship''''''''
Mark Tembo
June 4, 2019 at 7:55 pm
This is quite interesting for because I do such jobs, i.e. replacing membranes on POS/ cash register machines. I have been looking for the manufacturer of such membranes, especially in China. Any one there who has such information?
Thanks!
ulises Aguilar pazzani
August 5, 2019 at 11:08 am
good Job Mr Parasuraman. You are good with microwaves